رقابتپذیری در بازارهای جهانی
آیا سودآوری فولادسازان به معنای افزایش بهرهوری است؟
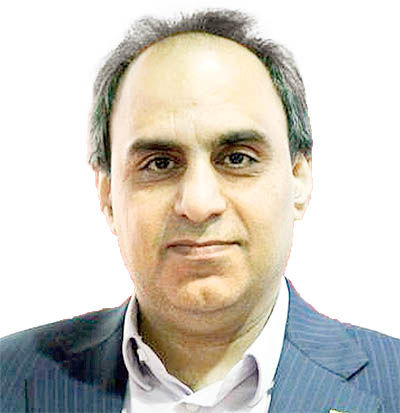
اظهارنظر نسبت به میزان بهرهوری فعلی صنعت فولاد کشور در شرایط کنونی نیاز به بررسی دقیق این موضوع از زوایای مختلف دارد. اگر بهرهور بودن فولادسازان معادل سودده بودن آنها تعریف شود، میتوان گفت که در حال حاضر فولادسازی ایران صنعتی بهرهور بهشمار میرود که میتواند سود ذینفعان خود را محقق کند. اما واقعیت آن است که معادلسازی بهرهوری با سوددهی چندان درست نیست و برای آنکه مشخص شود یک صنعت، بهرهور است یا خیر باید علاوه بر سوددهی مولفههای متعدد دیگری مدنظر قرار گرفته و بررسی شود.
بهروزرسانی تکنولوژی، حلقه مغفول واقعشده افزایش بهرهوری
پارامترهای متعددی در تعیین بهرهوری یک مجموعه اثرگذار است که یکی از آنها دانش و تکنولوژی بهکاررفته در صنعت مورد بررسی است. طیف وسیعی از تکنولوژی در صنعت فولاد کشور به کار رفته است. به عنوان مثال شرکت ذوب آهن اصفهان بهعنوان قدیمیترین فولادساز کشور از تکنولوژی کوره بلند برخوردار بوده و شرکت فولاد خوزستان اولین تولیدکننده فولاد به روش احیای مستقیم و کوره قوس است و شرکتهای متعدد فولادسازی ظرف سالهای گذشته در کشور با طیف وسیعی از تکنولوژی و فناوری شکل گرفتهاند که میزان بهرهوری صنعت فولاد وابسته به نوع تکنولوژی هر یک از این شرکتها و البته میزان بهروزرسانی آنها در طول سالهای فعالیت است.
در حالی که بخشی از صنایع فولادی مطابق استانداردهای روز دنیا احداث شده و ظرف سالهای فعالیت نیز تجهیزات و تکنولوژی آنها بهروز شده اما بخش قابل توجهی از تولید فولاد کشور توسط واحدهای کوچک القایی انجام میشود که تجهیزات آنها دستدوم خریداری شده و حتی این تجهیزات دستدوم نیز مربوط به شرکتهای صاحب نام در تکنولوژی فولادسازی دنیا نیست. اگرچه در شرایط کنونی بازار کشور این واحدها سودده هستند اما اگر قرار باشد که این فولادسازان در شرایطی برابر به رقابت با تولیدکنندگان جهانی بپردازند، تابآوری لازم را نداشته و این یعنی این مجموعهها بهرهور نیستند.
همچنین در سالهای اخیر طرحهای فولادی در کشور تصویب و اجرایی شده و همچنان در مرحله اجرا قرار دارد که طراحی آنها مربوط به بیش از دو دهه قبل است. نمونه بارز این مجموعهها طرحهای هفتگانه فولادی با ظرفیت تولید سالانه ۸۰۰ هزار تن محصول در سال است که در نقاط مختلف کشور اجرایی شده و در برخی موارد همچنان در حال اجرا بوده و بر همگان نیز مبرهن است که این شرکتها در شرایط مساوی هیچ شانسی برای رقابت در بازارهای جهانی ندارند و عملاً در صورت ایجاد فضای آزاد و رقابتی تابآوری لازم را نخواهند داشت. به این ترتیب باید گفت اگرچه اقدامات قابل توجهی در صنعت فولاد کشور انجام شده اما بهرهور شدن این صنعت به مفهوم واقعی، نیاز به نگاهی عمیقتر و حرکت به سمت تکنولوژیهای بهروز و قابل رقابت با تولیدکنندگان خارجی دارد.
