ارزش افزوده شش میلیارد ریالی در خط برش سنگین واحد تکمیل نورد گرم
دنیای اقتصاد: با اجرای یک پروژه در ناحیه نورد گرم فولاد مبارکه بطور میانگین در هرسال ۶ میلیارد ریال ارزش افزوده حاصل شد. علیرضا پژوهنده کارشناس برق و ابزار دقیق از ارزش افزوده ۶ میلیارد ریالی در خط برش سنگین واحد ۵۲ ناحیه نورد گرم فولاد مبارکه خبر داد و افزود: پس از اجرای پروژه جایگزینی سیستم دارای سنسور لیزری بجای رول میژرینگ و پالس ژنراتور قیچی برش سنگین خط HG ، با کاهش ورقهای قراضه و پکهای NC۱ وNC۲ ناشی ازمغایرت طول ورق، طی یکسال اجرای این سیستم، شرایط بهبود بازدهی وزنی تولید و کاهش حدود ۳۵۰ تن قراضه، افزایش تولید، کاهش توقفات تولید و تعمیرات، کاهش هزینههای تعمیراتی، کاهش مصرف قطعات یدکی و افزایش سوددهی نسبت به یکسال قبل فراهم شد.
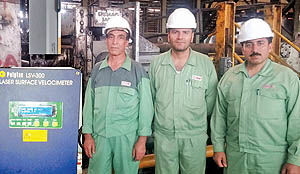
دنیای اقتصاد: با اجرای یک پروژه در ناحیه نورد گرم فولاد مبارکه بطور میانگین در هرسال 6 میلیارد ریال ارزش افزوده حاصل شد. علیرضا پژوهنده کارشناس برق و ابزار دقیق از ارزش افزوده 6 میلیارد ریالی در خط برش سنگین واحد 52 ناحیه نورد گرم فولاد مبارکه خبر داد و افزود: پس از اجرای پروژه جایگزینی سیستم دارای سنسور لیزری بجای رول میژرینگ و پالس ژنراتور قیچی برش سنگین خط HG ، با کاهش ورقهای قراضه و پکهای NC1 وNC2 ناشی ازمغایرت طول ورق، طی یکسال اجرای این سیستم، شرایط بهبود بازدهی وزنی تولید و کاهش حدود 350 تن قراضه، افزایش تولید، کاهش توقفات تولید و تعمیرات، کاهش هزینههای تعمیراتی، کاهش مصرف قطعات یدکی و افزایش سوددهی نسبت به یکسال قبل فراهم شد.
وی در تشریح فرایند تولید در این خط برش گفت: در خط برش سنگین طبق درخواست مشتری ورق از ضخامت 6 تا 16میلیمتر در طول های مختلف ( از 1تا 12 متر) برش داده می شود و پس از انجام اصلاحات، در قسمت پایلر، بسته بندی و ارسال می گردد. برای انجام عملیات برش، بطور همزمان با حرکت طولی ورق، قیچی طی زمانی حرکت کرده و سرعت خود را با ورق یکسان نموده و سریعاً ورق را برش داده که برای انجام این مراحل رول اندازه گیر، روی ورق قرار گرفته و سرعت حرکت ورق را توسط پالس ژنراتور به سیستم کنترل اعمال کرده تا پس از اینکه سرعت حرکت قیچی با سرعت حرکت ورق یکسان شد،
برش داده شود.
پژوهنده در رابطه با اشکالهای سیستم برش قبلی اظهار داشت: این سیستم چون همیشه با ورق در تماس بود به دلایلضربه های ورق، وجود آلودگی روی ورقو شوکهای ناشی از موج و لوپ ورق، تغییرات قطر رول اندازه گیر، اشکال در اتصالات الکتریکی و همچنین اشکال در قسمتهای مکانیکی مربوط به حرکتهای عمودی سیستم که باعث گیر کردن ورق زیر تیغه قیچی، خرابی مکرر تیغه های قیچی که موارد فوق منجر به اختلال در طول ورق و قراضه شدن ورقها (مخصوصاً ورقهایی که دارای طول و عرض و ضخامت حداکثر بوده که وزن هر ورق بیشتر از ۱ تن می باشد) و همچنین توقفات تولید، کاهش تولید، افزایش مصرف قطعات یدکی، عدم ایمنی پرسنل تعمیرات در زمان رفع عیب بطور دائم سیستم را دچار مشکل می کرد.
این کارشناس برق و ابزار دقیق در خصوص چگونگی جایگزینی این سیستم و رفع اشکالات فوق گفت: با بررسی در کارخانجات تولید فولاد در ایران و کشورهای تولید کننده ورق و با توجه به شرایط برش دراین خط تولید که بتواند در یک زمان طول ورق، سرعت ورق، حرکت درجهت های مثبت و منفی ورق تا حداکثر سرعت نامی خط و همچنین حرکتهای ناخواسته برگشت ورق، موجهای ورق و رمپ سرعتهای خط در زمان توقف و راه اندازی مجدد خط توسط اپراتور را اندازه گیری نماید، پیشنهاد تغییر سیستم به سنسور لیزری (غیر تماسی) داده شد. به همین منظور با همکاری واحد طرحهای بهینه سازی ISC و شرکت الکترونیک پیشتاز سپاهان، سنسور لیزری مذکور پس از تأیید جایگزین گردید.
