فولادسازِ کارخانه فولادساز
تکنولوژی فولاد خوزستان از کجا آمد و به کجا رسید؟
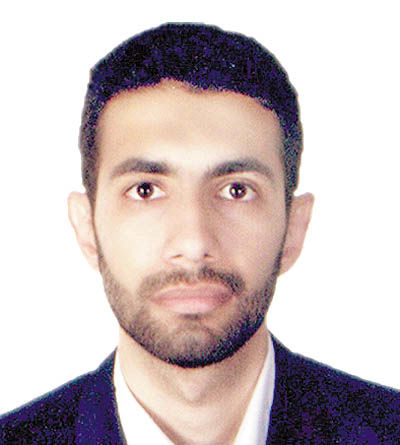
فولاد خوزستان قرار بود چگونه باشد؟
همانگونه که در اطلاعرسانیهای شرکت فولاد خوزستان و در ادبیات مدیران آن عنوان شده؛ گرچه به لحاظ تاریخی، شروع عملیات احداث مجتمع اولیه این شرکت به سال ۱۳۵۳ در زمان رژیم گذشته بازمیگردد، اما تا پیروزی انقلاب اسلامی، درصد کمی از کار صورت گرفته بود. در حقیقت، عمده عملیات نصب، تکمیل و راهاندازی واحدها و همچنین موفقیتهای بهدستآمده در جریان رسیدن به ظرفیت اولیه و توسعه تولید در شرکت را باید مرهون همت بلند و توان فنی چشمگیر و تلاش یکپارچه مدیران و کارکنان شرکت پس از پیروزی انقلاب اسلامی و دوران جنگ تحمیلی دانست. بر اساس توافقات حاصله قرار بود در این مجتمع تاسیساتی به شرح زیر احداث شود:
دو واحد گندلهسازی با مجموع ظرفیت تولید پنج میلیون تن گندله در سال یک کوره احیای مستقیم به روش پروفر به ظرفیت تولید ۳۳۰ هزار تن آهن اسفنجی (بریکت گرم) در سال سه مدول احیای مستقیم میدرکس با مجموع ظرفیت تولید سالانه یک میلیون و ۲۰۰ هزار تن آهن اسفنجی یک واحد احیای مستقیم به روش H.Y.L به ظرفیت تولید یک میلیون تن در سال شش کوره قوس الکتریکی ۱۸۰تنی برای تولید ۶۵/ ۱ میلیون تن مذاب در سال یک ماشین ششخطه ریختهگری بلوم و دو ماشین دوخطه ریختهگری اسلب برای ریختهگری و تولید نهایی یک میلیون و ۵۵۰ هزار تن شمش فولاد در سال تصفیهخانه آب، کارخانه اکسیژن، پستهای برق، سیستم حمل مواد و دیگر تاسیسات جانبی.
فولاد خوزستان به چه سمتی رفت؟
در این طرح پیشبینی شده بود از ۲/ ۵۳ میلیون تن آهن اسفنجی و بریکت تولیدشده در واحدهای احیای مستقیم، حدود دو میلیون تن آن برای مصرف در فولادسازی و مابقی برای فروش عرضه شود. برنامه راهاندازی این تاسیسات نیز طی سه فاز جداگانه طراحی شده بود که بر اساس آن در نهایت ظرفیت اسمی کارخانه به میزان یک میلیون و ۵۵۰ هزار تن شمش طی یک دوره دوساله تحقق مییافت. عملیات زیرسازی و بهطور همزمان خرید و حمل تجهیزات کارخانه برای نصب واحدهای مختلف از سال ۱۳۵۳ شمسی آغاز شد و با مشارکت بیش از ۷۰ شرکت بینالمللی خارجی و ۳۰ شرکت داخلی در قالب پیمانکار و ناظر و مشاور تا نیمه دوم سال ۱۳۵۷ ادامه یافت.