رشد بهرهوری با تکیهبر نیروی انسانی بهرهور
منابع انسانی موضوع مهم دیگری است که در افزایش بهرهوری یک مجموعه تاثیری بسزا دارد. اگر مجموعهای با بهروزترین تکنولوژیهای روز دنیا ساخته شود، بهرهبرداری از آن با نیروی انسانی با دانش قدیمی امکانپذیر نیست. درواقع یک مجموعه فناور نیاز به نیروی انسانی با دانش بهروز دارد. بنابراین برای داشتن مجموعهای بهرهور، علاوه بر بهروزسانی تجهیزات و تکنولوژی، باید در بخش آموزش و رشد مهارت نیروی انسانی نیز سرمایهگذاری انجام شود تا در نهایت بتوان به یک مجموعه تماماً فناور تبدیل شد که جایگاهی در سطح جهانی داشته باشد.
موارد دیگری نیز در افزایش بهرهوری یک صنعت اثرگذارند که عبارتاند از: کیفیت و کمیت مواد اولیه، بهرهور بودن انرژی، وجود زیرساختهای مورد نیاز همانند زیرساخت حملونقل ریلی، جادهای، دریایی و... که تمامی این موارد در بهرهوری یک شرکت اثرگذار هستند. البته بخشی از این موارد تحت اختیار و درواقع مدیریت مجموعه و بخشی نیز خارج از اختیارات یک مجموعه است.
اگر مجموعهای در زمان تعریف به درستی طراحی نشود، طبیعتاً نمیتواند در زمان بهرهبرداری به بهرهوری مناسب نیز برسد؛ با وجود این بهرهبرداران میتوانند حداکثر تلاش خود را انجام دهند که چنین مجموعههایی را نیز به حداکثر بهرهوری برسانند. به عنوان مثال بهروزرسانی تکنولوژی مطابق شرایط روز در اختیار بهرهبردار است اما لزوماً داشتن نیروی انسانی کارآزموده تنها در اختیار تصمیمگیران یک مجموعه نیست؛ چراکه نیروی انسانی یک بنگاه اقتصادی از بدنه جامعه انتخاب میشود و داشتن نیروی انسانی کارآمد نیاز به تربیت نیروی انسانی مناسب در بطن جامعه دارد. درواقع صنعت فولاد بخشی از جامعه بوده که از سویی دانش و دستاوردهای این صنعت با جامعه و از طرف دیگر دانش جامعه با این صنعت به اشتراک گذاشته میشود و البته توسعه این صنعت میتواند به ارتقای دانش صنعتی جامعه کمک کند. مولفههای بیانشده در تشخیص بهرهور بودن یک مجموعه فولادی در قیاس با مجموعههای مشابه خارجی بود که مطابق استانداردهای روز دنیا فعالیت میکنند.
فولاد خوزستان در مسیر صحیح حرکت
فولاد خوزستان در زمان آغاز پروژه، طراحی مطابق با شرایط و استانداردهای روز دنیا داشت و در زمان آغاز به کار فولادسازی شرکتی در مقیاس سایر فولادسازان دنیا بهشمار میرفت. طراحی ابتدایی در نظر گرفتهشده برای این واحد، ظرفیت تولید سالانه ۵/ ۱ میلیون تن شمش فولاد بود؛ در ادامه و در سالهای بعد با طرحهای توسعهای که در مجموعه انجام شد ظرفیت اسمی تولید شمش در این شرکت به حدود چهار میلیون تن در سال رسید و ظرف سالهای اخیر فولاد خوزستان سالانه بیش از ۸/ ۳ میلیون تن فولاد تولید میکند. درواقع ظرف ۳۰ سال سپریشده از آغاز به کار فولاد خوزستان، ظرفیت تولید شمش در این مجموعه بیش از ۵/ ۲ برابر شده است. همچنین در این سالها ارتقای تکنولوژی و تجهیزات در این مجموعه مدنظر بوده و اجرایی شده است. همانگونه که مستحضر هستید فولاد خوزستان صادرکننده نمونه کشور بهشمار میرود که محصولاتش در بیش از ۲۰ کشور دنیا خریدار دارد. شرکت فولاد خوزستان در سال ۹۷ بیش از ۷۰ درصد تولیدات خود را به بازارهای جهانی صادر کرد؛ محصولی که قدرت رقابت با سایر رقبای خارجی را به لحاظ کیفیت و قیمت داشت. این موضوع به مفهوم آن است که در این سالها فولاد خوزستان در مسیر صحیح حرکت کرده و گامهای خوبی در مسیر ارتقا و توسعه شرکت برداشته شده است.
