«شرکت بابک مس ایرانیان» در مسیر توسعه
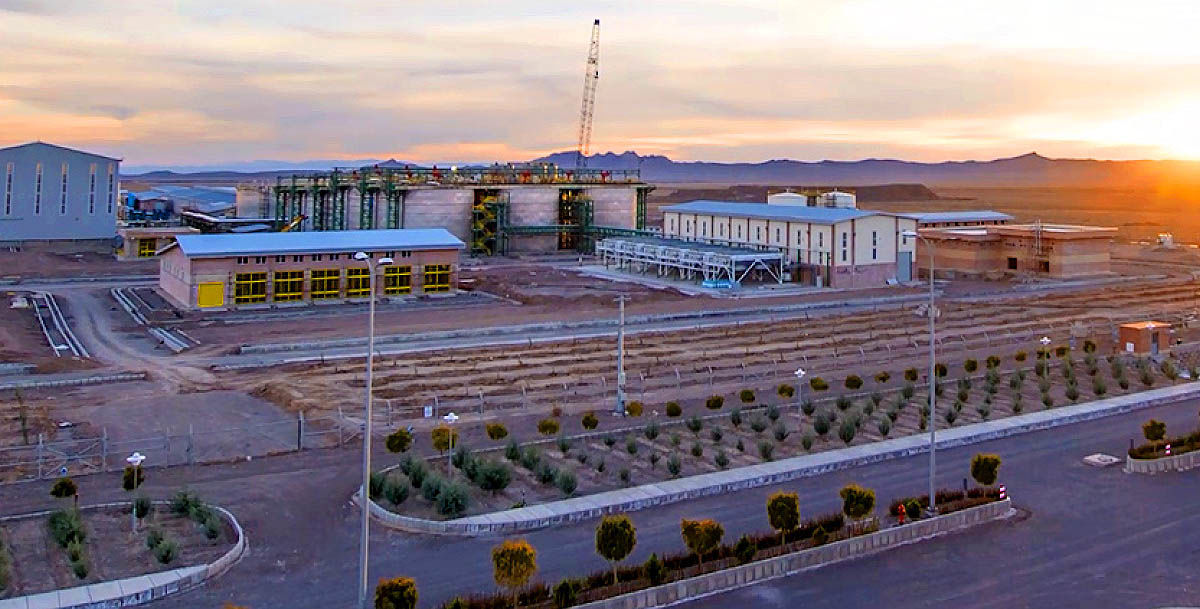
زمینه فعالیت شرکت
زمینه فعالیت شرکت با محوریت معدن و صنایع مس است که عمده آن به شرح ذیل است:
- پیجویی، اکتشافات، طراحی، تجهیز و استخراج از معادن مس
- ایجاد، راهاندازی و بهرهبرداری کارخانجات فرآوری مس و واحدهای مربوطه
- انجام عملیات فرآوری مس با روشهای مختلف
- احداث واحدهای مربوطه و صنایع وابسته و توسعه هرچه بیشتر و بهینه صنعت مس
- انجام هرگونه عملیات پیمانکاری مشتمل بر مشاوره، پیمان مدیریت، ارائه خدمات مهندسی در داخل و خارج از کشور که مرتبط با معدن و صنایع باشد
- انجام کلیه فعالیتهای بازرگانی اعم از خرید و فروش کالاهای وارداتی و صادراتی مجاز، تجهیزات، محصولات، مواد و مصالح مربوط به معدن و صنایع معدنی
- مشارکت و سرمایهگذاری در سایر شرکتها و مؤسسات مرتبط از طریق خرید یا به عنوان سهامدار
پروژههای در دست احداث
کارخانه تغلیظ معدن چاه فیروزه
این کارخانه ۱۰۱.۰۰۰ تن در سال کنسانتره مس با عیار ۲۵ درصد تولید میکند و در تاریخ ۳۰ فروردین ۱۳۹۷ راهاندازی شده است.