پیشرفت فیزیکی کل پروژه تا آن زمان حدود ۵۰ درصد اعلام شده بود و از آن تاریخ تا پایان نیمه اول سال ۱۳۶۰ به دلیل تحولات انقلاب اسلامی در کشور و شرایط جنگ تحمیلی، دوران فترت و توقف کار پیش آمد. پس از این دوران و عزم جدی دولت بر ادامه کار و تکمیل پروژه، شرکتهای داخلی داوطلب و جویندگان کار در قالب گروههای جدیدالتاسیس تعاونی وارد عمل شدند. بهطوری که ظرف کمتر از دو سال تا دیماه سال ۱۳۶۱ پیشرفت کار به میزان ۷/ ۶۷ درصد برآورد شد و سرانجام در سال ۱۳۶۷ فاز اول مجتمع فولاد اهواز به دست توانمند مهندسان و تکنسینهای شرکت راهاندازی شد. لازم به ذکر است که در طول جنگ تحمیلی این کارخانه سهبار در سالهای ۱۳۶۴، ۱۳۶۵و ۱۳۶۶ مورد حملات هوایی قرار گرفت که خسارات زیادی را به تجهیزات وارد کرد.
در نهایت نخستین کوره فولادسازی در دهه فجر سال ۱۳۶۷ روشن شد و در بهار سال ۱۳۶۸ با حضور مقام معظم رهبری (در زمان مسوولیت ریاستجمهوری) تولید رسمی مجتمع به میزان یکصدهزار تن شمش آغاز شد. ظرفیت اسمی اولیه شرکت ۵/ ۱ میلیون تن شمش فولاد در سال بود که طی دهه نخست فعالیت آن تا سال ۱۳۷۷ به دست آمد. طرحهای توسعه کارخانه زیرسقف و همزمان با تولید به گونهای برنامهریزی و اجرا شد که طی دو فاز، این ظرفیت به ترتیب به دو میلیون و چهارصد هزار تن در سال ۱۳۸۷ و سه میلیون و ۲۰۰ هزار تن تا سال ۱۳۹۰ رسید. هماکنون نیز با اجرای طرحهایی از جمله تقویت کورههای قوس الکتریکی ششگانه و استفاده از کورههای پاتیلی در فولادسازی، ظرفیت افزوده سه میلیون و ۸۰۰ هزار تن شمش در سال به دست آمده تا دومین فولادساز بزرگ کشور باشد.
فولاد خوزستان هماکنون چگونه است؟
فرآیند تولید را باید عملکرد اصلی یک واحد صنعتی بهشمار آورد که در خصوص فولاد با محوریت تولید محصولات میانی و نهایی قطعاً مهمترین بخش فعالیتهاست و عملکرد تولید را باید معدل موفقیتهای یک شرکت همچون فولاد خوزستان بهشمار آورد. البته در بخشهای دیگر این ویژهنامه به ویژگیهای تولید پرداخته شده اما اشاره به فرآیندهای تولید فعلی به صورت مختصر میتواند نمونهای از عملکرد واقعی شرکت بهشمار رود. کارخانههای گندلهسازی، احیای مستقیم و بخش فولادسازی سه بخش اصلی فعالیت در فولاد خوزستان است. شرکت فولاد خوزستان متشکل از سه واحد اصلی تولید برای عرضه محصولات میانی و نهایی است:
۱- کارخانههای گندلهسازی: شامل دو مدول گندلهسازی، هر یک به ظرفیت اسمی ۳/ ۲ میلیون تن گندله در سال است. در این کارخانهها سالانه بالغ بر شش میلیون تن گندله سنگآهن از پودر تغلیظشده تولید میشود.
۲- کارخانههای احیای مستقیم: در این بخش گندلههای سنگآهن به آهن اسفنجی (آهن احیای مستقیم) تبدیل میشوند. در این بخش در حال حاضر سه مدول میدرکس با ظرفیت ۲/ ۲ میلیون تن و دو مدول زمزم با ظرفیت ۱/ ۸ هزار تن در سال مشغول تولید هستند که رویهمرفته سالانه چهار میلیون تن آهن اسفنجی تولید میکنند. مدولهای زمزم بر اساس فناوری بومیشده میدرکس و توسط کارشناسان داخلی طراحی و نصب شدهاند.
۳- بخش فولادسازی: در این بخش محصولات نهایی شرکت یعنی شمش ۱ و تختال ۲ از آهن اسفنجی تولید میشود. بخش فولادسازی متشکل از شش کوره قوس الکتریکی، چهار کوره پاتیلی، دو ماشین دوخطه ریختهگری تختال، سه ماشین ششخطه شمش و تاسیسات جمعآوری غبار فولادسازی است.