همچنین به گواه آمار ظرف این سالها با اقدامات انجامشده، میزان مصرف انرژی ازجمله برق در این مجموعه کاهش پیدا کرده است. در زمینه افزایش ایمنی و مسائل زیستمحیطی نیز اقدامات خوبی در مجموعه به اجرا درآمده است. در کنار موارد بیانشده ظرف سالهای اخیر تکمیل زنجیره تولید تبدیل به یکی از اهداف اصلی شرکت شد و در همین راستا نیز فولاد خوزستان به بخش ابتدایی زنجیره یعنی معدن ورود پیدا کرد؛ با سرمایهگذاری شرکت در معدن ظرف این مدت از چالشهای فولاد خوزستان در تامین بلندمدت مواد اولیه کاسته شد.
تمامی موارد بیانشده بیانگر آن است که فولاد خوزستان ظرف سالهای گذشته در مسیر ارتقای بهرهوری حرکت کرده اما این موضوع به این مفهوم نیست که در حال حاضر این مجموعه بزرگ فولادی، شرکتی صددرصد بهرهور بهشمار میرود. قطعاً این امکان وجود داشت که در این سالها تلاش بیشتری انجام شود و نتایج به مراتب بهتری نیز برای این شرکت به دست آید. در این شرایط باید در سالهای آینده بهتر عمل شود تا فولاد خوزستان بتواند سهم خود را در بازارهای جهانی حفظ کند و برند فولاد خوزستان که برندی معتبر در دنیاست، همچنان اعتبار خود را در بازارهای جهانی داشته باشد.
رشد نامتوازن زنجیره، بلای جان صنعتگران
در حال حاضر تامین پایدار مواد اولیه یکی از معضلات اصلی زنجیره تولید فولاد کشور به شمار میرود. برای تحقق تولید ۵۵ میلیون تن فولاد در افق ۱۴۰۴ به حدود ۱۵۰ تا ۱۶۰ میلیون تن سنگ آهن در سال نیاز است که همه متخصصان به اتفاق قول معتقدند که کشور در تامین این میزان سنگآهن دچار چالش میشود. بنابراین برای تامین پایدار سنگ آهن به عنوان ماده اولیه اصلی تولید فولاد در کشور چالشی اساسی وجود دارد و حل این چالش نیاز به اقدامی ویژه دارد.
متاسفانه حتی در حال حاضر نیز یکی از دغدغههای اصلی فولادسازان در پایان سال گرفتن سهمیه سنگ آهن برای تولید سال بعد خود است؛ شاید تا به حال این موضوع باعث نشده تولید در یک مجموعه فولادی متوقف شود اما به رشد بهای نامتعارف سنگ آهن انجامیده است. تا حدود هشت سال قبل سنگ آهن بهایی برابر با ۱۰ درصد شمش فولاد خوزستان داشت اما در حال حاضر نرخ این ماده اولیه به بیش از ۱۶ درصد شمش فولاد خوزستان رسیده و این رشد قیمتی بیانگر چالش صنعت فولاد در تامین مواد اولیه اصلی خود است. این چالش در این سالها به میزانی جدی شده که فولادسازان چارهای جز حرکت به سمت معدنداری با هدف تامین پایدار مواد اولیه نداشتهاند. فولاد خوزستان نیز از این قاعده مستثنی نبود و در حال حاضر بخشی از مواد اولیه مورد نیاز خود را با خرید بخشی از معدن سناباد با ظرفیت تولید سالانه پنج میلیون تن سنگ آهن در سال، تامین میکند. اما حل اساسی چالش تامین سنگ آهن مورد نیاز فولادسازان در سالهای آینده نیاز به سرمایهگذاری قابل توجه در بخش اکتشاف و استخراج معادن دارد.
موضوع دیگر که کمتر به آن پرداخته میشود بحث کیفیت مواد اولیه است؛ زمانی که موضوع کمبود در کالایی به وجود میآید، چارهای جز تامین ماده اولیه با هر کیفیتی باقی نمیماند اما این موضوع به شدت از بهرهوری تولید میکاهد. در واقع رشد نامتوازن زنجیره تولید به افت بهرهوری در انتهای زنجیره تولید میانجامد.
