دایرهالمعارف مدیریت- گذار از فوردیسم به پسافوردیسم
تفاوت فلسفه تولید جنرال موتورزو تویوتا
در بخشهای پیش گفته شد که مدیریت آمریکایی با گسترش سیستم تولید انبوه به صنایع مختلف توانست موفقیت بینظیری را در بازارهای جهانی کسب کند؛ اما به طور همزمان برخی شرکتهای ژاپنی شیوه دیگری را در مدیریت به کار میگرفتند که تولید انعطافپذیر نامیده شد. در این بخش سایر ویژگیهای بدل تولید ژاپنی برشمرده خواهد شد.
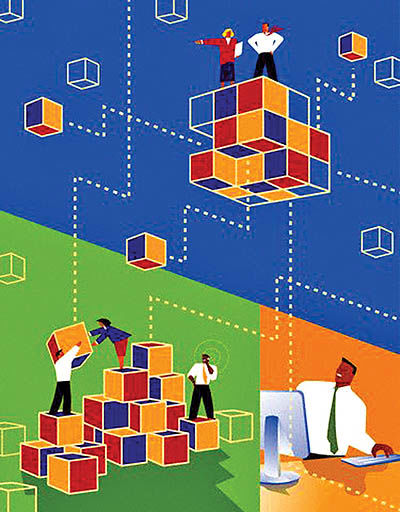
بخش پنجم
در بخشهای پیش گفته شد که مدیریت آمریکایی با گسترش سیستم تولید انبوه به صنایع مختلف توانست موفقیت بینظیری را در بازارهای جهانی کسب کند؛ اما به طور همزمان برخی شرکتهای ژاپنی شیوه دیگری را در مدیریت به کار میگرفتند که تولید انعطافپذیر نامیده شد. در این بخش سایر ویژگیهای بدل تولید ژاپنی برشمرده خواهد شد.
مدل تولید ژاپنیها همچنین اولویت بالایی برای تولید «به موقع» و تولید بدون انبار محصولات قائل است. این ایده در بازدیدی که تایچی اونو از تویوتا موتورز در دهه ۱۹۵۰ از ایالات متحده کرد، به ذهنش خطور نمود. اونو بیشتر تحت تاثیر سوپرمارکتهای عظیم آمریکا قرار گرفت تا کارخانههای اتومبیلسازی آن. او بعدها تعجب خود را از سرعت و کارآیی سوپرمارکتها در انبار کردن میزان دقیقی از کالاها که مورد نیاز مشتریان میباشد، بیان کرد: «سوپرمارکت جایی است که در آن مشتری میتواند (۱) آنچه که نیاز دارد (۲) در زمان مورد نیاز (۳) و به مقدار مورد نیاز بیابد... ما امید داشتیم که این موضوع به هدف ما در تولید به موقع یاری رساند. ما عملا در سال ۱۹۵۳ این سیستم را در کارگاههای ماشینسازی و کارخانه اصلی خود به کار بستیم.» وماک، جونز و رووس از دیدن تفاوت در ظاهر فیزیکی کارخانههای جنرال موتورز در فرامینگهام ماساچوست با کارخانه تویوتا در ژاپن شگفتزده شدند. در کارخانه جنرال موتورز، بخشی از خط تولید خوابیده بود و کارگران این طرف و آن طرف میلولیدند بدون آنکه کاری انجام دهند، محصول تولید یک هفته در گوشه و کنار راهروها انبار شده بود و سطح آشغالها پر از قطعات معیوب بود. در تقابلی شدید، راهروهای کارخانه تویوتا خالی بود و «کارگران تماما سر کار خود مشغول انجام وظایف خویش بودند.
در هیچ بخشی بیش از یک ساعت محصول تولیدی جمع نمیشد. به محض اینکه قطعه معیوبی پیدا میشد، فورا آن را از ماشین باز میکردند و برای تعویض به مرکز کنترل کیفیت میفرستادند.»
فلسفه صنایع تولیدی آمریکایی متکی به تولید «موردی» است. تولیدکنندگان اتومبیل مواد و ابزار مازاد بر احتیاج را در کنار خط تولید انبار میکنند تا در صورت نیاز جایگزین قطعات معیوب یا افزارهای خراب شوند. مدیریت ژاپنیها این فرآیند را هم هزینهبر و هم غیرضروری میداند. سیستم تولید به موقع ژاپنی متکی بر دقیق کردن استانداردهای کنترل کیفیت و طراحی مدیریت بحران برای جستوجوی مسائل بالقوه است قبل از آن که در فرآیند تولید نقصان عمدهای به وجود آید.
تفاوت چشمگیر در فلسفه تولید در جنرال موتوز و تویوتا در ارقام مربوط به عملکرد فنی هر دو شرکت خود را نشان داده است. در پژوهشی که موسسه تکنولوژی ماساچوست از هر دو شرکت انجام داد، پژوهشگران پی بردند که در کارخانه تویوتا «هر وسیله اتومبیل در شانزده ساعت در مساحتی به اندازه ۸/۴ فوت مربع ساخته میشود و عیبها و نقصها سالانه ۴۵/۰ اتومبیل است.
در جنرال موتورز فرامینگهام هر اتومبیل حدود سیویک ساعت در مساحتی به اندازه ۱۵/۸ فوت مربع ساخته میشود و سالانه حدود ۳/۱ اتومبیل معیوب تولید میشود.» تویوتا قادر به تولید سریعتر اتومبیل در فضایی کمتر و با خرابی کمتر و نصف نیروی کار لازم بود.
در سالهای اخیر، تولیدکنندگان ژاپنی تکنیکهای مدیریت انعطافپذیر را با کامپیوترهای پیچیده و سایر تکنولوژیهای اطلاعاتی ترکیب کردهاند تا «کارخانه آینده» را خلق کنند: تجهیزات خودکار تولیدی با کارگران کمتر که بیشتر شبیه به آزمایشگاه خواهد بود تا کارخانه. دانشمندان اجتماعی، مارتین کنی و ریچارد فلوریدا، از کارخانههای انعطافپذیر سخن میگویند که نمود آن بیشتر ذهنی است تا فیزیکی: «در اشکال قدیمی تولید صنعتی که تولید انبوه نظام فوردیستی را نیز شامل میشود، بخش اعظم کار فیزیکی بود... ظهور سیستمهای دیجیتالی اهمیت هوش انتزاعی را در تولید افزایش میدهد. این امر مستلزم آن است که کارگران کارهایی را که قبلا بهعنوان فعالیتهای ذهنی شمرده میشد، بر عهده بگیرند. در این شرایط جدید، کارگران آغشته به روغن و گریس نیستند بلکه کارخانه به نحو فزآیندهای شبیه آزمایشگاهی جهت آزمایش و پیشرفت فنی میگردد.»
پیشفرضهای عملیاتی مدیریت انعطافپذیر با تاکید شدید آن بر «فرآیند» به جای تاکید بر «ساختار و عملکرد»، تولیدکنندگان ژاپنی را در موقعیتی ایدهآل برای بهره بردن از تکنولوژی جدید اطلاعاتی متکی بر کامپیوتر قرارداده است.
منبع: پاپان «کار»، ترجمه حسن مرتضوی، انتشارات آمه
ارسال نظر