ریسک و فرصت زیرمجموعههای معدنی بورس تهران بررسی شد
پتانسیل سنگآهنیها در مسیر رشد
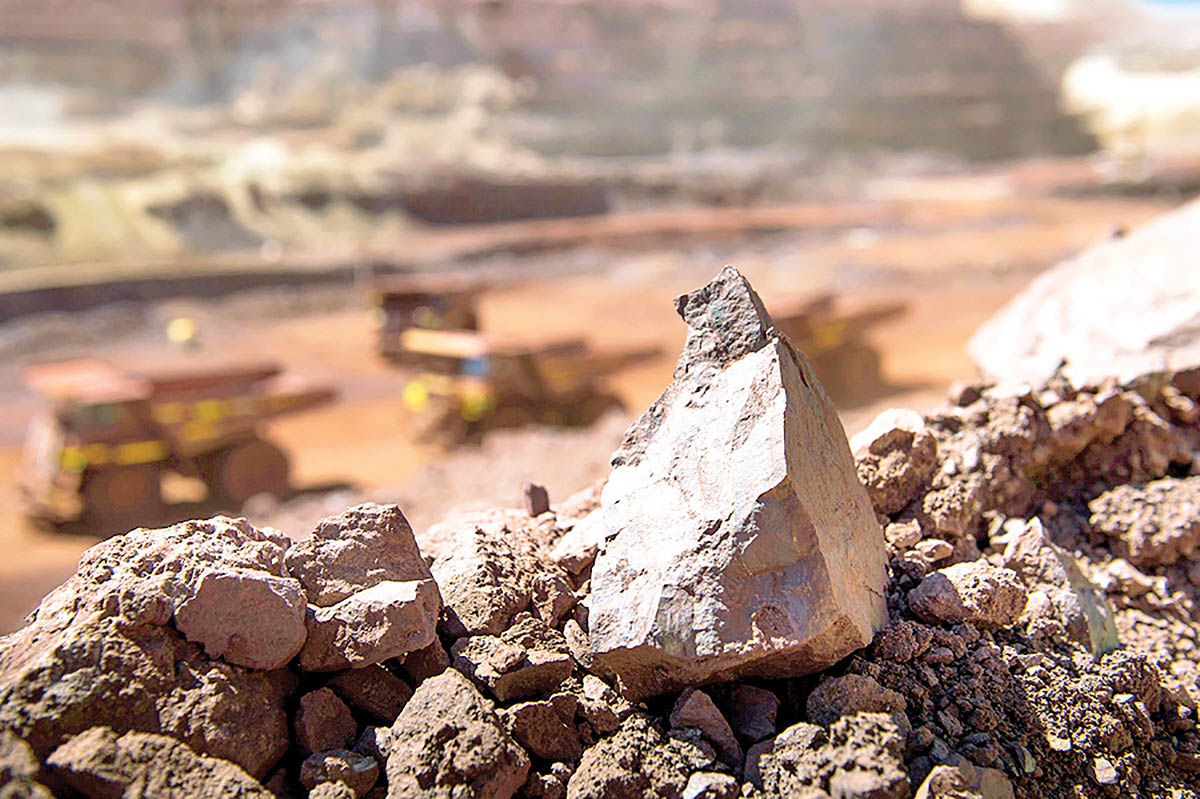
سنگآهن، انواع و کاربرد آن
آهن به عنوان ستون فقرات دنیای پیرامون ما و اولین ماده از زنجیره ساخت فولاد، اهمیتی استراتژیک دارد. با توجه به فراوانی سنگآهن در طبیعت و ارزان بودن آن به نسبت دیگر فلزات، از این فلز میتوان از ساخت خودرو تا سوزن، از لوازم خانگی تا خانه، از ریل قطار تا پل بهره برد. آهن موجود در طبیعت به میزان بسیار کمی به شکل خالص و بیشتر در قالب سنگآهن (Iron Ore) یافت میشود. کانیهای سنگآهن برحسب میزان آهن خالص و آرایش شیمیایی در انواع مختلفی در طبیعت یافت میشود که مهمترین آنها عبارتند از: مگنتیت (4/ 72درصد آهن)، هماتیت (9/ 69درصد آهن)، لیمونیت (8/ 59درصد آهن) و سیدریت (2/ 48درصد آهن). مهمترین عامل در خصوص ارزش سنگآهن، میزان آهن خالص موجود در آن یا عیار سنگآهن است که معمولا در بازه 17 تا 72درصد قرار دارد، میانگین جهانی عیار سنگآهن، 47درصد و میانگین عیار سنگآهن در ایران 46درصد است. باید تاکید کرد استخراج ذخایر با عیار کمتر از 30درصد معمولا اقتصادی نیست. کانیهای سنگآهن همراه با ناخالصیهای مختلف مثل: اکسید سیلیسیم، کربنات کلسیم، گوگرد، منگنز، ترکیبات فسفردار و... در طبیعت یافت میشوند. دیگر کانیهای موجود در سنگآهن که مجموع آنها «باطله» نامیده میشود، از عوامل مهم کیفیت سنگآهناند. وجود باطله، علاوه بر ایجاد هزینههای استخراج بیشتر، کیفیت فولاد تولیدی را نیز تحتتاثیر قرار میدهند؛ به علاوه برخی عناصر همراه مانند فسفر و گوگرد نیز میتوانند به تجهیزات فنی آسیب وارد کنند.
