در گفتگو با مدیر تکنولوژی فولاد فکور صنعت تهران مطرح شد
نقشه راه توسعه صنعت فولاد
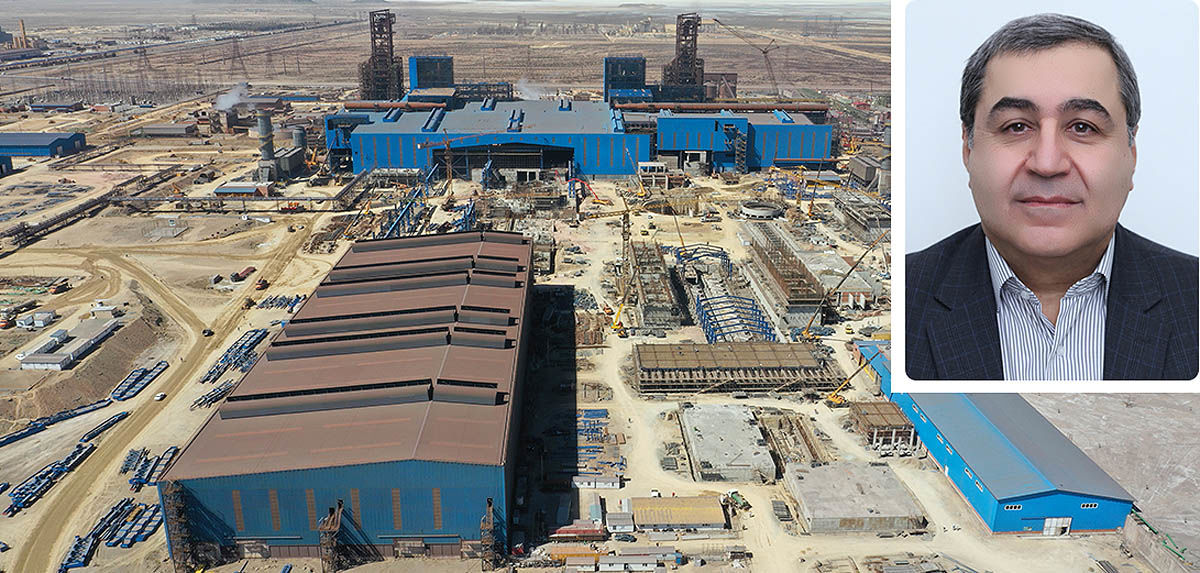
از آنجایی که صنعت فولاد از ابتدا یک صنعت انرژیبر بوده است، دستاندرکاران این صنعت اعم از تولیدکنندگان و صاحبان دانش و تکنولوژی همواره بهدنبال طرحهای کاهش هزینه و مصرف انرژی بودهاند و این حرکت خود در راستای کاهش تولید گازهای گلخانهای بوده و با مطرح شدن اعمال محدودیتها و اعمال جریمههای سنگین بهعنوان یک اهرم بازدارنده در تولید و انتشار این گازها، پیگیری و اقدام در رابطه با این موضوع را تشدید کرده است.
نعمتالله اسدی مدیر تکنولوژی فولاد فکور صنعت تهران در گفتگو با دنیای اقتصاد به چند سوال درباره فولادسازی سبز پاسخ داد.
سهم صنعت فولاد در تولید گازهای گلخانه ای چقدر است؟
سهم صنعت فولاد از تولید گاز CO۲ حدودا ۹-۷% است. تولید جهانی فولاد در جهان حدودا ۱،۹۰۰ میلیون تن در سال است البته این آمار مربوط به ۲ سال پیش بوده و تولید جهانی جمعا طی دو سال گذشته حدودا ۷ درصد افزایش داشته ولی نسبتها همین حدود است. از این مقدار ۷۲ درصد آن از ترکیب روش کوره بلند و کنورتور و ۲۸ درصد آن - بیش از ۵۰۰ میلیون تن در سال - از طریق کوره قوس - که بخش عمده تامین خوراک آن از قراضه است - تولید میشود و ۲۰ درصد از ۲۸ درصد - به عبارتی بیش از ۱۰۰ میلیون تن آن - توسط آهن اسفنجی تامین میشود.
به ازای هر تن تولید فولاد از طریق کوره بلند-کنورتور ۲/ ۲ تن گاز CO۲ و از طریق کوره قوس ۴/ ۰ تن گاز CO۲ تولید میشود و منابع دیگر تولید گاز CO۲ در فرآیند احیا مستقیم را ۴/ ۱ تن اعلام کردهاند.
