معرفی فرآیندهای احیای مستقیم در تولید فولاد
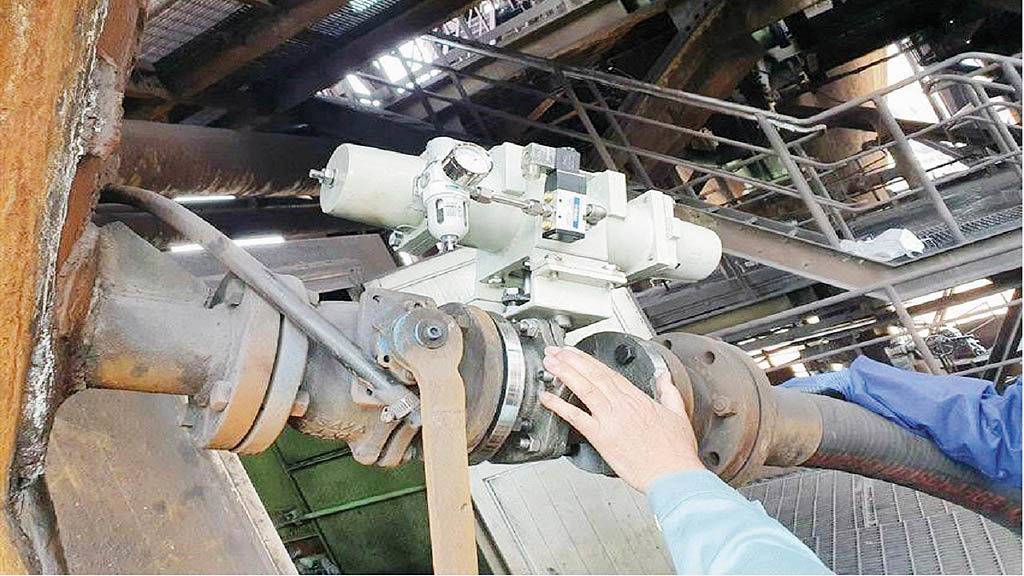
تقریبا ۷۵ درصد از کل آهناسفنجی تولیدی در جهان با دو روش میدرکس و اچوایال تولید میشود. امروزه بیشتر تولید فولاد در دنیا به دو روش کوره بلند- کنورتور و احیای مستقیم – ذوب الکتریکی اختصاص دارد که روش دوم به طور قابل توجهی در حال توسعه و پیشرفت است. فرآیند تولید فولاد بر پایه احیای مستقیم – ذوب الکتریکی شامل دو مرحله تولید آهناسفنجی و سپس تبدیل آن به فولاد در کوره قوس الکتریکی است. در روش احیای مستقیم، ذرات اکسیدی آهن در تماس با گازهای احیاکننده شامل H۲، CO و CH۴ در دمای ۷۵۰ تا ۹۰۰ درجه سانتیگراد احیا شده و به آهناسفنجی تبدیل میشوند.
آهناسفنجی معمولا دارای بیش از ۹۰ درصد آهن به صورت فلزی است که میل زیادی به ترکیب شدن با اکسیژن دارد. برای تهیه آهن، باید ناخالصیهایی مانند اکسیژن را توسط احیای شیمیایی از سنگ آهن حذف کرد. روشهای متفاوتی برای تولید آهن وجود دارد. عمده این تولید توسط فرآیند کوره بلند انجام میشود. در کوره بلند سنگآهن همراه با کک به عنوان عامل احیاکننده پس از طی فرآیندهایی وارد کوره شده و به صورت آهن مذاب کربن دارد خارج که در نهایت این آهن مذاب در کانورتر به فولاد تبدیل میشود.
برای سالهای متمادی کوره بلند یکی از مهمترین و کارآمدترین روشها در زمینه تولید آهن بوده و در حال حاضر نیز بیش از ۹۰ درصد آهن مورد نیاز در جهان را تامین میکند. فرآیند تولید آهن توسط کوره بلند از نظر نرخ تولید؛ بازدهی بالایی دارد، اما نیازمند مواد خام باکیفیت است. آهن در کوره بلند توسط احتراق کک تولید میشود و با توجه به کاهش منابع زغالسنگهای ککشو، قیمت کک در حال افزایش است. همچنین مراحل آمادهسازی مواد اولیه این فرآیند مانند کلوخهسازی، ککسازی و سینترینگ هزینه بالایی را بر صنعت فولاد تحمیل میکنند.
در نتیجه میتوان گفت کوره بلند به دلیل مشکلات اقتصادی و زیستمحیطی ناشی از بهکارگیری کک و سینترینگ در صنعت فولاد آینده نامشخصی خواهد داشت. بنابراین با توجه به وجود منابع عظیم زغالسنگ ککنشو در جهان، هزینههای بالای مراحل آمادهسازی و اهمیت روزافزون مسائل زیستمحیطی گرایش به سمت روشهای جدید و جایگزین در این زمینه روزبهروز بیشتر میشود. یکی از این روشها، تولید آهن توسط فرآیند احیای مستقیم است. در این گونه فرآیندها، تعدادی از مراحل آمادهسازی حذف شده و در نتیجه هزینهها و آلودگیهای مربوط به کل فرآیند به صورت قابل توجهی کاهش مییابد.