ذخایر سنگآهن قابل استخراج جهانی طبق آخرین آمارهای سازمان زمینشناسی ایالات متحده، تا پایان سال 2020 به میزان 180میلیارد تن تخمین زده شده است. استرالیا، برزیل، چین، روسیه و اوکراین 5 کشور بزرگ تولیدکننده سنگآهن در دنیا هستند اما در هند، ایالات متحده آمریکا، کانادا و آفریقای جنوبی نیز مقادیر قابلتوجهی سنگآهن تولید میشود. در ایران اما ذخایر زمینشناسی سنگآهن حدود 5میلیارد تن برآورد شده است که از این میزان 3/ 3میلیارد تن جزو ذخایر قطعی است. عمده ذخایر سنگآهن ایران دارای زمینه مگنتیتی و به مقداری اندک از نوع هماتیتی است.
با توجه به مقاومت اندک آهن خالص در برابر اکسیداسیون و عدماستحکام آن، عناصر دیگری همچون کربن، نیکل، کروم و منگنز با آهن ترکیب میشوند تا آلیاژهایی با مصارف متفاوت تولید شود. فولاد به عنوان مهمترین این آلیاژها که با ترکیب آهن و کربن تولید میشود، بیش از 98درصد از مصرف سنگآهن استخراج شده را به خود اختصاص داده است. این موضوع علت وابستگی قیمت سنگآهن به عوامل موثر بر تقاضای محصولات فولادی را به خوبی توضیح داده و اهمیت آگاهی از فرآیند تولید فولاد، به عنوان اصلیترین محصول سنگآهن را روشن میسازد.
فرآیند تولید فولاد
سنگآهن پس از استخراج و پیش از انتقال به کوره احیا، باید از نظر شرایط فیزیکی، دانهبندی و نیز حذف بخش عمده ناخالصیها، فرآوری شود. فرآوری سنگآهن در چند مرحله به شرح زیر صورت میگیرد:
۱- غربال کردن: با توجه به اینکه در مرحله استخراج، سنگهای معدنی با ابعاد مختلفی به دست میآیند، لازم است سنگهای ریزتر توسط سرند جدا شوند. این موضوع منجر به کاهش وزن خوراک ورودی به سنگشکن میشود.
۲- خرد کردن: تکههای بزرگتر سنگآهن در این مرحله جهت انتقال به آسیاب خرد میشود. فرآیند موصوف بر اساس جنس و درجه سختی سنگ، در چند مرحله توسط سنگشکنها انجام و ماده معدنی حاصل برای آسیاب کردن دپو میشود.