بازنگری دولت و فولادسازان در تامین و مصرف انرژی
صنعت فولاد، صنعتی انرژیبر است و بنابراین قابلیت دسترسی به انرژی و قیمت آن در سوددهی و بهرهوری فولادسازان به عنوان بنگاههای اقتصادی نقش اساسی دارد. انرژی را باید در سه بخش آب، برق و گاز به شکل جداگانه مورد بررسی قرار داد. با وجودی که فولادسازی صنعتی آببر محسوب میشود اما متاسفانه بسیاری از واحدهای فولادی کشور در محلهایی احداث شدهاند که با بحران کمآبی درگیر هستند و همین موضوع تبدیل به چالشی برای این صنعت شده است. این در حالی است که تامین پایدار آب یکی از مواردی است که در طرحهای توجیه اقتصادی برای آغاز یک پروژه مورد توجه قرار میگیرد اما به دلایل مختلف در بسیاری از طرحهای فولادی کشور به این موضوع مهم بیتوجهی شده است. همین موضوع و چالشهای آن نیز باعث شده تا امروز طرحهایی پرهزینه همانند شیرینسازی و انتقال آب خلیج فارس به مناطق مرکزی کشور اجرایی شود. اگرچه با توجه به وجود انرژی ارزان و در دسترس این روش تامین آب در شرایط کنونی، تولید فولاد را برای مجموعههای واقع در مناطق مرکزی کشور فاقد توجیه اقتصادی نمیکند اما اگر قرار باشد تولید فولاد در کشور براساس قیمت مشابه انرژی در دنیا انجام شود، محصول تولیدی این واحدها قدرت رقابت قیمتی خود در بازارهای جهانی را از دست میدهد.
برق نیز از دیگر مواردی است که تاثیری بسزا در استمرار تولید فولادسازان دارد اما همواره در تابستان این صنعت از بابت کمبود در تامین، توزیع و انتقال برق دچار زیان میشود. توسعه صنعت فولاد کشور بدون تامین زیرساختهای انرژی همانند برق و گاز امکانپذیر نیست. با وجود این امسال فولادسازان علاوه بر چالش تامین برق در تابستان در فصل زمستان نیز با مشکل تامین برق روبهرو شدند. تا به حال، شرکت فولاد خوزستان تولید بالغبر ۱۷۰ هزار تن شمش فولاد را تنها به دلیل عدم تامین برق از دست داده است. این در حالی است که اگر برق شرکت تامین میشد، تولید این میزان شمش و صادرات آن میتوانست ارزآوری قابل توجهی برای کشور داشته باشد.
با وجودی که یکی از مزایای صنایع ایران برخورداری از گاز فراوان و ارزان کشور برشمرده میشود اما صنایع کشور حتی در این زمینه نیز با چالش روبهرو هستند و در زمستان به دلیل پیک مصرف خانگی، صنایع با قطعی گاز روبهرو میشوند که این موضوع خسارت زیادی را به آنها تحمیل میکند.
بنابراین برای بهرهور کردن صنعت فولاد کشور نیاز به چارهاندیشی اساسی در بحث تامین انرژی شامل آب، برق و گاز است و لزوم توجه به این موضوع با توجه به نزدیکی به سال ۱۴۰۴ اهمیتی بیشتر پیدا میکند. بخشی از این موضوع بر عهده سیاستگذاران و خارج از حیطه کار صنعت فولاد است اما صنعت فولاد نیز باید برای تصحیح الگوی مصرف انرژی خود اقدامات مهمی انجام دهد.
متاسفانه دسترسی به انرژی ارزان در کشور باعث شده صنایع کشور کمتر به فکر سرمایهگذاری بر روی پروژههایی باشند که به کاهش مصرف انرژی و درواقع بهرهور کردن آن میانجامد، اما اگر قیمت حاملهای انرژی در کشور به بهای حاملهای انرژی در دنیا نزدیک شود یا تنها بهای حاملهای انرژی افزایش یابد، همانگونه که امسال نیز بحثهایی برای افزایش بهای انرژی در سال بعد مطرح شد، سوددهی شرکتها دچار چالش میشود. هرچند در نهایت مجلس شورای اسلامی با این طرح پیشنهادی موافقت نکرد اما صنعت فولاد باید از هماکنون برای بهینهسازی مصرف انرژی خود چارهاندیشی کند تا در آینده با تغییر قیمت حاملهای انرژی دچار چالش نشود.
