حکایت پرفراز و نشیب تولید فولاد در ایران - ۵ اسفند ۸۶
دکتر مهندس سیدتقی نعیمی، تحصیلکرده و مدرس دانشگاههای اتریش و آلمان از سال ۱۳۵۱ به عنوان عضو هیات علمی در دانشگاه علم و صنعت مشغول تدریس و تحقیق بوده است. وی همچنین نویسنده کتاب «طرز تهیه و موارد مصرف آهن اسفنجی» است.
این کتاب در سال ۱۳۵۷ به زبان آلمانی نگاشته شده است. وی در سال ۱۳۶۵ مشاور مجتمع فولاد خوزستان بوده و تنها استاد متالورژی دانشگاههای ایران است که کارشناس رسمی دادگستری نیز است.
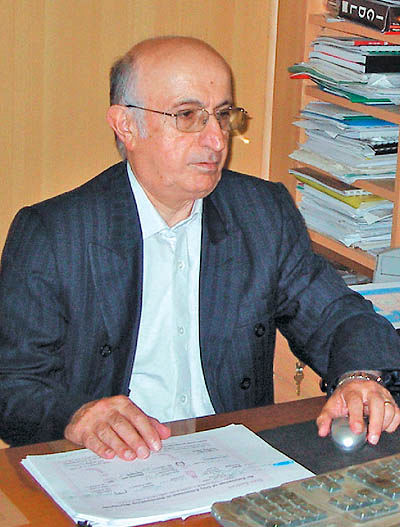
دکتر مهندس سیدتقی نعیمی، تحصیلکرده و مدرس دانشگاههای اتریش و آلمان از سال ۱۳۵۱ به عنوان عضو هیات علمی در دانشگاه علم و صنعت مشغول تدریس و تحقیق بوده است. وی همچنین نویسنده کتاب «طرز تهیه و موارد مصرف آهن اسفنجی» است.
این کتاب در سال 1357 به زبان آلمانی نگاشته شده است. وی در سال 1365 مشاور مجتمع فولاد خوزستان بوده و تنها استاد متالورژی دانشگاههای ایران است که کارشناس رسمی دادگستری نیز است. دکتر نعیمی در حال حاضر عضو هیات علمی دانشکده تحصیلات تکمیلی دانشگاه آزاد اسلامی واحد تهران جنوب میباشند. با توجه به دههامقالهای که از تیرماه 86 تاکنون در نشریات تخصصی به قلم دکتر نعیمی در ارتباط با فولاد و مسائل جنبی آن منتشر شده است، روزنامه دنیای اقتصاد بر آن شد تا به بهانه انتشار ویژه نامه فولاد گفتوگویی با وی داشته باشد. آنچه در ادامه میخوانید مشروح مصاحبه «دنیای اقتصاد» با ایشان در ارتباط با آخرین دستاوردهای صنعت فولاد است.
گفتوگو از: بهنود دامغانی
* آقای دکتر نعیمی لطفا مختصری درباره تاریخچه تولید آهن و فولاد در ایران و اینکه چرا در ایران تا سال 1346 فولاد تولید نشده، بفرمایید؟
عملیات باستان شناسی در حاشیه تپه سقزآباد قزوین موید وجود سنگهای معدنی آهن با عیار بالا، سربارههای آهن و کلوخههای آهن اسفنجی که شکل خاصی ندارند، میباشد. این اکتشافات تاییدکننده رواج دانش فنی فلزکاری (آلیاژهای مس و قطعات آهنی) در ایران باستان است.
از یک گودال زباله که مربوط به عصر آهن (حدود 800 الی 1100سال پیش از میلاد) در اطراف سقز آباد قزوین میباشد، تعداد زیادی اشیاء فرسوده تولید شده از آهن شامل تیغههای خنجر، چاقو و داس بهدست آمده است. این یافتهها موید این میباشد که در این دوره تولید اشیاء آهنی در این منطقه از کشور ما رواج داشته است.
آثار باقی مانده از بهرهبرداری سنگ آهن معدن گل گهر موید شناخت ایرانیان در ۲۰۰۰ سال قبل برای تولید ابزار فولادی بوده است. در دوران سلطنت نادر شاه افشار متاسفانه به جای گسترش تولید فولاد به تزیین مصالح و ابزار فولادی روی آوردند. (طرحهای مختلفی برای تولید فولاد حتی قبل از ایجاد حکومت مشروطه توسط افراد خیر اندیش و وطن پرست ارائه شد. به علت کارشکنیهای انگلستان و روسیه تزاری این طرحها به اجرا نرسیدند. در سال ۱۸۸۷ میلادی حاج محمد حسن امینالضرب اجازه تاسیس کارخانه تولید آهن را از ناصرالدین شاه گرفت.) قرار بود کوره بلندی به ظرفیت ۱۰۰هزار تن که بیشترین ظرفیت کورههای بلند آن زمان دنیا بود در مازندران احداث شود. تجهیزات این کارخانه به فرانسه سفارش داده شد؛ اما با ترفندهای مزورانه انگلستان این طرح به نتیجه نرسید و امینالضرب به دولت فرانسه خسارت پرداخت کرد.
در سال 1304 (1925 میلادی) مجلس شورای ملی وقت دولت را موظف به تاسیس یک کارخانه تولید آهن به ظرفیت 50هزار تن نمود. این طرح نیز به دست فراموشی سپرده شد. از آن سال مجالس مختلف شورای ملی کرارا توجه دولتها را به تاسیس کارخانه ذوبآهن جلب میکردند.
در سال ۱۳۱۲ قرار شد با بررسیهایی که به عمل آمده بود، یک کارخانه تولید آهن و فولاد در امینآباد شهر ری تاسیس شود. این پروژه هم متاسفانه عملی نشد.
