نورد سرد فولاد مبارکه، شتابدهنده صنعت خودرو
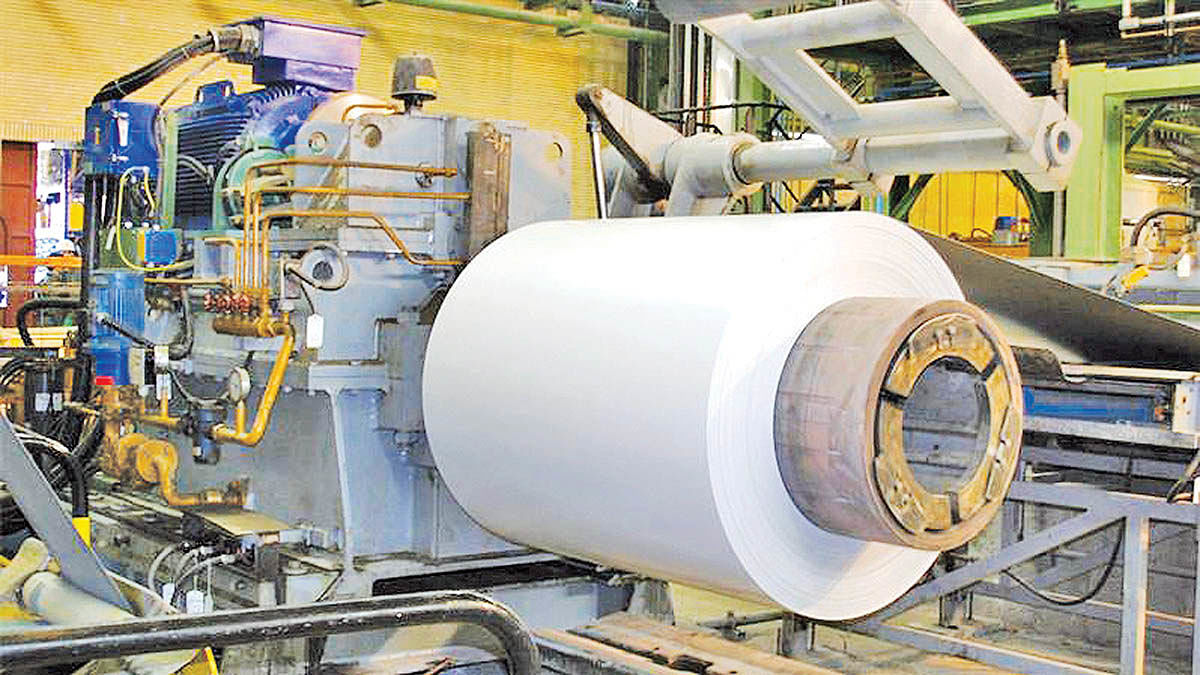
بهزاد بهادرانی، مدیر ناحیه نورد سرد و اکبر نادری درباغشاهی، رئیس خطوط آنیلینگ و شستوشوی الکترولیتی در گفتگویی به تشریح این موضوع پرداخته اند که در ادامه می خوانید مجری برنامه رادیو فولاد به این موضوع پرداختهاند که در ادامه میخوانید.
بهزاد بهادرانی، مدیر ناحیه نورد سرد در مورد تاثیر تبدیل روش HNX به هیدروژنی بر کیفیت ورقهای تولیدی و گریدبندی آنها می گوید:
نیاز خودروسازان هر روز گسترش پیدا میکند و با نیاز یک تا دو دهه پیش کاملاً متفاوت است. ما سعی کردیم این موضوع را بهموقع پاسخ بگوییم و با تبدیل فرایند HNX به H۲ توانستیم بخشی از نیازهای خودروسازان را تأمین کنیم. هرچند در این سالها سعی کردیم بهطور متوسط دو تا سه گرید جدید را در ناحیه نورد سرد تولید کنیم که یکی از نقاط کلیدی برای رسیدن به این گرید فرایند آنیلینگ و کیفیت خطی این ورق است که محقق نخواهد شد، جز با فرایند H۲ که خوشبختانه با ایجاد ۱۶ پایه این امر تا حدودی انجام شده است. منتهای مراتب، این موضوع پایانی ندارد و ما دنبال این هستیم که بتوانیم گریدهای دیگری را که الآن نیاز خودروسازان است از طریق بهبود فرایندها در بحث آنیل پیوسته انجام دهیم.
