نگاهی به صنعت و بازار فولاد ایران
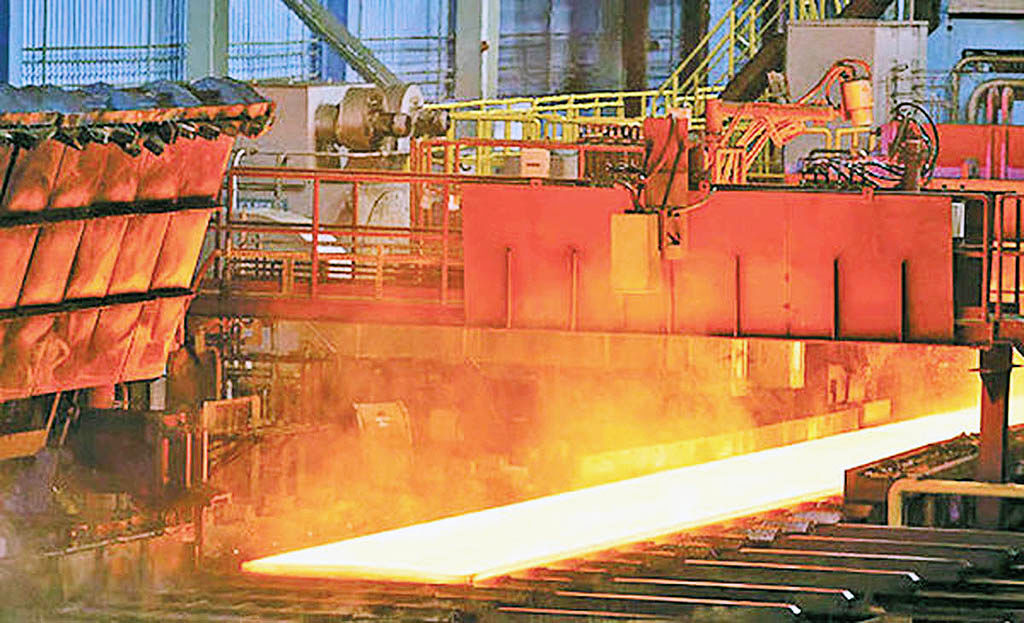
از کنسانتره تا تولید فولاد خام
در حال حاضر ۷۰ واحد فعال در زمینه تولید فولاد خام مشغول به فعالیت هستند که این واحدها با ظرفیت اسمی ۹۴/ ۳۳ میلیون تن ظرفیت هستند که تولید واقعی آنها ۶۷/ ۲۴ میلیون تن است. بزرگترین واحدهای تولیدکننده فولاد در کشور فولاد مبارکه، ذوب آهن اصفهان و فولاد خوزستان هستند.
در زمینه آهن اسفنجی نیز ۲۱ واحد فعال با ظرفیت اسمی ۶۷/ ۳۲ میلیون تن مشغول به کار هستند که در ازای این میزان ظرفیت ۳۶/ ۲۶ میلیون تن به صورت واقعی تولید دارند. بزرگترین واحدهای تولیدکننده آهن اسفنجی در کشور، فولاد مبارکه و فولاد خوزستان است.
در زمینه گندله ۱۳ واحد با ظرفیت اسمی ۱۵/ ۴۸ میلیون تن مشغول به تولید هستند که از این ظرفیت ۵/ ۴۱ میلیون تن تولید واقعی انجام میگیرد.
در زمینه کنسانتره نیز ۲۶ واحد در کشور فعال هستند که ظرفیت اسمی آنها ۴/ ۵۲ میلیون تن است و به میزان ۹/ ۴۴ میلیون تن تولید واقعی دارند. ۵۸ درصد تولید کنسانتره کشور متعلق به شرکت گلگهر و چادرملو است.
براساس طرح جامع فولاد ۱۳۹۷، تولید واقعی کنسانتره سنگ آهن از ۱۲ میلیون تن در سال ۱۳۸۶ به ۴۵ میلیون تن در پایان سال ۱۳۹۷ رسیده است که میانگین رشد سالانه آن معادل ۱۳ درصد بوده است.
در زمینه تولید واقعی گندله نیز از تولید واقعی ۱۱ میلیون تن گندله در سال ۱۳۸۶ به ۴۲ میلیون تن در سال ۱۳۹۷ رسیدهایم که میانگین رشد سالانه آن برابر ۱۲ درصد بوده است.
در زمینه تولید فولاد خام نیز از تولید واقعی ۱۰ میلیون تن در سال ۱۳۸۶ به ۲۵ میلیون تن تولید در پایان سال ۱۳۹۷ رسیدهایم که با میانگین رشد سالانه ۷ درصدی همراه بوده است.