کارخانههای راهاندازی شده
- کارخانه تولید لوله مسی با ظرفیت ۱۲.۰۰۰ تن در سال
- کارخانه تولید کاتد مس (بیولیچینگ) با ظرفیت تولید ۵۰.۰۰۰ تن در سال کاتد مس با گرید A بورس فلزات لندن (LME)
جدیدترین فناوری روز دنیا
شرکت بابک مس ایرانیان مفتخر است که از جدیدترین فناوری روز دنیا در تولید لوله مسی به روش CAST & DRAW (چهارمین خط راهاندازی شده در دنیا) و پیشرفتهترین فناوری تولید کاتد در دنیا به روش بیولیچینگ (نخستین خط راهاندازی شده به این روش در دنیا) در تولید محصولات خود استفاده کرده تا گامی بلند در راستای استقلال و آبادانی کشور عزیزمان ایران بردارد. این شرکت با به کارگیری امکانات فوق، توانسته است محصولات لوله مسی خود را با بالاترین کیفیت روز دنیا تولید کرده و در همین راستا موفق به اخذ گواهی CE از موسسه TUV NORD آلمان شده است. همچنین با رعایت تمامی استانداردهای مدیریت کیفی، ایمنی و محیط زیستی موفق به ا خذ گواهی ISO۹۰۰۱، ISO۱۴۰۰۱ ، ISO۱۸۰۰۱ و استاندارد HSE-MS از موسسه SGS ایران شده است.
راهاندازی بزرگترین واحد تولید مس جهان توسط شرکت بابک مس ایرانیان
بزرگترین واحد تولید مس جهان به روش «بیوتانک لیچینگ» توسط شرکت بابک مس ایرانیان با ظرفیت اسمی 50 هزار تن مس کاتدی در 23 کیلومتری شمال شهرستان شهر بابک در استان کرمان به بهرهبرداری رسیده و مطالعات آزمایشگاهی، پایلوت و طراحی بخش فرآیندی آن توسط شرکتهای کانادایی صورت گرفته است. در این روش تولید کاتد مس با استفاده از میکروارگانیسمهای گرمادوست و از طریق انحلال کنسانتره مس سولفیدی در محلول اسیدی صورت میپذیرد. در ادامه با استفاده از روش مرسوم استخراج حلالی و الکترووینینگ، مس با کیفیت گرید A بورس فلزات لندن (LME) (با خلوص 99/ 99 درصد) تحت استاندارد ASTM B115 (2016) تولید میشود.
فرآیند تولید کاتد مسی
فرآیند تولید در این کارخانه شامل بخش اصلی آسیاب، انحلال و پسماند، خنثیسازی، SX و EW هستند. آسیاب کردن کنسانتره توسط دو دستگاه آسیاب عمودی صورت میپذیرد و باعث کاهش سایز ابعادی کنسانتره از قطر 40µ به µ15-10 میشود.
انحلال کنسانتره سولفیدی مس توسط باکتریها در محیط اسیدی با دمای حدود c°50 بوده و وظیفه اصلی باکتریها اکسایش آهن و گوگرد و انحلال اسیدی کانیهای اکسید شده مس و در نهایت تولید محلول سولفات مس PLS است.
سپس پس از تهنشینی پسماند فلزات با ارزش طلا و نقره و ... توسط دو دستگاه تیکنر و فیلترهای اولیه جداسازی انجام میشود. واحد خنثیسازی در این واحد PLS اولیه تولید شده توسط آهک با هدف تامین pH مناسب و حذف ناخالصیهای آهن توسط تانکهای خنثیسازی جهت فرآیند SX به تیکنرها و فیلترهای ثانویه ارسال میشود.