در سال 1316 بین دولت ایران و شرکتهای کروپ و دماک آلمان قرار دادی برای نصب تجهیزات و راهاندازی یک کارخانه تولید فولاد به ظرفیت 100هزار تن منعقد شد. پس از بررسیهای لازم محل کارخانه در کرج انتخاب شد. قرار بود این کارخانه تیر آهن، ریل قطار، میلگرد و ورق فولادی تولید کند. اقدامات اولیه برای تاسیس این کارخانه قبل از سال 1320 شروع شد. اما متاسفانه کشتی حامل قسمت عمده تجهیزات این کارخانه دانسته توسط انگلیسیها غرق شد. در سال 1332 طرح تاسیس کارخانه تولید آهن و فولاد در ازنا پیشنهاد شد. قرار بود کورههای قوس الکتریکی در 4 مرحله به ظرفیت نهایی 300هزار تن با استفاده از انرژی برق آبی تاسیس شود. این طرح نیز به علت مخالفت غربیها عملی نشد.
قرارداد دیگری در سال ۱۳۳۴ برای تاسیس کارخانه تولید آهن و فولاد بین دولت ایران و کنسرسیومی از شرکتهای کروپ و دماک آلمان منعقد شد. تجهیزات مورد نظر فاز اول عبارت بودند از دو کوره قوس الکتریکی و دو کوره زیمنس مارتین و در فاز دوم نیز قرار بود از سیستم مدرن LD هم استفاده شود. این طرح با مخالفت آمریکا و صدر اعظم وقت آلمان اجراء نشد.
زنده یاد مرحوم مهندس حامی که میزبان صدراعظم آلمان در ایران بود،به ایشان گوشزد کرد که ملت ایران قوت لایموت خود یعنی گندم را به عنوان بهای کارخانه ذوبآهن در زمان جنگ به آلمان داد. دولت فعلی آلمان که خود را جانشین آلمان سابق میداند باید به تعهدات خود عمل کند و نسبت به اجرایی شدن تاسیس کارخانه تولید فولاد در ایران اقدام نماید. صدر اعظم آلمان در پاسخ گفت به فکر پروژههای تخیلی مانند داشتن کارخانه تولید فولاد برای کشورتان نباشید. مرحوم مهندس حامی به ایشان فرمودند: حتی بدون حمایت شما هم به امید خدا ایران دارای صنعت فولاد خواهد شد.
در سال ۱۳۳۹ مطالعات مجدد برای ایجاد کارخانه فولاد در محل نیمه تمام کارخانه کرج انجام گرفت. در آخرین مرحله بانک جهانی به علت اعمال نفوذ آمریکا از دادن اعتبار برای اجرایی شدن این طرح خودداری کرد. در همین سال مطالعاتی توسط فرانسویها برای تاسیس ۲ کوره بلند، کورههای قوس الکتریکی، کنورتور LD و تجهیزات نورد به ظرفیت ۶۰۰هزار تن انجام گرفت. پس از مطالعات لازم اصفهان برای محل ایجاد کارخانه مناسب تشخیص داده شد. سنگ آهن مورد نیاز این کارخانه قرار بود از معدن چغارت و ذغال سنگ از معادن البرز و کرمان تامین شود. این پروژه نیز به علت اعمال نفوذ کشورهای غربی اجرایی نشد.
در سال 1342 اقدامات اولیه برای تاسیس کارخانه نورد ایران با ظرفیت اولیه 65هزار تن توسط بخش خصوصی شروع شد. این طرح در سال 1346 با مواد اولیه خارجی در اهواز شروع به تولید نمود.
در سال ۱۳۵۱ با استفاده از شمش خارجی این کارخانه تولید تیر آهن به ظرفیت ۱۵۰هزار تن را شروع کرد. در جوار این کارخانه ۴ کوره قوس الکتریکی هر یک به ظرفیت ۵۰تن نصب شدند. ظرفیت سالانه این چهار کوره ۳۶۰هزار تن و خوراک آنها قرار بود قراضه وارداتی باشد.
در سال 1344 حکام شوروی سابق ناظر بر فعالیتهای آمریکایها در ایران بودند. روسها از تمایل ایرانیان به داشتن کارخانه تولید فولاد واقف بودند و میدانستند فقط به اسم مطالعات مختلف برای تولید فولاد میتوانند پایگاهی در ایران داشته باشند. از این رو برای آگاهی بیشتر از تجهیزات شنود آمریکاییها در ایران و....... از این مسیر وارد عمل شدند. در طی احداث کارخانه چند برابر پول تاسیس یک کارخانه را به تدریج از ایران گرفته اند. ولی هر بار با دسیسه غربیها یا خود روسها از اجرای پروژهها جلوگیری شد.
سرانجام به دولت ایران پیشنهاد تاسیس کارخانه تولید فولاد را داد و قرار شد پول این کارخانه را ایران با صادرات گاز طبیعی به شوروی پرداخت نماید. روسها برای تاسیس این کارخانه کار مهندسی جدیدی انجام ندادند. بلکه پروژهای را که برای یک کشور دیگری با شرایط محیطی آنجا و مواد اولیه آن کشور طراحی کرده بودند، بدون تغییر و به روز کردن تجهیزات آن در ایران نصب نمودند. به بهانه همکاری برای تاسیس کارخانه ذوبآهن نیز جاسوسان روسی به تعداد زیاد وارد ایران شدند و ایران عملا جولانگاه جاسوسان روس و آمریکا شد.روسها به خودشان زحمت ندادند حداقل جزییات قسمتهای مختلف کارخانه را با مهندسین روسی آشنا به شرایط ایران در میان بگذارند. زیرا در این صورت مسلما میدانستند سنگ آهن معدن چغارت ایران که روسها مشاور آنجا هم بودند، مانند سنگ آهن لهستان رطوبت زیادی ندارد که احتیاج به نصب سنگ خشکن در کارخانه ذوبآهن اصفهان باشد. روسها به پول این ملت تجهیزات سنگ خشک کنی را در کارخانه ذوبآهن اصفهان نصب کردند. در مقابل انتقاد متخصصان ایرانی در زمان راهاندازی کوره اول اصفهان جوابی برای این اشتباه فاحش مهندسی خود نداشتند. رییسجمهور روسیه شوروی از
این اشتباه مهندسی معذرت خواهی نمود. علاوهبر این تکنولوژی سیستم ریختگری مداوم نصب شده توسط روسها در ذوبآهن اصفهان بروز نبود. یکی از نواقص فنی ذوبآهن اصفهان همین سیستم ریختگری مداوم عمودی آن بودکه حتی در زمان جنگ تحمیلی نیز ما نتوانستیم به نحو احسن از تولیدات مجتمع ذوبآهن اصفهان بهرهمند شویم.