برخی از موفقیتهای فولاد خوزستان در سالهای اخیر
اولین شرکت فولادساز مستقرکننده نظام مدیریت کیفیت ISO ۹۰۰۱ در سطح کشور اولین شرکت فولادساز مستقرکننده نظام پیشنهادها و گروههای QCC در سطح شرکت مهمترین قطب تولیدکننده شمش فولاد کشور با سهم بازاری غیرقابل چشمپوشی اولین شرکت سازنده کوره پاتیلی در ایران تنها شرکت دارنده تکنولوژی ساخت کارخانه تولید آهن اسفنجی به روش میدرکس در سطح خاورمیانه با ظرفیت بالا (یک میلیون تن) دریافت پروانه تحقیق و توسعه دریافت تندیس زرین رعایت حقوق مصرفکنندگان دریافت تندیس سیمین جایزه ملی تعالی سازمانی
تعریف بومیسازی و الزامات آن
بومی شدن تکنولوژی یعنی؛ شناخت عمیق تکنولوژی وارداتی، قابل اجرا کردن تکنولوژی وارداتی، تسلط بر تکنولوژی انتقالیافته و ایجاد آن بر اساس خواستهها و تواناییهای داخلی.
بومیسازی و الزامات آن
اما بومیسازی الزاماتی دارد که در ابتدا به باور قلبی بر توسعه تکنولوژی صنعتی و اقتصادی بازمیگردد که در فولاد خوزستان مورد بررسی دقیق قرار گرفته است. در لایه دوم سیاستگذاری و برنامهریزی تکنولوژیک مورد نیاز است که باید به آن توجه جدی داشت. اما پرورش نیروی انسانی متخصص لایه بعدی و بسیار مهمی است که تا زمانی که ایجاد نشود، گویی بومیسازی جان نگرفته است. در لایه آخر نیز وجود منابع سختافزاری و نرمافزاری لازم و کافی را باید در دستور کار قرار داد تا فرآیند بومیسازی تکنولوژیها کامل شود.
مهمترین شاخصهای ارزیابی بومیسازی تکنولوژی
میزان صرفهجویی در هزینه ساخت محصول یا ارائه خدمات میزان صرفهجویی هزینهها در زمان اجرای تکنولوژی میزان بهکارگیری منابع انسانی داخل میزان استفاده از قطعات یا تجهیزات داخلی میزان دستیابی به دانش فنی تکنولوژی قابلیت انتقال تکنولوژی میزان دستیابی به بهرهوری کیفیتی میزان دستیابی به ظرفیت کمی تکنولوژی
در موارد فوق تقریباً ملزومات شاخصهای ارزیابی بومیسازی تکنولوژی را مورد بحث قرار دادیم که شناخت آنها در چارچوب تلاش برای بومیسازی تکنولوژی در فولاد خوزستان نمود عینی پیدا کرده است که خروجی آن انتظار رونق بومیسازی در این کارخانه است. رشد تکنولوژیک هر واحد تولیدی وقتی از مسیر بومیسازی آغاز شده نهایتاً به نوآوری و ایجاد تکنولوژیهای جدید و پتانسیل توسعه منتهی شده است. این روند کلی خروجیای را دربر دارد که باید شاهد رونق تولید و تقویت تکنولوژی و در نهایت نتایج بومیسازیها باشیم. با توجه به این موارد بررسی نتایج بومیسازی تکنولوژی در فولاد خوزستان نشان میدهد که آیا این شرکت توانسته است در این مسیر گامهای قدرتمندی بردارد یا خیر. شواهد نشان میدهد که نتایج بومیسازی تکنولوژیکی در فولاد خوزستان برجسته است و این روند میتواند آینده بهتری را برای این شرکت از مسیر حجم تولید دربر داشته باشد.