فرآیند واحد SX شامل 2 بخش است:
- بخش Extraction: جدایش یون مس از فاز آبی(PLS) به فاز آلی
- بخش Stripping: انتقال یون مس از فاز آلی به محلول الکترولیت و ارسال به واحد الکترووینینگ
- رسوب یون مس روی فولاد ضدزنگ با جریان برق مستقیم و تولید کاتد با خلوص 999/ 99 درصد با گرید A
مزایای استفاده از فرآیند بیوتانک لیچینگ کنسانتره مس در مقایسه با روش پیرو متالورژی
• قابلیت به کارگیری کنسانترههای مس با ترکیبات عنصری مختلف و بدون محدودیت در عیار ورودی.
• فرآیندی سازگارتر با محیط زیست و با میزان آلایندگی پایین؛ در فرآیند پیرومتالورژی مقادیر قابل توجهی گاز SO2 تولید میشود که باعث آلودگی محیط اطراف میشود. برای رفع این آلودگی، ساخت کارخانه تولید اسیدسولفوریک الزامی است، در صورتی که در این روش اسیدسولفوریک به عنوان ماده اولیه مصرف میشود.
• در مقایسه با پروژههای پیرومتالورژی، هزینه سرمایهگذاری در این روش پایینتر است (درحال حاضر احداث واحدهای ذوب و پالایش با ظرفیت کمتر از 200.000 تن در سال اقتصادی نیست).
• سادگی شرایط کنترلی عملیات و پایینتر بودن ریسک عملیاتی.
• در این روش مصرف کل انرژی شامل الکتریسیته و سوختهای فسیلی به شدت کاهش خواهد یافت.
• راندمان عملیات پیرو متالورژی در شرایط بهینه 92 درصد است، در حالیکه در این روش طراحی بر اساس راندمان 97 درصد انجام پذیرفته است.
• امکان بازیابی طلا (حدود 150 کیلوگرم در سال) و نقره از باطله تولیدی.
کارخانه لوله مسی
شرکت بابک مس ایرانیان در سال 1390 پروژه احداث خط تولید لوله مسی به روشCAST & DRAW (UP CAST)i را شروع و در سال 1394 راهاندازی اولیه آن را آغاز کرد. این روش جدیدترین و پیشرفتهترین روش تولید لوله مسی در دنیاست که با تغییرات فناوری ایجاد شده، فرآیند تولید لوله را کوتاهتر کرده و در نتیجه قیمت تمام شده کالا را کاهش میدهد. این کارخانه در زمینی به مساحت 6 هکتار و زیر بنای 10.000 متر مربع ساخته شده است.
تکنولوژی ریختهگری آن جز پیشرفتهترین تکنولوژیهای روز دنیا بوده که از شرکت UP CAST فنلاند و تجهیزات کشش لوله نیز از ASMAG اتریش خریداری شدهاند. با توجه به تکنولوژی پیشرفته، این کارخانه توان تولید لوله مسی با بهترین کیفیت و مطابق استانداردهای روز دنیا؛ بهخصوص استانداردهای بینالمللی ASTM B280، ASTM B75، ASTM B68 ، ASTM B743، EN12735، EN1075 و JIS H3300 ؛ جهت تأمین نیاز کامل صنایع داخلی و منطقه خاورمیانه را داراست.
فرآیند تولید لوله مسی
فرآیند تولید در این کارخانه شامل 3 بخش اصلی تولید شاه لوله به روش ریختهگری UP CAST، تولید لوله با قطر دلخواه توسط دستگاههای کشش و شکلدهی و در نهایت آنیل محصول توسط کوره آنیلینگ براق است.
ذوب و ریختهگری
تولید لوله مسی در این روش با ریختهگری توسط کوره UP CAST آغاز میشود. در این مرحله کاتد درجه A در کوره القایی 9 تنی ذوب شده و پس از آلیاژسازی مناسب با آمیژان مس-فسفر، مذاب به کوره القایی 7 تنی نگهدارنده منتقل میشود. پس از این مرحله، با روش ریختهگری سربالا (UP CAST) لولههای مادر (اولیه) با ابعاد OD38/ ID33 و OD52/ ID47 مستقیم ریختهگری شده و به سبدهای مخصوص منتقل میشوند.