آقای دکتر نعیمی قدری در ارتباط با روند تولید فولاد در ایران از سال 1351 تاکنون و مقایسه آن با روند مصرف فولاد در ایران مطالبی بیان بفرمایید.
مصرف فولاد در ایران از سال ۱۳۵۱ تاکنون به فاکتورهای مختلفی ازجمله، میزان فروش و تغییرات قیمت نفت، وضعیت اقتصادی و سیاسی، درگیریهای نظامی و...... وابسته بوده است. به طوری که در سالهای ۱۳۵۵ و ۵۶ به برکت فروش ۶میلیون بشکه در روز نفت و افزایش قیمت نفت و سوزاندن حدود ۳۶میلیارد مترمکعب گاز در سال بدون استفاده مفید از آنها، اجبارا دولت وقت تسهیلاتی برای واردات کالاهای مختلف ازجمله واردات محصولات فولادی قائل شد.
در نتیجه کل مصرف فولاد ایران در سال 1356 حدود 4میلیون تن بود که تقریبا سه چهارم این مصرف با واردات تامین شد. مصرف سرانه فولاد ایران در سال 1356 حدود 125کیلوگرم بود. از سال 1356 تولید داخلی فولاد و واردات کاهش یافت. به طوری که کل مصرف فولاد ایران در سال 1359 قدری کمتر از 2میلیون تن و مصرف سرانه فولاد خام به حدود 70کیلوگرم رسید. در سال 1373 واردات فولاد به حداقل خود رسیده و تولید داخلی قدری افزایش یافت.
با وجود افزایش صادرات مصرف فولاد با تولید برابری کرده است. نوسانات واردات و مصرف فولاد تا سال ۱۳۷۸ ادامه داشت. در این سال مجددا صادرات و واردات فولاد ایران مساوی شده و عملا مصرف داخلی فولاد با تولید برابری نمود. از این سال به بعد تولید داخلی فولاد افزایش یافته، ولی رشد واردات فولاد چند برابر رشد تولید داخلی فولاد بوده است. مصرف سرانه فولاد خام از ۱۲۰کیلوگرم در سال ۱۳۷۸ تا سال ۱۳۸۵ به بیش از ۲۰۰ کیلوگرم رسید. با توجه به ثبت سفارش، واردات فولاد خام و محصولات فولادی در سال ۱۳۸۶ افزایش زیادی نسبت به سال ۱۳۸۵ خواهد یافت. پیشبینی میشود مصرف سرانه فولاد خام ایران در سال ۱۳۸۶ حدود ۲۵۰کیلوگرم خواهد بود.
برای تولید فولاد به سنگآهن، مواد انرژیزا و.... نیاز است. همانطوری که در 4 مقالات منتشر شده در روزنامه دنیای اقتصاد و 8 مقاله منتشرشده در هفته نامه معدن و توسعه از تیرماه 1386 تاکنون کرارا ذکر کردم، خوشبختانه خداوند ما را از این مواد اولیه بیش از سایر کشورها بهرهمند ساخته است. با مدیریت درست ایمیدرو در چند سال اخیر نیاز به واردات سنگ آهن برای تولید فولاد مانند سالهای 1383 و 82 نداشتهایم. علاوهبر این در سه سال اخیر چندین میلیون تن هر ساله سنگآهن دانهبندی شده صادر کردهایم. کوره بلند سوم ذوبآهن اصفهان و گندلهسازی مجتمع معدنی گلگهر و ... . که قرار بود تا دی ماه 1386 مورد بهرهبرداری قرار گیرند، مورد بهرهبرداری قرار نگرفتهاند. علل تاخیر در بهرهبرداری به موقع طرحهای عمرانی کشور بسیار زیاداست. از جمله روابط سیاسی ایران با سایر کشورها، بروکراسی متداول در سایر ارکانهای کشور مانند بانکها و ... . میباشند.
به برکت افزایش قیمت نفت متاسفانه رشد واردات محصولات فولادی در سال ۱۳۸۶ چند برابر رشد تولید داخلی فولاد خواهد بود. همانطوری که در قسمت تاریخچه تولید فولاد بیان کردم، کشورهای غربی و شرقی انواع محصولات فولادی ساده ساختمانی مصرفی را با میل و به میزان کافی به ایران میفروشند. ولی با کارشکنیهای مزدورانه خود اختلالاتی در رشد صنایع ایران به وجود میآورند. مدیریت کلان تصمیمگیری کشور باید به جای خرج کردن بیرویه ارز برای واردات کالای عمدتا مصرفی همت خود را در افزایش تولید داخلی بکار گیرند و سیستم بروکراسی ثبت سفارش، افتتاح حساب اعتبار اسنادی و ... . که متاسفانه برای کالای سرمایهای خیلی بیشتر از کالای بنجل مصرفی است را به حداقل ممکن برسانند تا طرحهای صنعتی در مقیاس ملی کشور مشابه کوره بلند سوم ذوب اصفهان هرچه زودتر راهاندازی شوند و ایجاد اشتغال نمایند.