راهکارهای پیشنهادی کاهش تولید گاز CO۲ توسط صنعت فولاد در بخش بالادست تولید چیست؟
توسعه کشورها به افزایش تولید فولاد وابسته است و تنها راه کاهش تولید گاز CO۲، اصلاح روشهای تولید و تغییرات تکنولوژی است. از آنجایی که سرمایهگذاری عظیمی برای تولید فولاد از طریق کوره بلند-کنورتور لازم است و تغییر این روش به سادگی و در زمان محدود امکان پذیر نیست، برخی به عنوان یک برنامه بلندمدت جایگزینی روش احیای مسقیم و استفاده از گازهیدروژن برای تولید آهن اسفنجی و بهکارگیری کوره قوس جهت تولید مذاب را پیشنهاد میدهند.
چالش های این پیشنهاد چیست و این پیشنهاد چقدر قابل اجراست؟
البته در این راه مشکلاتی نیز وجود دارد و مهمترین آن هزینه تولید هیدروژن میباشد. برای تولید یک تن آهن اسفنجی حدود ۲/ ۵۶ کیلوگرم هیدرژن نیاز است که در حال حاضر تولید هر کیلوگرم هیدروژن بیش از ۳ دلار هزینه میبرد. شرکتهای صاحب دانش از جمله شرکت لینده به شدت بر تولید هیدروژن و همچنین ابداع روشهای جدید تولید، جهت کاهش هزینه و اقتصادی نمودن استفاده آن تمرکز کردهاند. اخیرا قرارداد تاسیس یک آزمایشگاه مشترک بین شرکت نفتی آرامکو و شرکت لینده برای تولید هیدروژن از آمونیاک منعقد شده است. به موازات برخی از تولیدکنندگان فولاد از طریق کوره بلند به استفاده از هیدروژن بهصورت تزریق روی آوردهاند که آمارهای انتشار یافته حدودا ۱۰% کاهش در تولید گاز CO۲ را نشان میدهد ولی بهدلایل تکنولوژیک استفاده از هیدروژن در کوره بلند بسار محدود است. از آنجایی که کشور چین بزرگترین تولیدکننده گاز CO۲ است، بهشدت به احداث واحدهای اسفنجی روی آورده است و قرارداد احداث اولین کارخانه احیا مستقیم برپایه هیدروژن کامل به ظرفیت یک میلیون تن را منعقد کرده است. شرکت POSCO بهعنوان یکی از تولیدکنندگان بزرگ فولاد برمبنای کوره بلند - کنورتور با کمک شرکت PRIMETALS - که قبلا فرآیندهای COREX و FINMET را توسعه داده بودند - با ترکیب این دو فرآیند تکنولوژی FINEX را بهوجود آورده که فرآیند آگلومراسیون و ککسازی را حذف نموده و با استفاده از سنگآهن با دانهبندی ریز و زغالسنگ غیرککشو مدعی کاهش ۵۰ درصدی CO۲ ، ۸۱ درصد Sox ، ۹۰ درصد NOx و ۴۸ درصد غبار شده است و میخواهند این فرآیند را جایگزین کوره بلندهای مرسوم کند.
تهدیدها و فرصتها برای تولیدکنندگان جهانی فولاد در مواجهه با این مهم چیست؟
آثار زیستمحیطی تولید گاز CO۲ و تخریب سراسری و پیوستگی اثرات آن در سطح کل کره زمین موجب اتخاذ تصمیمات شدید محدودکننده برای تولیدکنندگان فولاد و اعمال آن در سالهای آتی که موجب افزایش هزینههای تولید و از دست دادن بازارهای فروش و صادرات خواهد شد.
بدین لحاظ تولیدکنندگانی که در کنترل آلودگیها و حرکت به سمت تولید بهاصطلاح فولاد سبز پیشرو باشند از فرصتهای بهتری برخوردار خواهند شد و آنهایی که در این زمینه سستی نموده و عقب بیافتند با تهدیدهایی در ادامه راهشان روبهرو خواهند بود.
درست است که جنگ اوکراین موجب تضعیف کنترل منابع آلودهکننده محیط زیست و استفاده مجدد از منابع بیشتر آلودهکننده تولید انرژی شده است اما باید پذیرفت که این شرایط موقت خواهد بود و کنترل آلودگی کره زمین راهی اجباری است که بشر باید طی کند.
خوشبختانه بخش تولید فولاد ایران که در حال حاضر رتبه دهم تولیدکننده در جهان را دارد در این راه با مراحلی که تاکنون طی کرده است نسبت به بسیاری از تولیدکنندگان بزرگ در جهان پیشرو است؛ هر چند تا رسیدن به نقطه مطلوب فاصله قابل توجهی دارد.