همزمان با هفته دولت
عملیات اجرایی طرح «فولاد غدیر ایرانیان» آغاز شد
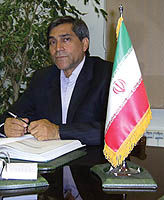
فولاد آلیاژی ایران و فولادهای مخصوص محور توسعه کیفی صنعت فولاد است.
در شرایطی که کشورهای آسیایی از جمله ترکیه، هند و چین همزمان با ایران به فکر ایجاد چنین واحدهایی افتادند، بسیار حرکت پرشتابی داشتهاند.
به عنوان مثال چین در سال ۱۹۹۱ حدود ۹۳میلیون تن فولاد تولید میکرد امروز به مرز ۳۸۰میلیون تن در سال رسیده است.
ترکیه و کره جنوبی نیز با ما شروع کردند. تولید فولاد ساختمانی در کشورمان از سال 46 در گروه ملی صنعت فولاد ایران شکل گرفت. آن زمان بخش خصوصی مجموع کارخانههای نورد را سرمایهگذاری کرد.
در سال ۵۰ هم برای نخستینبار کورههای ذوب با سیستم قوس الکتریکی از شرکت کروپ (آلمان) به کشورمان وارد شد.
5ماه بعد روسها سیستم فولادسازی با روش سنتی کوره بلند، را وارد ایران کردند.
عمر فولاد امروز در ایران به ۴۰سال میرسد. البته این رقم با احتساب صنایع نورد است. اما عمر ذوب فولاد ۳۵سال است.
در سال 53 ایران به این فکر افتاد تولید فولادهای مخصوص و آلیاژی را در دستور کار قرار دهد.
علت این است که صنایع نفت و گاز، حفاری، پتروشیمی، خودرو، ماشینسازی، لوازم خانگی و... نیاز به فولادهای مهندسی دارند.
از همینرو در سال 53 شرکت فرانسوی «کروز لوآ» قراردادی با ایران منعقد کرد تا یک مجتمع فولادی روبهروی مجتمع فولاد اهواز ایجاد کند.
در این میان گروهی برای گذراندن دورههای کارشناسی به آن کشور اعزام شدند.
اما پس از آنکه ایران 25درصد سهم کروپ را خرید، فرانسویها در عمل از صحنه خارج شدند و به نوعی عقبنشینی کردند. با تصور اینکه ایران تولید فولادهای مخصوص و آلیاژی را با آلمان پیگیری میکند. هر چند تا پیروزی انقلاب این مساله مسکوت ماند. پس از انقلاب نیز در سال 59 مجددا این طرح به عنوان یکی از پروژههای 10 گانه انقلاب مورد توجه و دستور کار قرار گرفت. اما با شروع جنگ تحمیلی، این طرح مجالی برای اجرا نیافت. اما ستادی در وزارت صنایع و معادن مسوول پیگیری این طرح شد.
این در حالی بود که اروپاییها و حتی ژاپنیها هم حاضر نشدند اسناد مناقصه را بگیرند، به همین دلیل تا سال ۶۷ این مساله مسکوت ماند. در آن سال کنسرسیوم بوهلر اتریش فوستاپین آلمان قرارداد را بر عهده گرفتند. (بوهلر یکی از ۵ شرکت صاحب دانش فنی ساخت فولاد مخصوص است.) پس از آن میتسوبیشی و دانیلی (ایتالیا) با ۴۷۳میلیون دلار تمام مراحل تا راهاندازی را در دست گرفتند. در این پروژه ۵ کارخانه زیر در دستور کار قرار گرفت.
1 - کارخانه فولاد آلیاژی
۲ - کارخانه نورد سنگین
3 - کارخانه نورد سبک
۴ - کارخانه عملیاتی حرارتی و تکمیل کاری
5 - کارخانه تولید گازهای صنعتی همچون اکسیژن، آرگن و ازت
علاوه بر آن یک پست انتقال برق، ۲۷کیلومتر راهآهن اختصاصی و جاده اختصاصی تا ۲۷کیلومتری شهریزد پیشبینی شده بود. بدین ترتیب این مجتمع در ردیف ۱۰ کارخانه معتبر تولید فولاد آلیاژی جهان قرار گرفت.
مجموعه فوق در سال 78 کاملا به بهرهبرداری رسید. سرمایه آن با مشارکت سرمایهگذاری غدیر (37درصد)، صندوق بازنشستگی و حمایت از کارکنان فولاد (22درصد) و ایمیدرو (41درصد) صورت گرفت. این مجموعه در واقع محور کیفی تولید فولاد در ایران شد. البته فولاد آلیاژی در مقیاس کوچک در اصفهان و اسفراین وجود دارد، اما در این حجم، یک مجموعه کاملی نیست.