آقای دکتر نعیمی به نظر شما آینده صنعت فولاد در دنیا چگونه خواهد بود؟
همانطوری که قبلا در مقالات منتشره بیان کردم از سال ۱۹۱۸ تا سال ۱۹۴۵ تغییرات جهانی تولید فولاد از یک آرامش نسبی برخوردار بوده است که به دوران اول آرامش رشد تولید فولاد معروف شد. در این دوران میانگین رشد جهانی سالانه فولاد ۲درصد بود. از سال ۱۹۴۵ تا ۱۹۷۳ رشد جهانی تولید فولاد سالانه سرسام آور بوده به طوری که میانگین این رشد جهانی سالانه در این دوران ۷درصد بوده است.
تولید جهانی فولاد از سال 1973 تا سال 2000 به علت شوکهای افزایش قیمت نفت، سقوط دیوار برلین و سایر وقایع اقتصادی سیاسی میانگین رشد سالانه تولید فولاد دنیا یک درصد بود. این دوره به دومین دوره آرامش رشد تولید فولاد معروف است.
از سال ۲۰۰۰ تا سال ۲۰۰۷ میانگین رشد جهانی سالانه تولید و مصرف فولاد حدود ۵درصد بود. پیشبینی میشود این روند رشد جهانی تولید فولاد در سالهای ۲۰۰۸ تا ۲۰۱۱ با شدت کمتری ادامه داشته باشد و رشد تولید فولاد جهان از سال ۲۰۱۱ دوران آرامش سومی را تجربه خواهد کرد. به عبارت دیگر میانگین رشد تولید فولاد جهان از سال ۲۰۱۱ تا چند سال بعد از آن سالانه حدود یک درصد خواهد بود. یکی از دلایل کاهش رشد جهانی تولید فولاد گسترش استفاده از نانو تکنولوژی در تولید فولاد خواهد بود که منجر به کاهش وزن قطعات مصرفی فولادی میگردد. لذا ارزش افزوده محصولات فولادی به علت تولید مارکهای جدید فولاد چند برابر ارزش فعلی محصولات فولادی در دنیا خواهد شد. البته این ارزش افزوده برای کشورهای صنعتی ایجاد میشود، نه آنهایی که فقط به تولید میلگرد، توری مرغی، تیر آهن و سایر محصولات کم ارزش فولاد ساده کربنی از لحاظ کمی ادامه میدهند. زیرا انقلاب صنعتی دوم یعنی استفاده از نانوتکنولوژی در کلیه صنایع به خصوص در صنعت فولاد در راه است. کشورهایی در آینده موفق خواهند بود که حرکت خود را با حرکت قطار تحولات تکنولوژی هماهنگ کنند تا از کشورهای پیشرفته صنعتی عقب
نماند.
شما در سوال قبل فرمودید، در آینده استفاده از نانوتکنولوژی در تولید فولاد گسترش خواهد یافت. لطفا قدری بیشتر درباره استفاده از نانوتکنولوژی در تولید فولاد صحبت کنید.
اجازه بدهید کمی در ارتباط با انقلاب صنعتی دوم که در راه است صحبت کنم. چون موضوع جدیدی است و احتمالا برای برخی از مهندسان که فرصت مطالعه ندارند، امری ناشناخته می باشد. به طور خلاصه و به زبان ساده بازگو مینمایم. در سال ۱۸۵۷ محلول کلوئیدی طلا توسط مایکل فارادی کشف شد. در سال ۱۹۰۵ آلبرت انیشتین رفتار محلولهای کلوئیدی را تشریح کرد. در سال ۱۹۳۲ ایجاد لایههای اتمی به ضخامت یک مولکول توسط دانشمندان عملی شد. در سال ۱۹۵۹ کار با مواد در مقیاس نانو مطرح گردید. در اوایل دهه ۸۰ قرن گذشته دستگاهی اختراع شد که به کمک آن جابجایی تک تک اتمها با استفاده از آن(STM) ممکن بود. در سال ۱۹۹۱ اولین تز دکتری مهندسی در زمینه نانوتکنولوژی در دانشگاه MIT دفاع شد. در سال ۲۰۰۰ میلادی برنامههای ملی آمریکا در زمینه نانو تکنولوژی به صورت مدون شروع شد. واحد اندازهگیری نانو یک میلیاردم یا ۹-۱۰متر میباشد. نانو تکنولوژی عبارت است از توانمندی تولید مواد ازجمله فولاد، ابزار و سیستمهای جدید با در دست گرفتن کنترل سطوح مولکولی و اتمی و استفاده از خواصی که به علت ابعاد کوچک ذرات در سطوح ایجاد میشود. نانوتکنولوژی یک رشته جدید نیست، بلکه یک
رویکرد جدید در تمام زمینههای مهندسی ازجمله مهندسی تولید قطعات فولادی است. استفاده از فنآوری نانو در آینده موجب ساخت مواد، انواع قطعات فولادی با وزن کمتر و خواص کاربردی بهتر خواهد شد. نانو تکنولوژی ریز ساختاری در ادامه فنآوری میکرو است. استفاده از تکنولوژی نانو موجب میشود تا قطعات فولادی محکمتر، سبکتر، عایق حرارتی بهتر، با فرسایش کمتر و.... تولید گردد.
