مسیر جهانی شدن فناوری« پرد »
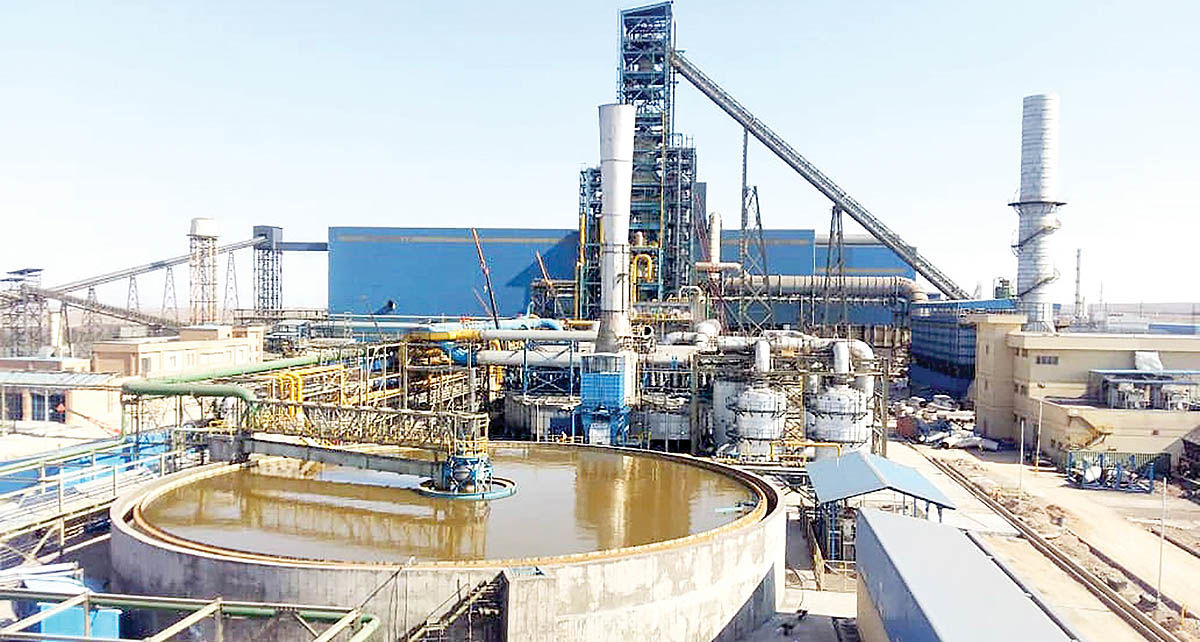
در شیوه پرد، گندله در کورههای حرارتی با استفاده از گاز طبیعی به آهناسفنجی تبدیل میشود.
چین که رتبه نخست تولید فولاد جهان را در اختیار دارد، بهطور عمده با روش کوره بلند این محصول پرمصرف را تولید میکند، اما اکنون با هدف گذر از چالشهای زیست محیطی و با استفاده از توان فنی و مهندسی ایرانی، رو به تولید فولاد به روش فوق آورده است.
در همین حال یک شرکت ایرانی با بهرهگیری از روش «احیای مستقیم ایرانی»، نخستین کارخانه تولید آهناسفنجی در بزرگترین تولیدکننده فولاد جهان را طراحی، اجرا و راهاندازی کرد.
پیش از این پلنت (کارخانه) احیا مستقیم گازی در آن کشور ساخته نشده بود و به سبب مسائل زیستمحیطی، جهتگیری «اژدهای زرد» به سمت ساخت کارخانههای تولید آهناسفنجی به روش گازی است.
قرارداد ساخت نخستین کارخانه احیای مستقیم به روش گازی بین شرکت CSTM از چین و شرکتی ایرانی به عنوان صاحب تکنولوژی «پرد» منعقد شد.
پروژه احیای مستقیم CSTM با ظرفیت ۳۰۰هزار تن در سال و محصول HBI در شهر تای یوآن (Taiyuan) احداث و در ۳۱ خرداد سال ۱۴۰۰ راهاندازی شد.
ناحیه کوره در این کارخانه احیا مستقیم با روش ایرانی احیای مستقیم PEREDتوسط شرکت MME طراحی شده است و بخشی از تجهیزات اصلی آن نیز در ایران ساخته و به چین صادر شد.