نکته پایانی
ایجاد توازن در طرح جامع فولاد برای افزایش بهرهوری این صنعت ضروری است. البته کارگروههایی برای برنامهریزی در جهت ایجاد توازن در این طرح شکل گرفته و مشغول به کار هستند اما لازم است که این کارگروهها فعالتر شوند و کار خود را به شکل گستردهتر و پویاتری اجرایی کنند. همچنین لازم است که گستره فعالیت هر شرکتی در این زنجیره از ابتدا تا انتها و چگونگی تامین مواد اولیه مشخص شود تا بخشهای میانی زنجیره دائماً در نگرانی تامین مواد اولیه نباشند.
همچنین لازم است که مجموعههای فولادی برای بهبود مصارف خود اقدامی جدی انجام دهند که به افزایش بهرهوری آنها در این موارد بینجامد. هرچند با توجه به ارائه یارانه به بخش انرژی و دسترسی واحدهای صنعتی به انرژی ارزان در حال حاضر کمتر به این موضوع توجه میشود، اما در ادامه این امر میتواند به یکی از چالشهای آینده صنعت فولاد بدل شود.
نکته مورد اهمیت بعدی در افزایش بهرهوری یک مجموعه فولادی مقیاس تولید است. فولاد خوزستان ظرف سالهای گذشته به این موضوع توجه داشته و اجرای طرحهای توسعهای که به افزایش ظرفیت مجموعه منجر شده نیز در همین راستا بوده است. اما بسیاری از شرکتهای کوچک از این موضوع غفلت کردهاند. این در حالی است که مجموعههای با ظرفیت کم توان رقابت در بازارهای بینالمللی را ندارند. در حال حاضر تولید در مجموعههای فولادی با ظرفیت تولید سالانه کمتر از ۵/ ۱ میلیون تن محصول دیگر مقرون بهصرفه نیست اما متاسفانه بسیاری از تولیدکنندگان فولاد کشور بهخصوص در میان تولیدکنندگان فولادهای ساختمانی ظرفیتی کمتر از این میزان دارند و برای حفظ تولید خود در آینده باید از هماکنون به فکر چارهاندیشی باشند. همانگونه که عنوان شد براساس طرح جامع فولاد باید میزان تولید فولاد کشور در سال ۱۴۰۴ به ۵۵ میلیون تن محصول در سال برسد که تمامی این فولاد در بازار داخل مصرف نخواهد شد و حداقل باید ۱۵ میلیون تن آن صادر شود. اما صادرات موضوعی بلندمدت بوده و نیاز به برنامهریزی دارد. مجموعههای فولادی کوچک و غیراستاندارد فعال در کشور طبیعتاً جایگاهی در بازار صادراتی نمیتوانند داشته باشند. اگر این مجموعهها درصدد بهبود وضعیت خود برنیایند در سالهای آینده با مشکل روبهرو میشوند. در حال حاضر نیز برخورداری از مواد اولیه و انرژی ارزان است که باعث شده این تولیدکنندگان بتوانند سودآور بوده و به فعالیت خود ادامه دهند.
نکته مورد اهمیت بعدی حرکت به سمت تولید فولادهای با ارزش افزوده بالاتر در کشور است که این موضوع باید در دستور کار فعالان این صنعت قرار گیرد. درواقع کیفیت نیز همانند کمیت دارای اهمیت بوده و باید مورد توجه باشد. تولید محصولات نهایی با کیفیت بیشتر میتواند سودآوری بیشتر در عین مصرف کمتر انرژی را برای یک مجموعه به دنبال داشته باشد. در کنار تمامی موارد بیانشده باید در عین توجه به حلقههای زنجیره تولید فولاد، به صنایع جانبی این زنجیره نیز توجه داشت. درواقع برای داشتن صنعت فولاد قوی لازم است که مجموعههای تولید نسوز، فروآلیاژ، آهک، دولومیت و... قدرتمندی در کشور شکل بگیرند؛ همچنین باید کمک کرد تا تمامی این صنایع بارور و توانمند شده تا در آینده چرخه فولاد کشور بتواند در بازار رقابتی دنیا حضوری موفق داشته باشد. در عین حال بهروزرسانی تجهیزات و تکنولوژی نیز باید مورد توجه باشد که به تفصیل به اهمیت این موضوع پرداخته شد.