۳-آسیاب کردن: سنگآهن پس از خرد شدن، آسیاب شده و مواد حاصل، توسط صفحه لرزان مجددا به ذرات کوچک و بزرگ غربال میشوند و تکههای بزرگ مجددا به مراحل پیشین بازمیگردند.
۴-جدایش و پرعیارسازی: به طوری کلی برای فرآوری دو کانی اصلی سنگآهن به نامهای مگنتیت و هماتیت روشهای متداول زیر استفاده میشود: برای کانسنگهای مگنتیتی مراحلی شامل جدایش مغناطیسی با شدت کم و فلوتاسیون برای حذف ترکیبات سولفور، فسفر و سیلیکات استفاده میشود؛ برای کانسنگهای هماتیتی مراحل مختلفی شامل جدایش ثقلی، جدایش مغناطیسی با شدت بالا، سایش به منظور تمیز کردن، نرمهگیری و فلوتاسیون برای حذف ترکیبات سولفور، فسفر، سیلیکات و رس مورد استفاده قرار میگیرد.
۵- احیا: سنگآهن فرآوری شده پس از طی مراحل فوق، به صورت سنگآهن دانهبندیشده، کنستانتره و گندله به واحد احیاء منتقل میشود. به طور کلی روشهای تولید فولاد به سه دسته کلی کوره بلند (Blast Furnace)، احیای مستقیم (Direct reduced iron) و احیا از طریق ذوب (Smelting Reduction Process) قابل تقسیماند که بیش از 70درصد فولاد جهان از طریق روش کوره بلند تولید میشود اما به دلیل آلودگیهای زیست محیطی، روش احیای مستقیم به سرعت در حال پیشرفت است.
قیمتگذاری سنگآهن در ایران
نرخگذاری سنگآهن در ایران همواره محل مناقشه شرکتهای فولادی و سنگآهنی بوده و در این راستا و در جهت حل این موضوع، در سال 97، فولادسازان و واحدهای سنگآهن روی فرمول قیمت کنسانتره، گندله و آهن اسفنجی بر روی ضرایب 16درصد، 5/ 23درصد و 50درصد شمش فولاد خوزستان توافق کردند. در سالهای 98 و 99، مذاکرات شرکتهای سنگآهنی با فولادسازان منجر به نتیجه نشده و در نهایت در دی ماه سال 99، متعاقب شکایت «انجمن تولیدکنندگان و صادرکنندگان سنگآهن ایران» دیوان عدالت اداری طی حکمی بخشنامه مورخ 06/ 05/ 98 وزارت صمت در جهت تثبیت ضرایب قیمتی مزبور را ابطال کرد. در پایان سال 99، عرضه محصولات سنگآهنی شرکتهای پذیرفته شده در بازار سرمایه آغاز شد. قیمتهای جدید بسته به کیفیت محصولات و رقابت در بورس کالا تعیین میشود اما در نهایت در محدوده خاصی به نسبت شمش فولاد خوزستان قرار دارد. در این میان، حتی محصولاتی که در بورس کالا نیز عرضه نشدهاند، بر اساس گزارشهای ماهانه با افزایش نرخ مواجه شدهاند.
ریسکهای صنعت سنگآهن
کمبود آتی سنگآهن: بر اساس مطالعات انجام شده توسط ایمیدرو پیرامون ذخایر سنگآهن کشور، در صورت تولید 55میلیون تن فولاد خام در افق 1404 و تولید کامل مطابق برنامه واحدهای فولادی، ذخایر کشور تقریبا تکافوی حدود 12 تا 13 سال پس از افق 1404 را خواهد داد؛ اما با روند فعلی تولید سنگآهن به میزان 30میلیون تن در سال، ذخایرسنگآهن برای حداقل 18 سال کافی به نظر میرسد. گرچه با توجه به تعدد طرحهای فولادسازی در کشور و کمبود 31میلیون تنی سنگآهن برای تولید 55میلیون تن فولاد در افق 1404، مهمترین چالش دستیابی به برنامه تولید فولاد در افق مزبور، دسترسی به منابع سنگآهن است. بر مبنای همین ریسک، تلاشهایی جهت اکتشافات هرچه بیشتر و در سطوح عمیقتر و سرمایهگذاری در معادن برونمرزی (جوینت ونچر کگل، کچاد و فکورصنعت با هدف تملک معدن سنگآهن در استرالیا) در جهت مواجهه با این موضوع انجام شده است.