اکنون بهدلیل عدمدسترسی به گاز طبیعی، این کارخانه از گاز حاصل از آون ککسازی استفاده میکند.
وجود ذخایر بزرگ گازی در کشور، توسعه فرآیندهایی با محوریت استفاده از این نعمت الهی را در چشمانداز ۲۰ ساله کشور به شدت مورد توجه قرار داده است. بهطوری که با توجه به نقش مولد صنعت فولاد، برنامهای هدفمند برای گسترش و رونق آن در چشمانداز توسعه اقتصادی ایران اسلامی تدوین شده است.
یکی از مهمترین دستاوردهای کسب شده در این زمینه، بهینهسازی فرآیند تولید فولاد به روش PERSIAN REDUCTION است که با نام تجاری پرد (PERED) معرفی شده است.
فناوری پرد بومیسازی شده با تکیه بر اصول علمی و تجربیات متخصصان ایرانی است. یکی از مهمترین مزیتهای فناوری پرد، کاتالیستهای منحصر بهفرد آن است که با ویژگی طول عمر بیشتر و تسریع در شکست گازهای احیایی در قلب ریفرمرهای فولادی PERED میتپد.
فناوری PERED با ظرفیت صادرات دانش فنی آن آینده صنعت فولاد را تضمین میکند.
با توجه به بومیسازی صنعت کاتالیست در ایران از سوی شرکت دانشبنیان نفت و گاز سرو، تولید و بومیسازی کاتالیست فناوری PERED با مشارکت دو مجموعه کشور یعنی شرکت مهندسی معادن و فلزات -MME- و نفت و گاز سرو و با همکاری شرکت مهندسی مشاور برسو در مجتمع احیا استیل فولاد بافت به ثمر نشست.
تولید و بارگذاری کاتالیستهای پرد در مجتمع احیا استیل فولاد بافت، به عنوان نخستین واحد احیای مستقیم آهن که با کاتالیستهای ایرانی فعالیت خواهد کرد، گامی بلند در خودکفایی کامل در فولادسازی کشور بود.
نخستین کارخانه تولید آهن اسفنجی جهان بر اساس روش ابداعی مهندسان ایرانی فولاد به نام «پرد» PERED در فولاد شادگان در استان خوزستان واقع شده و مراحل تولید و به ظرفیت رسیدن را با موفقیت طی کرده است.
فناوری احیای مستقیم پرد توسط شرکت MME در آلمان ثبت شد و برای نخستین بار در جهان در ایران و فولاد شادگان به بهرهبرداری رسید.
در ایران به طور معمول از روش و فناوری میدرکس استفاده میشود که باید حق امتیاز و استفاده از این تکنولوژی به صاحب آن پرداخت شود، اما مالک تکنولوژی پرد ایران است و پرداخت حق بهرهبرداری حذف میشود و این مزیت بزرگی برای این روش به حساب میآید.
در این زمینه، «امیرهومن کریمی وثیق» مدیرعامل شرکت دانشبنیان نفت و گاز سرو، که بنیانگذار کاتالیست مورد استفاده در فناوری پرد است، گفت: اکنون از هشت طرح فولادی جدید کشور، ۴ طرح فولاد شادگان(خوزستان)، میانه (آذربایجان شرقی)، بافت (کرمان) و نیریز (فارس) به فناوری پرد تجهیز شدهاند.
وی خاطر نشان کرد: بررسیها از فولاد بافت که حدود دو سال است از این فناوری استفاده میکند، بازخوردهای خوبی را نشان داده و حتی در نظر دارد در مدول دوم کارخانه خود نیز از آن استفاده کند.
مدیرعامل شرکت نفت و گاز سرو در خصوص مزیت کاتالیستهای این تکنولوژی یادآور شد: باتوجه به در اختیار داشتن تکنولوژی برتری که نزد این شرکت دانش بنیان است، توانایی تولید کاتالیستهای خاص فناوری پرد را بهدست آوردیم به طوری که طبق گزارشهای واصله از عملیات اورهال اخیر مجتمع فولاد بافت، این کاتالیست طی دو سال فعالیت خود بدون افت فعالیت بوده و تغییری در کیفیت آن پدیدار نشده و متخصصان این مجتمع توانستند به ظرفیت بالاتر از استاندارد تولید خود در سالهای اول و دوم خود برسند.