وی قابلیت تنظیم تعداد پالسها، دقت اندازه گیری طول ورق با خطای کمتر از ۱ درصد در میلیمتر، امکان اندازه گیری طول ورق در سرعتهای مختلف (مثبت و منفی، ۰ تا ۲۵۰۰ متر بر دقیقه)، ایجاد فاصله با ورق تا حدود ۱۰۰۰ میلیمتر، مشاهده سرعت خط، امکان اتصال با PLC وHMI از طریق پورت RS۲۳۲ ، قابلیت اعمال ولتاژهای ۵ تا ۱۱۰ولتDC و ۱۱۰ تا ۲۴۰ ولت AC، نگهداری مقدار اندازه گیری شده در حافظه در زمان قطع برق، امکان شمارش تعداد شیتهای بریده شده، درصورت انجام آموزش، امکان کالیبره کردن در داخل کشور، و افزایش ایمنی تجهیزات و نیروی انسانی را از دیگر مزایای سیستم جدید برشمرد.
علیرضا پژوهنده در خاتمه از همکاری اعضای کمیته EIG وپشتیبانی مدیریت ناحیه نوردگرم، مسئولین وکلیه همکاران تولید و تعمیرات در واحد ۵۲، دفتر فنی واحد، گروه فنی و مالی ناحیه، واحد طرحهای بهینهسازیISC و شرکت مجری (الکترونیک پیشتاز سپاهان) تشکر و قدردانی نمود.
وی در تشریح فرایند تولید در این خط برش گفت: در خط برش سنگین طبق درخواست مشتری ورق از ضخامت 6 تا 16میلیمتر در طول های مختلف ( از 1تا 12 متر) برش داده می شود و پس از انجام اصلاحات، در قسمت پایلر، بسته بندی و ارسال می گردد. برای انجام عملیات برش، بطور همزمان با حرکت طولی ورق، قیچی طی زمانی حرکت کرده و سرعت خود را با ورق یکسان نموده و سریعاً ورق را برش داده که برای انجام این مراحل رول اندازه گیر، روی ورق قرار گرفته و سرعت حرکت ورق را توسط پالس ژنراتور به سیستم کنترل اعمال کرده تا پس از اینکه سرعت حرکت قیچی با سرعت حرکت ورق یکسان شد،
برش داده شود.
پژوهنده در رابطه با اشکالهای سیستم برش قبلی اظهار داشت: این سیستم چون همیشه با ورق در تماس بود به دلایلضربه های ورق، وجود آلودگی روی ورقو شوکهای ناشی از موج و لوپ ورق، تغییرات قطر رول اندازه گیر، اشکال در اتصالات الکتریکی و همچنین اشکال در قسمتهای مکانیکی مربوط به حرکتهای عمودی سیستم که باعث گیر کردن ورق زیر تیغه قیچی، خرابی مکرر تیغه های قیچی که موارد فوق منجر به اختلال در طول ورق و قراضه شدن ورقها (مخصوصاً ورقهایی که دارای طول و عرض و ضخامت حداکثر بوده که وزن هر ورق بیشتر از ۱ تن می باشد) و همچنین توقفات تولید، کاهش تولید، افزایش مصرف قطعات یدکی، عدم ایمنی پرسنل تعمیرات در زمان رفع عیب بطور دائم سیستم را دچار مشکل می کرد.
این کارشناس برق و ابزار دقیق در خصوص چگونگی جایگزینی این سیستم و رفع اشکالات فوق گفت: با بررسی در کارخانجات تولید فولاد در ایران و کشورهای تولید کننده ورق و با توجه به شرایط برش دراین خط تولید که بتواند در یک زمان طول ورق، سرعت ورق، حرکت درجهت های مثبت و منفی ورق تا حداکثر سرعت نامی خط و همچنین حرکتهای ناخواسته برگشت ورق، موجهای ورق و رمپ سرعتهای خط در زمان توقف و راه اندازی مجدد خط توسط اپراتور را اندازه گیری نماید، پیشنهاد تغییر سیستم به سنسور لیزری (غیر تماسی) داده شد. به همین منظور با همکاری واحد طرحهای بهینه سازی ISC و شرکت الکترونیک پیشتاز سپاهان، سنسور لیزری مذکور پس از تأیید جایگزین گردید.
وی قابلیت تنظیم تعداد پالسها، دقت اندازه گیری طول ورق با خطای کمتر از ۱ درصد در میلیمتر، امکان اندازه گیری طول ورق در سرعتهای مختلف (مثبت و منفی، ۰ تا ۲۵۰۰ متر بر دقیقه)، ایجاد فاصله با ورق تا حدود ۱۰۰۰ میلیمتر، مشاهده سرعت خط، امکان اتصال با PLC وHMI از طریق پورت RS۲۳۲ ، قابلیت اعمال ولتاژهای ۵ تا ۱۱۰ولتDC و ۱۱۰ تا ۲۴۰ ولت AC، نگهداری مقدار اندازه گیری شده در حافظه در زمان قطع برق، امکان شمارش تعداد شیتهای بریده شده، درصورت انجام آموزش، امکان کالیبره کردن در داخل کشور، و افزایش ایمنی تجهیزات و نیروی انسانی را از دیگر مزایای سیستم جدید برشمرد.
علیرضا پژوهنده در خاتمه از همکاری اعضای کمیته EIG وپشتیبانی مدیریت ناحیه نوردگرم، مسئولین وکلیه همکاران تولید و تعمیرات در واحد ۵۲، دفتر فنی واحد، گروه فنی و مالی ناحیه، واحد طرحهای بهینهسازیISC و شرکت مجری (الکترونیک پیشتاز سپاهان) تشکر و قدردانی نمود.
ارسال نظر