احتمال افزایش حق مالکانه و حق انتفاع: با توجه به کسری بودجه دولت در سال 1400 و نیاز به منابع هرچه بیشتر، احتمال افزایش حقوق مالکانه و انتفاع وجود دارد. باید اشاره کرد در سالهای پیشین، حقوق مالکانه و انتفاع دریافتی از شرکتهای سنگآهنی، اغلب با تخفیف همراه بوده و افزایش مزبور میتواند در قالب عدمتداوم تخفیفات پیشین یا افزایش ضرایب محقق شود.
چالش دسترسی به انرژی: قطعیهای مکرر برق در کنار افزایش بیسابقه قیمت جهانی گاز و تداوم این شرایط، یکی از مهمترین مسائل شرکتهای سنگآهنی است. این موضوع در تابستان امسال، غالب شرکتهای فلزی و معدنی حاضر در بازار سرمایه را با افت تولید مواجه کرد. از مهمترین اثرات این موضوع، اجبار شرکتهای سنگآهنی به عرضه برق نیروگاههای تحت مالکیتشان به شبکه سراسری توزیع برق در تابستان است که به خوبی نشانگر سطح محافظت از حقوق مالکیت است. به علاوه با عنایت به ناترازی شدید بودجه سال 1400، افزایش نرخ مجدد حاملهای انرژی به امری ناگزیر مبدل شده است. همچنین با توجه به مصوبه هیات وزیران مبنی بر افزایش نرخ سوخت نیروگاهی طی پنج سال آتی، رشد نرخ برق مصرفی واحدهای سنگ آهن و فولادی قابل پیشبینی است.
ریسکهای مربوط به نرخ سنگآهن: هم اکنون قیمتگذاری غالب محصولات سنگآهنی به نسبت شمش فولاد خوزستان و بر مبنای رقابت در بورس کالا تعیین میشود. سایر محصولاتی از هر شرکت که در بورس کالا عرضه نشده نیز با توجه به عرضه دیگر محصولات زنجیره، به نسبت سال قبل با افزایش نرخ مواجه شده است. به نظر میرسد با توجه به چالشهای پیرامون تامین سنگآهن و عدمتوازن سرمایهگذاری در بالا و پاییندست زنجیره، ضرایب فعلی به نسبت قیمت شمش فولاد خوزستان را بتوان حداقل ضرایب در نظر گرفت. از سوی دیگر وجود ریسکهایی همچون احتمال نرخگذاری دستوری در صنعت فولاد و کاهش قابل انتظار نرخ جهانی فولاد نیز باید مدنظر قرار گیرد.
ریسک دسترسی به بازارهای صادراتی: در سالجاری، متاسفانه به علت تداوم محدودیت در صادرات از طریق اعمال تعرفههای سنگین صادراتی، شرکتهای تولیدکننده سنگآهن فرصت کمنظیر صادرات با نرخهای بیسابقه محصولات خود را از دست دادند. با توجه به قطعی برق واحدهای فولادی در تابستان امسال، تقاضا برای محصولات سنگآهن کاهش محسوسی داشته که این موضوع در نهایت منجر به دپوی کنسانتره و گندله در انبارهای این شرکتها شده است، در حالی که اگر امکان صادرات وجود داشت، با چنین موضوعی مواجه نمیشدیم. بنابراین برای دسترسی به بازارهای صادراتی متاسفانه افق و برنامهریزی روشنی در این صنعت موجود نیست.