پیشبینی افزایش تولید زنجیره فولاد تا چشمانداز ۱۴۰۴
در افق چشمانداز ۱۴۰۴ قرار است که ظرفیت تولید فولاد کشور به ۵۵ میلیون تن برسد. بر این اساس و در راستای تامین مواد اولیه برای تولید فولاد خام باید ظرفیت تولید آهن اسفنجی به ۴۵ میلیون تن، گندله به ۷۴ میلیون تن و کنسانتره آهن نیز به ۸۰ میلیون تن برسد.
سرمایهگذاری مورد نیاز در زنجیره فولاد تا تحقق تولید ۵۵ میلیون تنی
برای رسیدن به تولید ۵۵ میلیون تن فولاد در زمینه تولید فولاد نیاز به ایجاد ۳۷/ ۲۱ میلیون تن ظرفیت با سرمایه ۲۳۷۹ میلیون یورو، در زمینه آهن اسفنجی-چدن نیاز به ایجاد ظرفیت ۹۸/ ۱۱ میلیون تن با سرمایه ۸۷۸ میلیون یورو، در زمینه گندله نیاز به ایجاد ظرفیت ۳۲/ ۲۵ میلیون تن با سرمایه ۸۵۸ میلیون یورو و کنسانتره سنگآهن نیاز به ایجاد ظرفیت ۴/ ۲۰ میلیون تن با سرمایه ۵۳۸ میلیون یورو است.
در مجموع برای تکمیل زنجیره فولاد تا رسیدن به ۵۵ میلیون تن تولید به ۸/ ۶ میلیارد یورو سرمایه نیاز است.
سرمایهگذاری در زیرساختها برای رسیدن به تولید ۵۵ میلیون تن
در زنجیره تولید فولاد تا تحقق ظرفیت ۵۵ میلیون تنی به سرمایهگذاری ۲/ ۱۷ میلیارد یورو نیاز است که در این راستا ۴۸۰ میلیون یورو آن به راه، ۱۰۵۰ میلیون یورو به توسعه بنادر، ۷۸ میلیون یورو به انشعابات گاز، ۳۰۹۳ میلیون یورو به نیروگاه- خط و پست، ۷۲۰ میلیون یورو تجهیزات معادن، ۹۰۲ میلیون یورو به آب و ۴۰۸۸ میلیون یورو به ریل باید اختصاص یابد.
پیشبینی نیاز مصرف آب، گاز و برق صنعت فولاد در سال 1404
در حال حاضر 11 میلیارد مترمکعب نیاز فعلی مصرف گاز در صنعت فولاد است که در سال 1404 و با توجه به رسیدن به تولید 55 میلیون تن نیاز به 3/ 17 میلیارد مترمکعب خواهد داشت که برای رسیدن به این هدف نیاز به 730 میلیارد تومان سرمایهگذاری است.
در زمینه برق نیز هماکنون 28287 میلیون کیلووات ساعت نیاز مصرف فعلی برق در صنعت فولاد است که در چشمانداز 1404 باید به 45808 میلیون کیلووات ساعت برسد که در این راستا به 47/ 3 میلیارد دلار سرمایهگذاری نیاز است.
در زمینه آب نیز در حال حاضر 6/ 183 میلیون مترمکعب نیاز فعلی در صنعت فولاد است که به 5/ 262 میلیون مترمکعب تا افق 1404 مورد نیاز است.
توسعه حمل و نقل
صنعت ریلی کشور برای رسیدن به سند چشمانداز صنعت فولاد در افق 1404 باید سالانه حدود 9 درصد رشد داشته باشد. (یعنی احداث 430 کیلومتر در هر سال)، این در حالی است که متوسط نرخ رشد احداث خطوط ریلی در یکی دو سال گذشته حدود یک درصد بوده است. بدیهی است که با چنین رشدی، راهاندازی صنایع فولادی بدون تامین بهموقع زیر ساختهای مورد نیاز با مشکل جدی روبهرو خواهد شد.
چشمانداز صادرات فولاد ایران و چالشهای پیشرو
ایران در سالهای ابتدایی دهه ۹۰ شمسی به صورت میانگین بین 5 تا 7 میلیون تن واردات فولاد اعم از شمش و مقاطع فولادی داشت، اما در حال حاضر درصدد دستیابی به سهم ۴۰ تا ۴۵ درصد تولید فولاد برای صادرات است. در افق چشمانداز فولاد نیز باید بالای 40 درصد از تولیدات خود را به صادرات اختصاص دهد.