نیاز کشور به این نوع فولادها چه میزان است؟
ابتدا بگویم که حدود 14درصد کل تولید فولاد دنیا مربوط به فولادهای آلیاژی و مخصوص است.
سال گذشته میلادی از ۱۰۵۰میلیون تن فولاد خام حدود ۱۳۰تا ۱۵۰میلیون تن انواع فولاد آلیاژی، مخصوص و مهندسی تولید شد. در حال حاضر کشورهای توسعه یافته اروپا ۱۶درصد، آمریکا ۱۲درصد و سوئد ۵۰درصد از این رقم را مصرف میکنند. کشور ما اکنون تنها ۲درصد از کل فولاد آلیاژی دنیا را مصرف میکند.
برآوردها نشان داده در کشورمان کل صنایع (لوازم خانگی،...) در جمع 400هزار تن از این نوع فولاد را مصرف میکنند. البته این موضوع را یادآوری کنم که تنوع فولاد آلیاژی خیلی زیاد است. حال اگر در این شرایط میخواهیم در ردیف کشورهایی همچون کرهجنوبی قرار گیریم، باید مصرف فولاد آلیاژی ما به 800هزار تن برسد.
از سوی دیگر زمانی که ظرفیت تولید فولاد ما به ۲۹تا ۳۰میلیون تن رسید باید ۲ تا ۳میلیون تن آن به تولید فولاد آلیاژی اختصاص یابد.
تولید فولاد آلیاژی در ایران از چه سالی آغاز شد؟
سال ۷۸ به بررسی و تست گرم کارخانه سپری شد. هر چند در آن سال تولید فولاد آلیاژی به ۲۶هزار تن رسید.
این با تعهداتی که برای سال اول پیشبینی شده بود تطابق داشت.
در سال ۷۹ حدود ۳۹هزار تن، سال ۸۰ به ۴۲هزار تن، سال ۸۱ حدود ۴/۹۱هزار تن، سال ۸۲ به رقم ۵/۱۳۳هزار تن و سال ۸۳ به ۳/۱۶۵هزار تن و در سال ۸۴ (سال پنجم) تولید به ظرفیت اسمی یعنی ۲۰۱هزار تن رسید.
در سال گذشته انواع و اقسام فولادهای گرم کار، سرد کار، خوش تراش، میکروآلیاژها، مهندسی، کیفی، مخصوص، عملیات حرارتیپذیر و ... تولید شد.
اگر صنایع مختلف برای بهرهمندی از این محصول را تقسیم کنیم، ۶۱درصد نیاز صنایع خودروسازی را این واحد تامین میکند.
15درصد هم صنایع ماشینسازی، 21درصد برای ابزارسازی، صنایع نظامی هم حدود 2درصد و مابقی هم برای دیگر صنایع به کار گرفته میشود.
تولیدات فولاد آلیاژی به چه کشورهایی صادر میشود؟
سال گذشته افزون بر 5/17هزار تن به کشورهای اروپایی صادر شد که 82درصد آن به آلمان اختصاص یافت.
یک درصد به استرالیا، ۵/۹درصد به ایتالیا و ۵/۷درصد نیز به فرانسه صادر شد.
چرا این حجم از صادرات تنها به آلمان اختصاص دارد؟
به دلیل این که شرکتهای مرسدس بنز، بیامو و فولکس واگن مشتریان این محصول هستند.
در مجموع 16 تولیدکننده درجه اول خودرو در دنیا همچون بنز، بی.ام.و، ولوو، اسکانیا و فیات از مشترهای تولیدات فولاد آلیاژی ایران هستند.
اینها به لحاظ قوانین ایمنی، استانداردها با شرکتی در تبادل باشند که به آن اطمینان وجود داشته باشد.
حال برای شرکتی که 5 سال از بهرهبرداری آن میگذرد، چنین امری مایه افتخار است.
در سالهای گذشته انتقاداتی راجع به حجم سرمایهگذاریهای این کارخانه و زمان بازگشت سرمایه و ... مطرح میشد. شما چه میزان به آن انتقادات اعتقاد دارید؟
ببینید، وقتی به 30 سال پیش برمیگردیم میبینیم که احداث کارخانه فولاد آلیاژی برای این مملکت آرزوی دیرینه به حساب میآمد.
یعنی آرزوی جامعه متالورژی و مهندسان برتر این کشور این بود که فراتر از فولاد ساختمانی محصول دیگری تولید کنند.
بعد به دلایلی تحقق آن آرزو 30 سال به تعویق میافتد. اما حالا که به چنین دستاوردی رسیدیم به راحتی گذشته را به انتقاد میکشیم.