کشش اولیه (Drawing)
قطر و ضخامت لولههای تولیدی در مرحله قبل، بر اساس طراحی فرآیند محصول، توسط دو دستگاه کشش 120 کیلو نیوتنی ساخت شرکت ASMAG اتریش کاهش مییابد.
آنیل میانی (Annealing)
به دلیل اینکه فرآیند کشش لوله در حالت سرد انجام میگیرد، تنشهای پسماند در لوله ایجاد میشود. بنابراین جهت آزادسازی این تنشها، لولههای کشیده شده از داخل کوره آنیل عبور کرده تا تنشهای آن آزاد و ساختار متالورژیکی لوله اصلاح شود. این کوره نیز ساخت شرکت ASMAG اتریش است.
کشش دورانی ( اسپینر بلاک - Spinner Block)
جهت سایز نمودن نهایی، لولههای کشیده شده در مرحله قبل به دو دستگاه اسپینر بلاک منتقل میشوند. تفاوت این دستگاه با دستگاه کشش اولیه در تعداد دفعات کشش بوده و توانایی تولید لولههایی با قطر 4 تا 30 میلیمتر با سرعت 1200 متر بر دقیقه را دارا است. این دستگاهها ساخت شرکت ASMAG اتریش هستند.
تراز پیچ (Level Winder):
پس از سایز نمودن لوله، لولههایی که بایستی به بازار عرضه شوند به این ماشین منتقل میشوند. در این مرحله کل سطح لولهها از دستگاه Eddy Current عبور کرده و بازرسی میشود. محلهایی که احتمال وجود عیب ظاهری وجود دارد، توسط دستگاه با رنگ علامتگذاری شده و در صورت نیاز توسط مشتری جدا میشود. تجهیزات خریداری شده برای این تست از شرکت FOERSTER آلمان که شهرت جهانی در زمینه ساخت تجهیزات تست غیرمخرب دارد، خریداری شده است. تست لوله در این دستگاه توسط دو دستگاه Defectomat (این دستگاه عیوب نقطهای را شناسایی میکند) و Rotating (این دستگاه عیوب خطی را شناسایی میکند) انجام میگیرد و تعداد این عیوب طبق استاندارد کنترل میشود. سپس لوله به صورت کویلهای 100-250 کیلوگرمی پیچیده میشود. تمامی تجهیزات این دستگاه نیز ساخت شرکت ASMAG اتریش هستند.
دستگاه تولید شاخه و پن کیک (Finishing)
در این دستگاه لولهها با توجه به سفارش مشتری، به شاخه یا پن کیک تبدیل میشوند. لوله توسط تجهیزات شرکت FOERSTER بررسی شده و در صورت شناسایی محصول معیوب، آن محصول به کلی از چرخه تولید خارج میشود. این دستگاه قابلیت تولید لوله شاخه تا طول 6 متر و لوله پنکیک از طول 15 تا 50 متر را دارا است و ساخت شرکت ASMAG اتریش میباشد.
بخش آنیل نهایی
در این مرحله لولههای کویل و پنکیک جهت بازیابی خواص فیزیکی و مکانیکی محصولات مانند قابلیت ماشینکاری، خواص الکتریکی، قابلیت سرد کاری و ایجاد سطحی براق، در کوره آنیلینگ نهایی تا دمای مناسب گرم شده و سپس در آن دما نگهداری شده و سرانجام با سرعت مناسب تا دمای محیط سرد میشود. در این کوره با خارج کردن گاز اکسیژن و دمیدن گاز نیتروژن و هیدروژن از اکسید شدن سطح مس جلوگیری میشود.
محصولات نهایی
در نهایت لولهها با توجه به سفارش مشتریان به 3 شکل لوله LWC (کویل)، Pancake(کلاف) و Straight (شاخه) تولید و به بازار مصرف عرضه میشود.