نتایج بومیسازی تکنولوژی در فولاد خوزستان
فعالیت تغییر طرح سیل باکسهای کولینگ کوره از آبگرد به نسوز
فعالیت کاهش توقفات نوار نقاله G۱۰۳۰ از طریق ارتقای سیستم محرک
تغییر چرخدندههای تخصصی اتوماتیک کردن کمپرسورهای اضطراری ابزار دقیق در صورت افت فشار تغییر طرح برگشتی آسیاب خط ۱ و ۲۰۶۷ B۲ و ۲۰۱۷ B به سیستم DISCOUNT طراحی و ساخت کوپلینگ جدید برای فلوگیتها افزایش طول رولر و شافت آن و تغییر در ساپورت رولرهای برگشت کانوایرها و تبدیل رولرها از بافری به تخت G۷۰۰۴ – G۱۰۲۴ – G۳۰۶۵ – G۷۰۰۳ – G۷۰۰۱ مکانیزه کردن فلوی لجن خمیر طراحی مجدد شبکه آب آشامیدنی نصب تایمر بر روی لرزش فنهای ۲۲ / ۲۴، C۲ تغییر طرح شافت و هوزینگ بیرینگ اسکرین ۸
تغییر هندسی تاندیشهای بلوم جهت جلوگیری از سوراخ شدن طراحی و آمادهسازی آزمایشگاه قسمت کارتهای PLC مدل U ۱۳۵ شرکت زیمنس ساخت ساپورت نگهدارنده چک فازها بهینهسازی کنترل فنری قالبهای بیلت با تغییر سیستم کنترلر فنر سیستم کنترل روغن در پساب صنعتی
موارد فوق نشان میدهد که بومیسازی تکنولوژی و توجه جدی به نوآوری موجب شده تا وضعیت فولاد خوزستان به نسبت گذشته تغییری جدی داشته باشد که سادهترین خروجیهای آن را میتوان در پروژههای برجسته جستوجو کرد که هر کدام از آنها نشاندهنده عمق بومیسازی تکنولوژی و گذار به سمت دوران قدرتمندی از رونق تولید و تقویت سرمایهگذاریها است. با توجه به این موارد بررسی پروژههای بارز شرکت نشاندهنده خروجی جذاب و قدرتمندی برای حمایت از آینده صنعتی این شرکت و همچنین دورنمای صنعت فولاد از مسیر تکنولوژیهای بومیسازی شده است.
پروژههای بارز: ۱- ساخت دو دستگاه تریلر حمل سبد قراضه خاص شرکت فولاد خوزستان که اولین نمونه آن در آخر سال ۹۲ به بهرهبرداری رسید که پس از یک سال کار و تایید بهرهبرداری دستگاه دوم در دستور کار قرار گرفت تا با استفاده از تجربیات دستگاه اول دومین دستگاه بهبودیافته طراحی شده و در اسفند ۹۴ تحویل شود. لازم به ذکر است که تکنولوژی ساخت زنبیلکش در انحصار چند کشور خاص بوده و خرید آنها علاوه بر اعمال شرایط سخت تحریم در حال حاضر، ارزبری بالایی دارد. / ۲- پروژه استقرار سیستم مدیریت انرژی بر اساس ایزو ۵۰۰۰۱ ویرایش ۲۰۱۱ و فعالیتهای جانبی مربوطه (آگاهسازی انرژی و انجام ممیزی انرژی) که باعث شد شرکت فولاد خوزستان بهعنوان اولین شرکت فولادساز در کشور گواهینامه سیستم مدیریت انرژی جامع را از نماینده شرکت TUV-NORD دریافت کند. / ۳- ادامه فاز ۲ مدیریت دانش شامل: یکپارچهسازی منابع دانشی (حداقل ۱۶ منبع دانشی) با نظام مدیریت دانش، فرهنگسازی و اجرای دورههای آموزشی، راهبری مهندسان دانش و یکپارچهسازی نرمافزارهای مرتبط با مدیریت دانش/ ۴- هدایت کمیته اجرای پروژه توسعه محصولات جدید فولادی API X۶۰ و API X۷۰.
گذار از بومیسازی تکنولوژی تا آیندهای نوآورانه
همانگونه که عنوان شد لایه بعدی بومیسازی تکنولوژی، گذار به نوآوری در صنایع مختلف و عملکردهای اجرایی و حتی مدیریتی است که طرحهای پژوهشی و حمایت از ایدهها را باید در همین مسیر جستوجو کرد. در شرایطی که بومیسازی تکنولوژی شکل گرفته، توجه به نوآوری رکن اصلی توسعه فناورانه شرکتهای صنعتی است و این مطلب در عملکرد فولاد خوزستان به وضوح مشاهده میشود. اینکه در خصوص نوآوری در صنایع بزرگ کشور غفلتهای بزرگی شده را نمیتوان نادیده گرفت و هرچه شرکتهای بزرگ صنعتی همچون واحدهای برجسته و معظم تولید فولاد به این سمت حرکت کنند به معنی آن است که در گام اول ریسکهای بزرگی را پذیرفته و در گام دوم با پذیرش هزینههای آن، احتمال رونق قدرتمند و گذر از نگرانیهای فنی بسیاری را دربر دارد. سالهاست که ریسک تحریم یکی از واقعیتهای پیش روی واحدهای صنعتی در کشور است بنابراین عبور از این موارد در نهایت به توسعه برخی دانشها و عملکردهای خاصی منجر خواهد شد که شاید در نگاه اول برای عموم جامعه چندان برجسته نباشد اما اهل فن به خوبی میدانند که گذشته این شرکت و آینده آن چه میزان با یکدیگر متفاوت بوده و چه سرعتگیرهایی از پیشروی توسعه برداشته شده است. با توجه به این موارد، فعالیتهای تحقیقاتی و فناوری را باید آخرین گام از روند توسعه این شرکت بهشمار آورد که در این خصوص فعالیتهای بسیاری صورت گرفته است.