اجازه بفرمایید قدری از کلیگویی خارج شده و با ذکر مثالهای کاربردی استفاده فنآوری نانو در ارتباط با تولید و مصرف فولادها صحبت کنیم. فولاد ضد زنگ 316L تا چند سال پیش نهایت تکنولوژی جهانی بود. امروزه با استفاده از دانش نانو محققین توانستند در خواص کاربردی این فولاد به صورت جهشوار بهبود ایجاد کنند. تنش تسلیم فولاد 316L معمولی حدود 600مگا پاسگال میباشد. در صورتی که تنش تسلیم همین آلیاژ فقط با ریز شدن دانهها در حد نانو به بیش از 1500 مگا پاسگال رسیده است. به عبارت دیگر هرچه اندازه دانههای فولاد 316L به نانو نزدیکتر شود، تنش تسلیم آن افزایش خواهد یافت. یعنی شکلدهی چنین فولادی به سهولت و با هزینه کم انجامپذیر میباشد. مقاومت به سایش فولاد 316L با کاهش ابعاد دانهها تا حد نانو افزایش چشمگیری مییابد.
پیشبینی میشود در سالهای آینده انواع فولادهای نانو ساختار یکی از تکنولوژیهای کلیدی قرن ۲۱ باشد. در قطعات فولادهایی که به نحوی از نانو تکنولوژی در تولید آنها استفاده میشود میتوان به سختی بالاتر از سختی سرامیکهای آلومینایی و استحکام بالاتر از استحکام فیبرهای پایه کربنی دست یافت. بهرهگیری از نانو تکنولوژی در تولید قطعات فولادی سبب افزایش مقاومت به خوردگی بیش از سوپر آلیاژها با پایه نیکل میشود. همچنین فولادهایی از نانو تکنولوژی به صورت هدفمند در تولید قطعات صنعتی استفاده میشوند. این قطعات دارای نسبت استحکام وزنی بیشتر در مقایسه با قطعات فولادی از آلیاژهای تیتانیوم و جوشپذیری بهتر از آلیاژهای پایه کبالت میباشند.
استفاده از فنآوری نانو در 10 سال آینده تعداد زیادی از تولیدات امروزی بشر را تحت تاثیر قرار خواهد داد. محققین پیشبینی نمودهاند استفاده از فنآوری فرا رشتهای نانو تا سال 2014 در 15درصد انواع تولیدات جهانی از جمله فولاد دخالت خواهد کرد. محصولاتی که با استفاده از نانو تکنولوژی در سال 2014 تولید خواهند شد، بنابر پیشبینی محققین حدود 2600میلیارد دلار به قیمتهای امروزی ارزش خواهد داشت.
با توجه به مزایایی که برای استفاده از نانوتکنولوژی در تولید فولاد بیان کردید، به نظر شما بهتر نیست به جای گسترش کمی تولید فولاد بیشتر در زمینه کسب دانش فنی و تولید فولاد با استفاده از تکنولوژی نانو اقدام کنیم؟
جواب شما منفی است. زیرا استفاده از نانوتکنولوژی در تولید فولاد مشکلات امروزه ایران را که تامین انواع فولاد ساختمانی برای اجرای طرحهای مختلف عمرانی میباشد، بر طرف نمیکند. علاوه بر این قطعات فولادی که با استفاده از نانوتکنولوژی تولید میشوند، عمدتا در صنایع پیشرفته مصرف میشوند. امروزه در کشور ما استفاده از دانش نانوتکنولوژی در تولید فولاد به علت نداشتن چنین صنایعی هنوز مفید نخواهد بود. ولی دانستن اینکه تکنولوژی تولید فولاد دنیا از لحاظ کیفی در چه جهتی در حال تکامل است، برای آینده حائز اهمیت میباشد.
باید توجه نمود که امروزه در صنایع دفاعی میتوان با استفاده از نانوتکنولوژی به پیشرفتهای بیشتری دست یافت یا در ساخت قطعات ماهواره تحقیقاتی که به امید خدا در آینده نزدیک برای مقاصد صلح جویانه مانند کشاورزی، هواشناسی، کنترل هوشمند وسائل نقیله و .... به فضا خواهیم فرستاد، استفاده نمود. لذا مدیران صنایع تولید فولاد کشور باید از هم اکنون مطالعاتی برای دانستن جزئیات فنی این تکنولوژی از لحاظ تئوری به عمل آورده و زیربنای لازم برای استفاده از این تکنولوژی را در سالهای آینده فراهم نمایند. علاوه بر این لازمه استفاده از نانوتکنولوژی در تولید فولاد، تامین مواد اولیه آهندار با کیفیت مناسبی است که معادن ما امروزه از تولید آن عاجزند.
امید است مدیران صنایع معدنی ما نیز از هم اکنون بررسی لازم برای تامین کیفی سنگآهن جهت استفاده از تکنولوژی نانو برای تولید فولاد از آنها را انجام داده و آمادگی لازم را با سفارش تجهیزات خطوط تغلیظ جدید بر مبنای آخرین دستاوردهای تکنولوژی روز دنیا به جای کپیکاری خطوط موجود که از تکنولوژی چند دهه قبل میباشد، به دست آورند.
به نظر شما که استاد دانشگاه هستید، چرا اکثر مهندسان ما به خصوص مهندسین معدن و متالورژی در طی تحصیلات کلاسیک خود با نانوتکنولوژی آشنا نمیشوند؟
همان طوری که گفته شد نانوتکنولوژی دانش جدیدی است. اکثر برنامههای درسی ما بعد از انقلاب فرهنگی تدوین و تصویب شدهاند. برخی از این برنامهها هنوز به روز نشده و با توجه به محدودیت بودجههای خرید مجلات علمی و تحقیقاتی منابع زیادی در ارتباط با نانوتکنولوژی در اختیار استادان از طرف مسوولان کشور قرار نگرفته است. فعالیتهای جزئی در ارتباط با استفاده از نانوتکنولوژی هم اکنون در مهندسی پزشکی و آموزش رشتههای تخصصی پزشکی به عمل آمده و بیشتر به صورت تئوری هم تدریس میشود. در همین حد حداقل لازم است در گرایشهای مهندسی معدن و متالورژی نیز تدریس گردد. امید است هر ساله به علت کمی بودجه امکان تجهیز آزمایشگاههای تحقیقاتی دانشگاهها از سالی به سال دیگر موکول نشوند. زیرا پیشبینی اعتبار کافی برای کارهای تحقیقاتی به خصوص در دانشگاهها لازم است، اما کافی نیست. عملا بودجههای پیشبینی شده مانند سایر پروژههای عمرانی در مقیاس ملی با جابجایی ردیفهای بودجه به طور کامل تخصیص داده نمیشود.