فرآیند احیای مستقیم یکی از روشهای نوین برای تولید آهن است که در آن بدون استفاده از فرآیند ککسازی یا حتی در برخی موارد بدون کلوخهسازی، آهن تولید میشود. احیای مستقیم اکسیدهای آهن توسط کربن در دهههای اخیر به صورت گستردهای بررسی شده است. هزینههای سرمایهگذاری، راهاندازی و نگهداری فرآیند احیای مستقیم در مقایسه با سایر روشهای موجود بسیار کمتر بوده و میتوان از آن در واحدهای کوچک فولادسازی با توجیه اقتصادی مناسب استفاده کرد. همچنین این روش برای بسیاری از کشورهای در حال توسعه که با کمبود منابع زغالسنگ ککشو و باکیفیت روبهرو هستند، گزینه بسیار مناسبی است.
تقسیمبندی فرآیند احیای مستقیم
در بیش از سه دهه اخیر، فناوری جدیدی به نام فرآیند احیای مستقیم برای احیای سنگآهن به فلز آهن با استفاده از زغالسنگ ککنشو یا گاز طبیعی طراحی شده و به طور گستردهای توسعه پیدا کرده است. مسائل اقتصادی و اثرات زیستمحیطی زمینه و انگیزه لازم را برای تحقیق و مطالعه پیرامون این فرآیند به وجود آوردهاند. فرآیند احیای مستقیم در دماهای پایینتر از دمای نقطه ذوب، اکسیژن موجود در سنگآهن را حذف میکند و ساختار آن را به صورت متخلخل اسفنجی شکل در میآورد. به همین دلیل این محصول با نام آهناسفنجی شناخته میشود و معمولا حاوی ۹۲ تا ۹۶ درصد آهن خالص است. از آهناسفنجی میتوان برای مثال به عنوان ماده خام برای تولید فولاد در کوره قوس الکتریکی استفاده کرد.
فرآیند احیای مستقیم براساس نوع احیاکننده مورد استفاده، به طور کلی به دو گروه تقسیمبندی میشود.
-فرآیندهای احیای مستقیم بر پایه زغالسنگ که در آنها از یک احیاکننده کربنی، معمولا زغالسنگ استفاده میشود.
-فرآیندهای احیای مستقیم بر پایه گاز، که در آنها از احیاکننده گازی استفاده میشود.
انتخاب یکی از دو روش به محل قرارگیری کارخانه تولیدکننده و منابع موجود در دسترس بستگی دارد. در فرآیندهای نوع اول معمولا زغالسنگ ککنشو به عنوان عامل احیاکننده به کار میرود. از جمله فناوریهایی که از این روش برای احیا استفاده میکنند، میتوان به فرآیندهایی بر پایه کوره دوار مانند SL/ RN و فرآیندهایی بر پایه کوره بستر دوار نظیر «فستمت» اشاره کرد. عدم نیاز به استفاده از زغالسنگ ککشو و باکیفیت، هزینههای پایین راهاندازی و نگهداری، دمای پایین عملکرد نسبت به کوره بلند و صرفهجویی در انرژی از جمله مزیتهای این روشها هستند. در فرآیندهای نوع دوم، معمولا از گاز طبیعی برای جداسازی اکسیژن از اکسیدهای آهن استفاده میشود.
این فرآیندها در مناطقی که منابع گاز طبیعی با قیمت مناسبی وجود دارد نسبت به فرآیندهای بر پایه زغالسنگ ترجیح داده میشوند. همچنین آلودگی ناشی از آنها کمتر است. از جمله روشهای رایجی که در آنها از احیاکننده گازی استفاده میشود، میتوان به فرآیندهای میدرکس و اچوایال اشاره کرد. امروزه بیش از ۸ درصد آهن مورد نیاز در جهان از طریق فرآیند احیای مستقیم به کمک زغالسنگ به دست میآید. با این حال تحقیق و بررسی در این زمینه جهت افزایش بازده، کاهش مصرف انرژی، بهبود کیفیت محصول و در کل ارتقای فرآیند احیا همچنان به صورت گستردهای ادامه دارد.
استفاده از فناوری پرد در واحدهای احیای مستقیم
احیای مستقیم به روش پرد (PERED) فناوری ایرانی است که گندلههای اکسید آن را به آهن فلزی یا همان آهناسفنجی تبدیل میکند که برای فولادسازی باکیفیت بالا مفید است. کوره احیای استوانهای از یک جریان فرآیند پیوسته با بازدهی بالا استفاده میکند.
اکسید آهن از مخزن تغذیه کوره احیا توسط نیروی جاذبه و از طریق یک لوله عایق شده توسط گاز آببندی به لولههای توزیعکننده و از آنجا به کوره احیا شارژ میشود. در کوره گندلهها در اثر نیروی وزن و با کمک فیدر ارتعاشی به سمت پایین حرکت کرده و توسط تماس مستقیم با جریان مخالف گازهای احیاکننده در منطقه احیا، به فلز آهن تبدیل میشود. کوره استوانهای به سه منطقه با سیستم گاز مجزا تقسیم میشود: منطقه بالایی برای احیا، منطقه انتقال برای کربندهی و منطقه پایینی برای خنک کردن. فناوری پرد که توسط شرکت «امامای» در ایران ابداع شده در بیشتر واحدهای هشتگانه فولاد از جمله فولاد بافت به کار گرفته شده است.