این خوب است. اما این تجزیه و تحلیل گذشته میتواند چراغ راهنمای آیندهمان شود.
آن زمان که در شرایط جنگ به سر میبردیم، کسی حاضر به تهیه اسناد مناقصه نمیشد. میخواستیم دانش فنی بخریم. کسی آن را به ما نمیداد. در حالی که امروز با اقداماتی که با دانشگاه شیراز انجام دادیم دانش فنی میکروآلیاژی را بومی کردیم و بالغ بر 4 - 5هزار تن نیاز داخل را تامین کردیم.
اکنون شرایط متفاوت از وضعیت قبلی است. ما میتوانیم از فناوری تولید فولاد زنگ نزن (stainless steel) حرف بزنیم. به اعتقاد من کسانی که در دولتهای قبلی چنین تصمیمی گرفتند، اقدام بسیار شجاعانهای انجام دادند.
چرا که به جای وارد کردن آدامس و چیپس و پفک، دست به چنین کاری زدند. اما شرایط به گونهای بود که برای خرید دانش فنی مثلا 40میلیون دلار پرداخت کنند. از طرف دیگر هم زیرساختها نظیر احداث پست برق، جاده، خط انتقال آب و... را روی دوش خود میدیدند. حالا این پروژه را با کارخانهای در مصر مقایسه میکنند. این در حالی است که تشابهی با این کارخانه ندارد. چرا که تجهیزات آن کمتر از این طرح بوده است. علاوه بر آن نیازی به احداث زیرساختهایی که ما ایجاد کردیم، نداشته است.
اگر واقع بین باشیم میتوانیم بگوییم بله، امروز با تجربهای که داریم میتوانیم با سرمایهگذاری کمتری کارخانهای مشابه مجتمع فولاد آلیاژی بسازیم.
نرخ بازگشت سرمایه در فولاد آلیاژی چه مدتی پیشبینی شده بود؟ اکنون در عالم واقع هستیم چه مقدار از سرمایهگذاری اولیه بازگشته است؟
سوال بسیار خوبی است. قسمتی از آن سرمایهگذاری که در آن مدت انجام گرفت با دلار ۷تومانی بود و بخشی هم با دلار ۱۷۵تومان.
هر چند حساب ذخیره ارزی با تصمیم دولت قسمتی از بدهی ارزی این کارخانه را بخشیده است. در آن مقطع گزارش فنی و اقتصادی مشخص کرده بود که دانش فنی با ارز 175تومانی و تجهیزات با دلار 7تومانی تامین شود. هرچند در ابتدا طرح توجیهی به صورت دلار 7تومانی تعریف شده بود. شما بدانید همه سرمایهگذاریهای فولادی با نرخ رسمی (7تومانی) انجام گرفته است. واقعا دور از انصاف بود که در یک صنعتی که دانش فنی نیاز دارد، از ارز شناور (175تومانی) استفاده شود.
خوب آن زمان پیشبینی نمیشد نرخ ارز چنین شتابان پیش برود. بنابراین طبیعی بود که بازگشت سرمایه به درازا بکشد. این کارخانه وقتی به بهرهبرداری رسید که نرخ دلار تقریبا به مرز ۸۰۰تومان رسیده بود.
اما به دلیل بازپرداخت سود و تسهیلاتی که در مدت نصب و راهاندازی دریافت شده بود کارخانه در شرایط زیاندهی قرار گرفته بود. چرا که تولید پایین و زیر ظرفیت اسمی بود. از سوی دیگر فولادهای مخصوص صنایع ماشینسازِی، خودرو و... از کشورهای چین، روسیه، اوکراین و... وارد کشور میشد اما با رسیدن به ظرفیت اسمی، کارخانه به سوددهی رسید. طوری که اکنون با حدود 12 تا 15درصد نرخ سرمایهگذاری (آن هم با تجدید ارزیابی) میتواند سودده باشد. الان هم مقدمات لازم برای ورود به بورس، ارزیابی و مطالعات کمیته ارزیابی نهایی شده است. انشاءا... به زودی شرکتی بورس میشویم.
شما اشاره کردید کارخانه میتواند با این نرخ سودده باشد؟ الان در چه وضعیتی قرار دارد؟
در سال گذشته حدود 12درصد سود پس از کسر مالیات داشتیم.
از طرح فولاد غدیر ایرانیان که در هفته دولت شاهد عملیات اجرایی شد بفرمایید. درست است که یزد تاکنون فولاد آلیاژی داشته اما بهرغم معادن بزرگ از مجتمع فولادسازی (فولاد خام) بهرهمند نشده است. ظاهرا توافقنامهای در این باره امضا کردهاید.