با توجه به شناختی که به منابع معدنی و انرژیزای اولیه ایران که برای تولید فولاد لازم است، دارید، آیا ایران برای گسترش تولید فولاد حتی بیش از نیاز داخلی خود دارای مزیت نسبی میباشد؟
ایران با ذخیره ذغال سنگ حدود 17/0درصد، ذخایر گاز و نفت به ترتیب 9/14 و 5/11درصد از کل ذخایر این سه ماده انرژیزا را در جهان به خود اختصاص داده است. حدود 3/1درصد از کل ذخایر شناخته شده سنگآهن دنیا در ایران وجود دارد. شناخت ما از منابع طبیعی خدادادی به علت عدم سرمایهگذاری کافی در امر زمین شناسی و اکتشاف محدود است و مسلما ذخایر بیشتری از مواد انرژی زای نفت و گاز و سنگآهن در کشور پهناور ایران وجود دارد و با سرمایهگذاری در امر اکتشاف و استفاده از انواع تجهیزات پیشرفته اکتشافی تا چند سال آینده ذخایر شناخته شده ایران در این ارتباط افزایش خواهد یافت. تولید فعلی فولاد ما اگر به نسبت ذخیره شناخته شده سنگآهن فعلی ما باشد، میبایست در سال 2007 حدود 17میلیون تن بوده است. یعنی درست حدود مصرف ظاهری فولاد در همین سال. اما با عنایت به اینکه ذخیره نفت و گاز ایران چندین برابر ذخایر شناخته شده سایر کشورها منجمله چین، 27 کشور بازار مشترک اروپا، ژاپن، کره جنوبی و... که تولیدکنندگان تولید فولاد در دنیا هستند، میباشد و تولید فولاد صنعت انرژیبری است، لذا ایران برای گسترش تولید فولاد نسبت به سایر کشورهای جهان دارای
مزیت خدادادی بالقوه است که باید برخلاف گذشته با درایت و مدیریت درست این مزیت بالقوه را به مزیت بالفعل تبدیل نماییم. زیرا ژاپن، آلمان و کره جنوبی 100درصد سنگآهن مورد نیاز خود را از خارج وارد میکنند. ژاپن حدود 95درصد انرژی مصرفی صنایع فولاد را از خارج وارد میکند.
۲۷کشور اروپایی نیز طی سالهای اخیر حدود ۸۸درصد سنگآهن و ۹۰درصد مواد انرژیزای لازم برای تولید فولاد را از خارج تامین کردهاند. چین نیز در سالهای اخیر حدود ۶۵درصد سنگآهن مصرفی خود را برای تولید فولاد از طریق واردات تامین کرده است. همچنین نزدیک به ۶۰درصد انرژی مصرفی در صنایع فولاد چین را از طریق واردات تامین میشود.
مقایسه این اعداد با آنچه که در مورد ایران گفته شد، موید مزیت نسبی ایران برای گسترش کیفی و کمی تولید فولاد میباشد.
همانطوری که گفته شد ایران برای گسترش کمی و کیفی تولید فولاد نسبت به سایر کشورها دارای مزیت نسبی بالقوهای میباشد که تا کنون این مزیت بالقوه به نظر اینجانب بنا به علل مختلف که مختصری شرح داده خواهد شد، تبدیل بالفعل نشده است.
بخش خصوصی سرمایهگذاری اندکی برای گسترش تولید محصولات نورد شده فولادی عمدتا در حد ظرفیت کارگاهی نموده است. اکثر اقداماتی که مدیران صنایع تولید فولاد عمدتا دولتی ایران در سالهای گذشته برای صادرات فولاد انجام دادهاند، بینتیجه بوده است. مثلا یک مرتبه با دستور مدیران کلان کشور مجبور به قطع صادرات یک نوع محصول که قرارداد فروش آن را منعقد نموده بودند، میشوند. این عمل لطمه زیادی به صادرات آینده فولاد کشور خواهد زد. مدیران صنایع از طرفی مجبور به اطاعت از مقامات مسوول دولتی هستند و از طرفی به علت عدم ایفای به عهد مجبور به پرداخت خسارت به طرف خارجی میباشند. همچنین در سالهای گذشته دولتها صنایع را مجبور به پایین نگه داشتن قیمت محصولات خود حتی به زیر قیمت تمام شده مینمودند. فکر میکردند با این کار جلوی تورم را خواهند گرفت. اما دیدیم تفاوت قیمت حوالههای محصولات فولادی با قیمت بازار آزاد آنها چقدر بود و عدههای سود جو از تفاوت قیمتها سودمیلیاردی کسب کردند. علاوه بر این صنایع تولید فولاد کشور نمیتوانستند با استفاده از منابع داخلی خود برای گسترش کیفی و کمی فولاد اقدام نمایند.