صنایع مصرفکننده عمده عبارتند از:
• صنایع برودتی و حرارتی
• صنایع لوازم خانگی
• لوله کشی آب و گاز
• رادیاتورسازی
• صنایع برق
• پانلهای خورشیدی
• صنعت خودرو
بازه ابعادی تولیدات لوله مسی
مشخصات فنی تولیدات لوله مسی در جدول روبهرو آمده است.
آلیاژ DHP حاوی ppm400-150 فسفر (040/ 0-015/ 0 درصد وزنی) بوده که دارای قابلیت خمکاری، کشش، جوشکاری، هدایت حرارتی بالا، مقاومت بالا در برابر خوردگی و تردی هیدروژنی است.
- فشار قابل تحمل لوله مسی (Mpa)
P: فشار هیدرواستاتیکی برحسب بار
(S (Annealed: تنش فیبری معادل 414 بار در دمای 7/ 37 درجه سانتیگراد برای حالت آنیل
(S (Drawn: تنش فیبری معادل 710 بار در دمای 7/ 37 درجه سانتیگراد برای حالت کشیده شده
t: مینیمم ضخامت
D: ماکزیمم قطر خارجی واقعی
(LWC (Level Wound Coil: ابعاد لولههای تولیدی کویل
شرکت بابک مس ایرانیان علاوه بر ابعاد فوق آمادگی دارد تا هرگونه درخواست لوله مسی را در زمان مناسب تولید و تحویل دهد.
چرا بابک مس ایرانیان؟
بهبود کیفیت محصولات تولید شده در کنار کاهش هزینههای تولید، کاهش میزان آلایندگی در فرآیند تولید و همچنین کاهش قیمت تمامشده محصول برای مشتری، دو شرکت Upcast فنلاند و ASMAG اتریش را بر آن داشت تا با همکاری یکدیگر جدیدترین روش تولید «لوله مسی» را در دنیا به عنوان Cast&Draw معرفی کنند.
1) ریختهگری (CASTING) (کورهها و تجهیزات ریختهگری، ساخت شرکت Upcast فنلاند)
در این روش، برخلاف سایر روشهای تولید لوله، مادرتیوب اولیه بدون طی مراحل پیش گرمایش، اکستروژن، براده برداری و نورد، مستقیما و بهصورت پیوسته و سربالا (Upcast) ریختهگری شده و سپس وارد مرحله کشش میشود و در واقع تمام هزینههای تولیدی در مراحل میانی حذف شده است. ماده اولیه مورد استفاده در این روش ریختهگری کاتد درجه 1 منطبق با استاندارد ASTM B115 GRADE A است.
مزایای روش ریختهگری سربالا (UPCAST)
- سهولت کنترل کیفیت مذاب از نظر ناخالصیهای مضر و افزایش قابل توجه کیفیت مادرتیوب تولیدی بهواسطه عدم شارژ ضایعات
- محافظت از سطح لوله تحت اتمسفر خنثی بر خلاف سایر روشها، جهت جلوگیری از ایجاد فیلم اکسیدی
- کاهش زمان تحویل محصولات به مشتریان بهواسطه کاهش مراحل تولید
2) کشش (DRAWING)
(دستگاههای کشش، ساخت شرکت ASMAG اتریش)
موارد تاثیرگذار در بخش کشش شامل کیفیت مادرتیوب ورودی، نوع دستگاه کشش، ابزارآلات کشش و روند کاهش قطر و ضخامت برای رسیدن به محصول نهایی است. در این بخش نیز تلاش شده تا در حوزه انتخاب تجهیزات از بروزترین تکنولوژی دنیا استفاده شود. طراحی ابزارآلات کشش توسط شرکت ایتالیایی که طراح ابزارآلات کشش شرکت Buntmetall اتریش (عضو گروه صنعتی Weiland آلمان) میباشد، انجام شده است.