کریمی وثیق تصریح کرد: نفت و گاز سرو با تکیه بر دانش متخصصان خود امکان سفارشیسازی کاتالیستهای موردنیاز صنایع مختلف نفت، گاز، پتروشیمی، پالایش و فولاد را در اختیار دارد.
رفع نواقص فناوری پرد توسط متخصصان داخلی
همچنین مدیرعامل فولاد بافت نیز در این زمینه اظهار کرد: فناوری پرد از ابتدا ایده بسیار خوبی بود و کارآیی خوبی نیز داشت، اما مشکلات و نقایصی به همراه داشت که باید برطرف میشد و این مهم به دست متخصصان توانمند مجتمع احیا استیل فولاد بافت با پشت سرگذاشتن موانع و مشکلات، رکوردهای متوالی در تولید آهناسفنجی در این مجتمع به تحقق رسید.
عطارد گودرزی یادآور شد: احیا استیل فولاد بافت درست در اوج تحریمها یعنی سال ۱۳۹۷ که کارخانه در حال تکمیل بود، شکل گرفت. بحث تحریمها بهشدت مطرح شده بود و آن امر باعث شد که همه فعالیت فولاد بافت بر دانش بومی متمرکز شود. تا آن زمان یکسری تجهیزات از خارج کشور وارد شده بود ولی مابقی جزئیات ساخت کارخانه با مهندسی ایرانی کامل شد.
وی اضافه کرد: حتی تجهیزاتی که از خارج آمده بود و قرار بود سوپروایزرهای خارجی آنها را در کارخانه راهاندازی کنند، بهدلیل تحریمها حضور نیافتند و با استفاده از کارشناسان و متخصصان داخلی فولاد بافت، کارخانه راهاندازی شد.
وی تاکید کرد: تکنولوژی پرد میتواند رقیب بسیار خوبی برای فناوری میدرکس باشد، اهمیت این مساله وقتی بیشتر میشود که میدرکس نیز به تبعیت از تحریمهای آمریکایی، صنعت فولاد ایران را تحریم کرد.
گودرزی درباره کاتالیستهای تکنولوژی پرد با بیان اینکه انتخاب کاتالیست از شرکت نفت و گاز سرو بر اساس کارنامه رضایتبخش این شرکت در حوزه تولید کاتالیست میدرکس بود، گفت: قبل از اینکه برنامه کاری در احیا استیل به سمت مصرف کاتالیست شرکتهای خارجی سوق یابد، سعی کردیم از شرکتهای ایرانی تولیدکننده کاتالیست بهره گیریم و نیاز خود را تامین کنیم، به همین دلیل سراغ شرکت نفت و گاز سرو رفتیم.
گودرزی با اشاره به این مطلب که طبیعی بود که ما هم از یک برند ایرانی که هم امتحانش را پس داده و هم رضایتمندی بالایی از محصولاتش وجود داشت، استفاده کنیم، خاطرنشان کرد: با توجه به اینکه سال سوم تولید را پشتسر گذاشته، خوشبختانه نتیجه خیلی خوبی از استفاده این کاتالیستها دریافت کردهایم و به طور قطع در فاز بعدی نیز از برندهای ایرانی استفاده خواهیم کرد.
مدیرعامل فولاد بافت در خصوص فعالیتهای این مجتمع افزود: هدف اصلی شرکت احیا استیل فولاد بافت از ابتدا توسعه بوده است. برهمین اساس دو پروژه واحد احیا مستقیم ۸۰۰هزار تنی مشابه همین واحد فعلی و یک واحد گندله ۵/ ۲میلیون تنی را تعریف کرده است.
وی ادامه داد: پروژه نخست احیا مستقیم است کار خود را شروع کرده و تا به امروز ۱۷درصد پیشرفت فیزیکی داشته است. با تمام توان در تلاش هستیم تا پایان سال ۱۴۰۱ آن را وارد مدار تولید کنیم.
گودرزی افزود: در پروژه گندلهسازی نیز کارهای مقدماتی آن انجام شده و فکر میکنم ظرف یک تا دو ماه آینده، عملیات اجرایی آن نیز آغاز شود؛ بنابراین تا پایان سال ۱۴۰۴، ما میتوانیم ۵/ ۲میلیون تن گندله و ۶/ ۱میلیون تن آهناسفنجی تولید کنیم.