فعالیتهای کلی تحقیقات و فناوری در سال گذشته
۱- انجام اقدامات لازم جهت اجرای قراردادهای پژوهشی جاری (۱۸ قرارداد) / ۲- انجام اقدامات لازم جهت اعزام حدود ۱۲۰ نفر از کارکنان شرکت به همایشها و سمینارهای علمی-پژوهشی در طول سال بهویژه هفته پژوهش استان و سمپوزیوم فولاد که شرکت از اعضای اصلی انجمن آهن و فولاد محسوب میشود. / ۳- انجام اقدامات لازم جهت فراخوان، تهیه، ارسال و دریافت تاییدیه (پذیرش جهت ارائه یا چاپ) مقالات همکاران و اعزام پذیرفتهشدگان به مجامع علمی مرتبط (۳۰ مورد در سال) / ۴- ارتباط تنگاتنگ با دانشگاهها و مراکز پژوهشی کشور در تعریف پروژههای مورد نیاز (بهویژه حضور در دانشگاه شهید چمران و ارائه نیازها) و همچنین هماهنگی برای پشتیبانی از انجام دهها پروژه دانشجویی در سطح کارشناسی ارشد و دکترا در شرکت / ۵- مشارکت در تدوین اظهارنامه تعالی سازمانی سال ۹۴ شرکت و گردآوری اطلاعات و پاسخگویی به ارزیابان تعالی سازمانی و ممیزان کیفیت و انرژی / ۶- مشارکت در تدوین تعدادی از استانداردهای ملی فولاد کشور (بهویژه هدایت و پیگیری تدوین استاندارد ملی شمش) / ۷- برگزاری دو سمینار تخصصی مرتبط در داخل شرکت برای معرفی محصولات و فناوریهای جدید / ۸- انجام اقدامات لازم در تدوین درخت فناوری شرکت و اجرای پروژه روند تکنولوژی در راستای استقرار نظام مدیریت فناوری / ۹- حضور در جلسات تدوین استراتژیهای شرکت، معاونت برنامهریزی و توسعه و مدیریت دانش / ۱۰- تهیه و تدوین آییننامهها و دستورالعملهای مورد نیاز پژوهشی و پیگیری جهت تصویب و اجرایی کردن آنها / ۱۱- پیگیری تغییر در شیوههای تعریف، تصویب و اجرای فعالیتهای پژوهشی و در همین راستا اخذ دستور مدیرعامل محترم برای تشکیل کمیته پژوهش شرکت با اعضای مرتبط و تهیه اهداف و وظایف آن / ۱۲- پیگیری تمدید پروانه تحقیق و توسعه برای شرکت (از طریق سازمان صنعت، معدن و تجارت استان) / ۱۳- بررسی درخواستهای مشتریان جهت امکانسنجی فنی-اقتصادی تولید / ۱۴- ارائه خدمات مشاوره فنی به واحدهای مختلف شرکت در زمینه فعالیتهای مرتبط (تولید، فروش و...) / ۱۵- پیگیری و همکاری در مطالعات امکانسنجی احداث کارخانه تولید بریکت سرد / ۱۶- همکاری با مدیریت آموزش در تدوین و ارائه دورههای تخصصی در مرکز آموزش و آموزشکده علمی-کاربردی شهدای فولاد / ۱۷- عضویت در کارگروه تولید، تقاضا و صادرات محصولات دانشبنیان استان خوزستان و شرکت در جلسات و همایش برگزارشده در دانشگاه شهید چمران به همین مناسبت.