3) کنترل کیفیت و آزمایشگاه
کارخانه لوله مسی شرکت بابک مس ایرانیان با در اختیار داشتن تجهیزات دقیق آزمایشگاهی، محصولات خود را با بالاترین سطح کیفی و مطابق با استانداردهای روز دنیا (EN1057, 12735, 12449 و ASTM B75, B280, B68, B743, B88) به دست مشتریان خود میرساند. این آزمایشگاه جهت کنترل مواد اولیه، محصولات و فرآیند تولید طراحی شده است و آزمونهای زیر مطابق استانداردهای ملی و بینالمللی در این مجموعه انجام میشود:
- آزمون جریان گردابی (Eddy Current): این آزمون به منظور عدم عبور محصول غیریکنواخت و معیوب و حصول اطمینان از سالم بودن لولهها، با عبور صد درصدی لولههای حین تولید از داخل دستگاه آزمون جریان گردابی (ساخت شرکت فورستر آلمان) مطابق استاندارد ملی ایران INSO16927 و استاندارد ASTM E243 انجام میشود.
1) دستگاه تست جریان گردابی Defectomat که غیریکنواختیها، عیوب نقطهای و حفرهای را شناسایی میکند.
2) دستگاه تست جریان گردابی Rotating که غیریکنواختیها، عیوب خطی و طولی را شناسایی میکند.
- آنالیز شیمیایی (عنصری): بهوسیله دستگاه کوانتومتر BELEC و مطابق استاندارد ASTM E255 انجام میگیرد. همچنین مقدار اکسیژن و هیدروژن نیز توسط دستگاه آلمانی Eltra OH 900 اندازهگیری میشود.
- آزمون کشش: تعیین قابلیت ازدیاد طول و همچنین استحکام محصولات مطابق استاندارد ASTM E8M توسط دستگاه تست کشش سنتام انجام میشود.
- آزمون سختی سنجی: این آزمون مطابق استانداردهای ASTM E18 و EN6507-1 توسط دستگاه سختسنجی Innovatest Nexus 7501 انجام میشود.
- آزمون متالوگرافی و تعیین اندازه دانه: طی استاندارد ASTM E112 توسط میکروسکوپ نوری Dewinter انجام میشود.
- کنترل ابعادی: اندازهگیری ابعادی (قطر و ضخامت) بهوسیله میکرومترهای قطرسنج و ضخامتسنج، به منظور کنترل دقت ابعادی و مطابقت داشتن با تلرانسهای ذکر شده در استانداردهای INSO 16927، B251،B280 ،ASTM B75، EN 1057, 12735 انجام میشود.
- آزمونهای خمکاری (Bend)، انبساط (Expand)، فشار هیدرواستاتیکی و پنوماتیکی مطابق استانداردهای EN 1057 و B153 ،ASTM B75 به منظور بررسی قابلیت خمکاری، منبسط شدن و بررسی قابلیت تحمل فشارهای هیدرواستاتیکی و پنوماتیکی به منظور برآوردن نیاز مشتری روی محصول انجام میشود.
4) گواهینامهها: دریافت گواهی کیفیت از موسسه TÜV NORD آلمان، استاندارد ملی ایران، ISO-9001، ISO 14001، ISO18001 و استاندارد HSE-MS از موسسه SGS ایران.
خطمشی شرکت بابک مس ایرانیان در حوزه HSE
خطمشی شرکت بابک مس ایرانیان در حوزه ایمنی، بهداشت و محیط زیست براساس سطح آسیب صفر تعریف شده و این صنعت با توجه به در نظر گرفتن استانداردهای روز جهان و استفاده از کمترین میزان مصرف انرژی و بهدلیل جلوگیری از آلودگیهای آب، خاک و هوا در فرایند تولیدات خود، یکی از صنایع سبز دنیا به شمار میرود.