ما با نگاه به آینده و با حمایت مدیریت عالی شرکت درصددیم یک خط آنیل پیوسته را در پلنت موجود ایجاد کنیم. اگرچه در طرح توسعه ناحیه نورد سرد خوشبختانه یک پلنت آنیل پیوسته هم دیده شده و قطعاً با اجرای آن طرح، گستره وسیعی از نیاز خودروسازان و شاید همه نیازهای آنان را رفع میکنیم و گام بلند دیگری در مسیر خودکفایی برخواهیم داشت.
اکبر نادری درباغشاهی، رئیس خطوط آنیلینگ و شستشوی الکترولیتی هم در این رابطه به چالش های پیش روی پروژه بومیسازی ۱۶ پایه هیدروژنی در نورد سرد و واحد باکسآنیلینگ اشاره می کند و می افزاید:
برای اجرای این پروژه باید بالغبر ۲ هزار ردیف قطعه در بخشهای برق، مکانیک، هیدرولیک و پنوماتیک نصب میشد. در نخستین گام، تأمین این قطعات حائز اهمیت بود. رویکرد اصلی سازمان این بود که از محل تأمین داخل و بومیسازی این کار انجام شود. این ۲ هزار ردیف قطعه تقریباً ۲۲ هزار عدد قطعه را تشکیل میدادند که خوشبختانه حتی برخی قطعات خاص با لحاظ کردن پارامترهای کیفی آمادهسازی و نصب شد.
او با اشاره به نیاز برای ورقهای عریض و ویژه در ساختن پایه آنیلها یکپارچه اضافه کرد:
یکی از مهمترین قطعات این پروژه خود پایه آنیلینگ بود که تکنولوژی ساخت آن در انحصار برخی شرکت خارجی نظیر اتریش، آلمان و چین بود و فولاد مبارکه برای اولین بار میخواست پایه آنیل بسازد. به همین منظور از پایههای موجود یک متالوگرافی انجام دادیم، ورق را مهندسی معکوس کردیم و در نهایت از این طریق مشکل تأمین ورق را حل کردیم. همچنین موتورهای الکتریکی و ایمپلر پایه دو قطعه فوقالعاده حساس بودند. موتورهایی که در پایه هیدروژن کار میکنند دور خیلی زیادی دارند و در دمای ۷۰۰ درجه کار میکنند. بهطورکلی این پروژه با انسجام و همدلی بین همکاران و واحدهای مختلف ازجمله خرید و بومیسازی، با موفقیت به پایان رسید.
اما از جمله مهمترین چالشهای این پروژه، کار با گاز هیدروژن است، نادری باغشاهی در این مورد نیز می گوید:
وقتی قطعات و تجهیزات تماماً ساخته و در محل مونتاژ شدند، موضوع راهاندازی مسئله اصلی ما شد. به همین منظور، باید واحدِ در حال کار را متوقف و قسمتی از آن را دمونتاژ و قسمت جدید را نصب و راهاندازی میکردیم. مهم این بود ما بتوانیم آن را راهاندازی کنیم. گاز هیدروژن گاز فوقالعاده خطرناکی است و میتواند آتشسوزی ایجاد کند. برای پیشگیری از بروز هرگونه حادثه، تصمیم گرفتیم پایهها را یکییکی راهاندازی کنیم. روی کاغذ نمیتوانستیم تضمین بدهیم، ولی باور داشتیم این کار را میتوانیم انجام دهیم. سناریو این بود که پایهها اول با گاز نیتروژن راهاندازی شود و بعد از اینکه مطمئن شدیم تمام فرایندها درست کار میکنند گاز هیدروژن را زیر پایهها بگذاریم و با همین سناریو تمام ۱۶ پایه بدون هیچ مشکل و حادثهای راهاندازی شد.
با توجه به تغییرات در حوزه فناوری ، آنیلینگ هم از این حوزه مستثنی نیست، باغ شاهی می گوید:
ما موظفیم خودمان را بهطور مستمر بهروز کنیم تا فولاد مبارکه همچنان سرآمد بماند. آنیل جعبهای که سال ۱۳۹۶ انجام شد تکنولوژیای مربوط به همان ۱۰ سال پیش بود و ما در آن تکنولوژی، کلافها را بهصورت جعبه و بهصورت بسته آنیل میکنیم. نیاز امروز بازار، ورقهای با کیفیتِ بهتر است و این کار محقق نمیشود، مگر اینکه ما یک آنیل پیوسته داشته باشیم. طرحها همه آماده است و در طرح توسعه نورد سرد یک آنیل پیوسته دیده شده است. طرحی را دنبال میکنیم که در همین سایت آنیلینگ بتوانیم یک آنیل پیوسته با ظرفیت ۲۰۰ هزار تن راهاندازی کنیم تا بتوانیم نیاز بازار کشور را برآورده سازیم.