قیمتها امروزه جهانی شده است و نمیتوان دستوری قیمت کالایی را تعیین نمود. بلکه دولت باید مانند کشورهای پیشرفته دنیا زیر بنای لازم برای گسترش تولید فولاد (تامین مواد انرژیزا به میزان کافی و در ۳۶۵ روز از سال، سنگآهن با کیفیت مناسب، جاده برای حملونقل مواد اولیه و محصولات تولیدی و...) را فراهم نمایند تا بخش خصوصی با اطمینان کامل از آزادی تولید در چهارچوب قوانین کشور که هر روزه تغییر نکند، اقدام به سرمایهگذاری کند. متاسفانه تاکنون مسوولین کشور هیچ گونه تعهدی برای تامین انرژی و سنگآهن به سرمایهگذاران بخش خصوصی نداده است. به همین دلیل سرمایهگذاری بخش خصوصی برای تولید فولاد، عمدتا در محصولات نورد شده با ظرفیت کارگاهی حداکثر چند صدهزار تنی سرمایهگذاری میکنند، نه چندمیلیون تنی، متاسفانه باید بگویم تا زمانی که دولتمردان زیر بنای لازم را برای گسترش کیفی و کمی تولید فولاد به وجود نیاورند واردات فولاد به کشور ادامه خواهد داشت. زیرا بر مبنای برنامه چهارم توسعه که سه سال از آن گذشته است، دیدیم چه میزان از اهداف توسعه صنایع فولاد عملیاتی شد. در برنامه سوم توسعه نیز به اهدافی که در نظر داشتیم به دلایل گفته شده
نرسیدیم. امید است دولت مردان از گذشته عبرت گرفته و همت خود را برای فراهم کردن زیربنای مناسب برای توسعه صنایع تولید فولاد کشور به کار گیرند. در این صورت نیازی به ایجاد کارخانههای کوچک با تکنولوژیهای به روز نشده آن هم در آخر انشعابات خطوط انتقال گاز نخواهد بود.
رساندن گاز برای واحدهای احیاء مستقیم به ظرفیت 800 هزار تن در سال (طرحهای استانی فولاد)، روزانه به حدود یکمیلیون مترمکعب در 365 روز از سال با توجه به امکانات شبکه سراسری انتقال گاز عملا غیرممکن است. شاید هنوز دیر نشده باشد که احیاء سنگآهن را با استفاده از انرژی گاز در نزدیکی معادن سنگآهنی که به منابع تولید گاز نزدیک هستند، انجام داد. میتوان آهن اسفنجی تولیدی را به صورت بریکت گرم درآورده و بریکت گرم تولید شده را به کارخانههای متعددی که در نظر گرفته شده است، حمل نمایند. برای ایجاد اشتغال در محلهای فوق میتوان پس از تبدیل آهن اسفنجی به فولاد با ایجاد خطوط نورد نسبت به تولید محصولات نورد شده اقدام کرد.
ایجاد اشتغال به ازاء تولید یک تن آهن اسفنجی حدود یک چهارم ایجاد اشتغال به ازاء تولید یک تن محصولات نورد شده فولادی است. به عبارت دیگر با این تصمیمگیری اولا هزینه حمل مواد آهن دار به هشت کارخانه مورد نظر ۴۰درصد کمتر خواهد شد. ثانیا حمل گاز از مبادی تولید تا آخر انشعابات فرعی که بسیار هزینهبر خواهد بود و به سرمایهگذاری گزافی نیاز خواهد داشت، کمتر خواهد شد. ثالثا هزینه تولید آهن اسفنجی در یک یا دو محل به صورت انبوه خیلی کمتر از هزینه تولید در ۸ محل خواهد بود. رابعا سرمایه در گردش برای تامین موجودی انبار ۸ واحد احیاء مستقیم در ۸ محل خیلی بیشتر از تجمع این واحدها در یک یا دو محل میباشد. این افزایش سرمایه در گردش نقش بسزایی در قیمت تمام شده فولاد خواهد داشت.
برای گسترش کمی و کیفی تولید فولاد در ایران به نظر شما کدام یک از روشهای رایج تولید مناسب تر است؟
با توجه به ذخیره کم ذغال سنگ کک شو در ایران که در سوالهای قبل نیز گفته شد و اینکه تولید فولاد با استفاده از کوره بلند + کنورتور نیازمند کک متالورژی میباشد، لذا ایران برای گسترش تولید فولاد با استفاده از روش کوره بلند+ کنورتور در آینده مجبور به وارد کردن ذغال سنگ کک شو یا کک متالورژی خواهد بود. واردات ذغال سنگ کک شو وابستگی صنعت فولاد کشور را به خارج افزایش خواهد داد که این افزایش وابستگی به صلاح ملی ما نیست. اما در ارتباط با گاز ذخایر خدادادی ایران حدود ۱۵درصد کل ذخایر گاز طبیعی دنیا میباشد و دانش فنی تولید فولاد با استفاده از انرژی گاز در ایران هم سطح دانش فنی تولید فولاد بر مبنای استفاده از انرژی کک متالورژی است. لذا عقل سلیم حکم میکند با استفاده از انرژی گاز در گسترش تولید فولاد کوشا باشیم.
صنعت تولید فولاد بعد از صنعت آلومینیوم، انرژی برترین صنعت دنیاست. متاسفانه هنوز طرح جامع انرژی کشور و مدیریت چندهزارمیلیارد دلاری ثروت ملی در این 28 سال پس از انقلاب جدی گرفته نشده و بر مبنای اصول شناخته علمی دنیا تدوین نگردیدهاند. همچنین کشورهای پیشرفته صنعتی همزمان با انقلاب ایران که با افزایش قیمت نفت همراه بود، برای کاهش مصرف انرژی در کلیه زمینهها به خصوص صنایع انرژی بر با تدوین قوانین و ممیزی انرژی توانستند بدون لطمه زدن به کمیت تولید، مصرف انرژی را کاهش دهد. بدین وسیله برای تولید فولاد انرژی مصرفی به ازاء تن تولید را کاهش دادند. مثلا آلمانها از سال 1960 مصرف انرژی را در صنایع فولاد خود به ازاء تن تولید از 4/29 گیگاژول به 7/17 گیگاژول در سال 2006 رسانده اند. یعنی 8/39درصد انرژی مصرفی برای تولید فولاد در این کشور کاهش یافته است. با مصرف بهینه انرژی علاوه بر اینکه کمک به تامین انرژی نسل فعلی مینماییم، به نسلهای آینده هم برای بهرهمندی از منابع انرژیهای تجدیدناپذیر کمک شایانی خواهیم نمود. زیرا منابع نفت و گاز درآمد ارزی کشور را تامین میکنند.