در زمینه صادرات فولاد این پرسش مطرح است که در چگونه میتوان با بهرهگیری از نقاط قوت حداکثر بهره را از فرصتها برد؟ در پاسخ به این پرسش میتوان به نکات زیر توجه کرد:
-بهرهگیری از ظرفیتهای بازار منطقهای و نفوذ در بازارهای خاورمیانه و بهویژه کشورهایی با روند توسعه بالاتر (افغانستان، عراق و...)
-افزایش ضرایب حمایتی دولت از صادرکنندگان فولادی با هدف جذب سرمایههای ارزی
-ایجاد مشوقها و راهکارهای حمایتی برای ورود فناوری جدید با راندمان بالاتر.
در پاسخ به این پرسش که چگونه با بهرهگیری از فرصتها نقاط ضعف را تبدیل به نقطه قوت کرد یا از شدت نقاط ضعف کاست؟ میتوان به نکات زیر توجه کرد:
-استفاده از سرمایهگذاری خارجی و داخلی در سیستم حمل و نقل
-استفاده از فناوری نوین در تولید فولاد
-توسعه روشهای مدیریت بازار برای گسترش و نفوذ در بازارهای منطقهای
-کاهش موانع گمرکی و صادراتی همراه با استانداردهای سازمان تجارت جهانی.
در پاسخ به این پرسش که چگونه با استفاده از نقاط قوت میتوان اثر تهدیدها را حذف کرد یا کاهش داد؟ میتوان به موارد زیر توجه کرد:
-تکنرخی کردن ارز و تضمین حمایت از صادرکنندگان در برابر نوسانات ارزی
-بازاریابی و رایزنی هیاتهای تجاری در کشورهای منطقه به منظور ایجاد بازارهای نوین فولادی
-کاهش قیمت تمامشده محصولات فولاد به منظور رقابت در بازارهای جهانی
-توجه بیشتر به تجاریسازی فولاد و محصولات آن با افزایش کیفیت محصولات برای مقابله با تغییرات احتمالی ساختارهای سیاسی و اقتصادی.
در پاسخ به این پرسش که چگونه باید با کاهش دادن نقاط ضعف، تاثیر تهدیدات را کاهش داد یا تاثیرشان را حذف کرد؟ میتوان به موارد زیر توجه کرد:
-ایجاد ساختارهای مناسب در مبادی مبادلاتی و تجهیز بنادر به صورت استاندارد
-افزایش بهرهوری در جهت کاهش قیمت تمامشده محصولات و به دنبال آن افزایش رقابتپذیری
-افزایش قدرت بازاریابی منطقهای و بینالملل در جهت شناسایی ظرفیتهای جدید بازارهای نوین.
تاثیر تحریمها بر طرح جامع فولاد کشور
در بررسی آثار تحریمها بر صنعت فولاد را میتوان آن را به دو بخش توسعه صنعت فولاد و بازار فولاد تقسیم کرد.
در بخش توسعه صنعت فولاد، تحریمها میتواند مواردی همچون تامین مالی و استفاده از منابع خارجی، تامین فناوری، صادرات و توسعه اکتشافات جهت تامین مواد اولیه را تحت تاثیر خود قرار دهد.
در بخش بازار فولاد نیز تحریمها میتواند با رکود بخش ساختمان و به دنبال آن تاثیر بر صنعت فولاد، رکود بخش صنعت و تاثیر آن بر صنعت فولاد (با ایجاد چالشهایی در واردات مواد اولیه، گشایش السی و...) و رکود در بخش خودرو و تاثیر آن بر صنعت فولاد با از دست دادن شرکای خارجی، مشکلات تامین قطعات و مواد اولیه، افزایش قیمت خودروهای داخلی، محدود شدن انتقال فناوری و کاهش قدرت خرید مشتریان، آثار خود را نشان دهد.
محرکههای تاثیرگذار بر آینده صنعت فولاد در ایران
عوامل مختلفی بر آینده صنعت فولاد در ایران تاثیرگذار است که در این راستا میتوان به قیمت و دسترسیپذیری به انرژی (گاز، زغالسنگ و برق)، تابآوری زیست محیطی (منابع آبی و آلودگی هوا)، سیاستهای دولتی در حلقههای بالادستی صنعت (بهویژه معدن)، حجم بودجههای عمرانی دولت، استهلاک فناوری و عدم جایگزینی فناوری و افت کارآیی ناشی از مسائل داخلی (بازار ایران) یا بینالمللی (تحریمها) اشاره کرد.