پیش از هر چیز بگویم که الان به وضعیتی رسیدیم که مواد اولیه صنایع خودروسازی، ماشینسازی، نفت و گاز و.... در داخل تولید میشود. اما استان یزد به لحاظ داشتن پتانسیل معدنی و صنایع معدنی، میتواند قطب چهارم فولاد در کشور شود. چرا که ذخایر غنی در سنگآهن مرکزی ایران و چادرملو در اختیار دارد و علاوهبر آن سرمایههای عظیمی در بخش معدن جذب کرده است.
در حال حاضر نیز در اردکان در شرف راهاندازی طرح ۴/۳میلیون تنی گندلهسازی هستیم. این طرح اکنون مراحل نهایی نصب را طی میکند. انشاءا... تا انتها یا ابتدای سال بعد به تولید میرسد. این مجموعه با توجه به نیاز بار فلزی که در استان وجود دارد، قرار بود ۲واحد یزد ۱ و ۲ هر کدام ۸۰۰هزار تن فولاد خام تولید کنند. اما در ماه اخیر تصمیم بر آن شد که با سرمایهگذاری غدیر، امید، چادرملو، ایمیدرو، آهن و فولاد غدیر ایرانیان، آهن و فولاد ارفع، گندلهسازی اردکان و سرمایهگذاری معادن و فلزات به مجتمع عظیم فولاد و به هم پیوسته از گندلهسازی، ۳واحد آهن اسفنجی ۸۰۰هزار تنی با روش میدرکس (Midrex) و با سرمایهگذاری غدیر ایرانیان و ارفع احداث شود.
علاوه بر آن 3واحد فولادسازی (شامل 2واحد بیلت و یک اسلب 800هزار تنی) در آن مجموعه احداث شود. در انتهای خط هم با مشارکت همین شرکتها یک نورد ورق نازک احداث خواهد شد. در حقیقت بار فلزی منطقه کاملا تامین میشود.
البته میدانید در منطقه اردکان خط لوله گاز، برق و.... وجود دارد.
این صنعت فولاد که ما دنبال آن هستیم، در مقایسه با روشهای سنتی به مراتب به آب کمتری نیاز دارد. احیای مستقیم تنها 20درصد روش کوره بلند آب نیاز دارد. ضمن آنکه در فناوری جدیدی که در این طرحها داریم استفاده مجدد از آب را داریم. بنابراین با تبخیر بسیار کمی مواجه خواهیم شد. آنجا با مخازن بتنی، آب را برگشت میدهیم. سیستمهای خنککننده همه از نوع مداربسته و فوقالعاده مدرن هستند. قرارداد این بخش را فولاد غدیر ایرانیان با کنسرسیوم ایرانکو، ایرتیک و ایتالیا منعقد کرده است. کلنگ احداث این مجموعه هم در هفته دولت زده شده است.
پیشبینی کردهاید بحث گشایش اعتبار طولانی نشود؟
معمولا مراحل استفاده از تسهیلات بانکی زمانبر است. شما بدانید از مرحلهای که وارد بانک عامل میشوید تا هیات امنا، بانکمرکزی، برگشت به بانک، مشارکت مدنی، 2، 3سال زمان صرف میشود. البته جای تاسف دارد. چرا برای طرحهایی که از سوددهی، از اشتغالزایی و عدالتگستری آنها اطمینان داریم این همه وقت صرف میشود. این صنعت بومی شده است. به خصوص در بخش مکانیکال، با این حال زمان بسیار طاقتفرسایی صرف میشود. بحمدا... این پروسه برای فولاد غدیر ایرانیان سپری شده است. البته برای فعالشدن LC نیازمند حمایت ایمیدرو و سرمایهگذاری غدیر هستیم.
زمان اجرای طرح چه میزان پیشبینی شده است؟
هر چند از پیمانکار اییپیسی تعهد گرفتهایم طرح را 30 ماه انجام دهد اما به طور یقین تا زمان بهرهبرداری به 36 ماه میرسد.
گویا کل این طرحها ۶۰۰میلیارد تومان سرمایه جذب منطقه میکند. چه بخشی از این رقم از حساب ذخیره ارزی تامین میشود؟
در کل پیشبینی کردیم حدود 240میلیون یورو از حساب ذخیره و 360میلیارد تومان نیز سهم آورده نقدی سهامداران باشد. در مجموع حجم سرمایهگذاری به 600میلیارد تومان میرسد.
مناسبات تامین سرمایه اکنون فراهم شده است. در واقع سود سهامی که چادرملو باید بابت سهام حساب و سرمایهگذاری معادن و فلزات بپردازد، در همان منطقه خواهد ماند. این هم از محاسن اجرای طرح است.
ارسال نظر