کنترل کیفیت و آزمایشگاهها
آزمایشگاه کنترل کیفیت شرکت بابک مس ایرانیان به منظور حفظ، ارتقاء و بهبود مستمر کیفیت محصولات خود به صورت یک واحد مستقل در این شرکت فعالیت دارد و با در اختیار داشتن تجهیزات دقیق آزمایشگاهی و حضور متخصصان برجسته به انجام آزمونهای خاص و دقیق، به تولید محصولات استاندارد با هدف افزایش ضریب کیفیت محصولات میپردازد.
محدوده فعالیتهای واحد کنترل کیفیت، هم راستا با واحد تولید از ابتداییترین مرحله یعنی خرید مواد اولیه، تا آخرین مرحله یعنی ارائه محصول به مشتری لازم و ضروری است. بنابراین بازرسیها و کنترل فرایند براساس موارد زیر صورت میگیرد:
- کنترل فرایند تولید محصول
- نمونهگیری از محصولات
- بازرسی نمونهها
- کنترل مواد ورودی
- کنترل حین تولید به منظور اقدامات پیشگیرانه
این شرکت دارای دو آزمایشگاه مرکزی و کارخانه لوله مسی است.
1- آزمایشگاه مرکزی
این آزمایشگاه جهت کنترل مواد ورودی، کنترل کیفیت محصولات و مواد کارخانه تولید کاتد راهاندازی شده است.
2- آزمایشگاه کارخانه لوله مسی
این آزمایشگاه جهت کنترل محصولات و فرآیند تولید کارخانه لوله مسی طراحی شده است و تستهای زیر براساس استانداردهای بینالمللی در این کارخانه روی محصول انجام میشود.
آزمون جریان گردابی (Eddy Current): به منظور عدم عبور محصول غیریکنواخت و معیوب (لولههای سوراخ دار یا خراش دار) و حصول اطمینان صد درصدی از سالم بودن لولهها، این آزمون مطابق استاندارد ASTM E243 با عبور لوله (حین فرایند تولید) از داخل دستگاه آزمون جریان گردابی (Rotating و Defectomat) برروی کلیه محصولات انجام میشود.
آنالیز شیمیایی (عنصری): آنالیز عنصری مطابق استانداردهای ASTM B75 و ASTM E255 و به منظور تعیین ترکیب شیمیایی بهوسیله دستگاه کوانتومتر Belec انجام میشود. مقدار اکسیژن و هیدروژن نیز توسط دستگاه Eltra OH اندازهگیری میشود.
آزمون کشش: این آزمون به منظور تعیین قابلیت ازدیاد طول و همچنین استحکام محصولات مطابق استاندارد ASTM E8M انجام میشود.
آزمون سختی سنجی: مطابق استانداردهای ASTM E18 و EN6507-1 و به منظور تعیین سختی محصولات صورت میگیرد.
آزمون متالوگرافی: بررسی متالوگرافی و تعیین اندازهدانه مطابق استاندارد ASTM E112 و توسط میکروسکوپ نوری انجام میشود.
کنترل ابعادی: اندازهگیری ابعادی (قطر و ضخامت) بهوسیله میکرومتر به منظور کنترل دقت ابعادی و مطابقت داشتن با تلرانسهای ذکر شده در
استانداردهای INSO 16927، ASTM B251، ASTM B280 ، ASTM B75، EN 1057 و EN 12735 انجام میشود.
آزمون خمکاری (Bend): به منظور بررسی قابلیت خمکاری و برآوردن نیاز مشتری روی محصول صورت میگیرد.
آزمون انبساط (Expand): به منظور بررسی قابلیت منبسط شدن و برآوردن نیاز مشتری روی محصول انجام میشود.
آزمون فشار هیدرواستاتیکی و پنوماتیکی: این آزمونها بهمنظور بررسی فشارهای هیدرواستاتیکی و پنوماتیکی قابل تحمل لوله مطابق استاندارد ASTM B75 روی محصول انجام میشوند.
تجهیزات اصلی آزمایشگاه