با مصرف بهینه آنها سالهایی که مردم این کشور میتوانند از این نعمتهای خدادادی بهرهمند شوند، افزایش خواهد یافت. مصرف بهینه انرژی گازهای گلخانهای کمتری ایجاد مینمایند. گازهای گلخانهای مخرب محیط زیست هستند.
کشورهای بازار مشترک اروپا برای اجبار کارخانههای تولید فولاد سایر کشورها به مصرف بهینه انرژی به ازای تن تولید فولاد قصد دارند با تصویب تعرفه جدیدی از صادرات فولاد کشورهایی که بیش از حد معین به ازای تن تولید فولاد انرژی مصرف میکنند، جلوگیری نمایند. لذا کاهش شدت مصرف انرژی (انرژی مصرفی برای یک واحد تولید ناخالص ملی) را در تولید فولاد کشور حتما باید در طرح جامع تولید فولاد رعایت کنیم که متاسفانه چنین نکردهایم. شدت انرژی در ایران نسبت به ژاپن به طور کلی حدود 7 برابر است. ادامه این وضعیت یعنی اصراف در مصرف انرژی حتی برای تولید فولاد و ایجاد اشتغال اجحاف در حق آیندگان این مرز و بوم خواهد بود. کارایی انرژی برای مصرفکننده (واحدهای تولید فولاد) یعنی نسبت کار مفید مصرفکننده به انرژی نهفته مثلا در انرژی گاز مهمترین فاکتور طراحی چرخه تولید تا مصرف گاز و نفت کشور باید باشد.
اگر دو روش متداول تولید فولاد در ایران یعنی استفاده از کوره بلند+ کنورتور را با استفاده از سیستم احیای مستقیم (با استفاده از انرژی گاز) + کورههای قوس الکتریکی از لحاظ آلودگی محیطزیست مقایسه کنیم، خواهیم دید که در سال ۲۰۰۶ در سطح جهان در محیط زیست به ازاء تن تولید فولاد خام به طور میانگین با استفاده از کوره بلند+ کنورتور حدود ۱۴/۲تن گاز CO۲ و با استفاده از سیستم احیاء مستقیم + کورههای قوس الکتریکی حدود ۶۳/۰ تن گازCO۲ رها شده است. به عبارت دیگر استفاده از انرژی گاز برای گسترش کیفی و کمی تولید فولاد در ایران کمتر موجب آلودگی محیطزیست میشود.
متاسفانه هنوز قانونگذاران دولت را مجبور به ممیزی انرژی به خصوص در صنایع انرژی بر مانند تولید فولاد نکردهاند. ولی همین مقننین به دولت با مصوبههای خود رسما اجازه دادهاند برحسب نیاز یعنی در تابستان و زمستان انرژی صنایع را محدود و در مواردی قطع نماید تا دولتمردان بتوانند سوء مدیریت خود را در برنامه ریزی تامین انرژی بخش خانگی با کاهش یا قطع انرژی صنایع تا حدودی جبران نمایند.
همچنین تعرفه قیمتگذاری انواع انرژی مصرفی در ایران با مصوبه مجالس قانون گذاری بر خلاف سایر کشورهای جهان میباشد. یعنی تعرفه انرژی بخش خانگی که فقط مصرفکننده است کمتر از تعرفه بخش صنعتی که تولیدکننده است، اجرا میشود.
چگونه میتوان انتظار داشت مدیران صنایع عمدتا دولتی بتوانند به حیات صنعتی خود با قطع مکرر انرژی یا کاهش سطح آن ادامه دهند. قطع برق به مدت چند ساعت برای کارخانه تولید آلومینیوم المهدی مساوی چندینمیلیارد تومان خسارت میباشد. زیرا مذاب در سلولها تولید آلومینیوم منجمد شده و مجددا باید سلولها را به تدریج وارد مدار نمود. علاوه بر افزایش مصرف انرژی برای اینکه سلولها مجددا وارد مدار شوند، به تجهیزات گران بهای سلولهای تولید آلومینیوم نیز خسارت زیادی وارد میشود. یکی از علل عمده عدم گسترش صنایع تولید آلومینیوم در ایران حتی نسبت به بحرین مشکلات تامین انرژی بدون وقفه و محدودیت مجتمع آلومینیوم المهدی میباشد. البته خسارت وارده به علت قطع برق یا گاز به تجهیزات فرآیند تولید فولاد کشور برحسب نوع روش تولید فولاد متفاوت میباشد. آنچه مسلم است به علت اینکه حجم تولید فولاد ایران حدود 50برابر حجم فعلی تولید آلومینیوم کشور است، لذا خسارت وارده به علت قطع انرژی یا محدودیت مصرف انرژی به صنایع تولید فولاد چندین برابر صنعت آلومینیوم کشور میباشد.
اگر تمهیدات لازم برای نگهداری تجهیزات رفورمر (گازشکنهای میدرکس مجتمع فولاد مبارکه، خوزستان و...) قبل از قطع انرژی گاز انجام نگیرد، حرارت لولههای پر شده از کاتالیزاتور گازشکنها کاهش یافته و مسلما گرم کردن مکرر آنها سبب کاهش طول عمر تجهیزات گران قیمت که عمدتا وارداتی هستند، خواهد شد.
ارسال نظر