سناریوی تولید ۴۰ میلیون تن فولاد چگونه محقق میشود
دو راهکار اساسی برای افزایش ظرفیت تولید فولاد
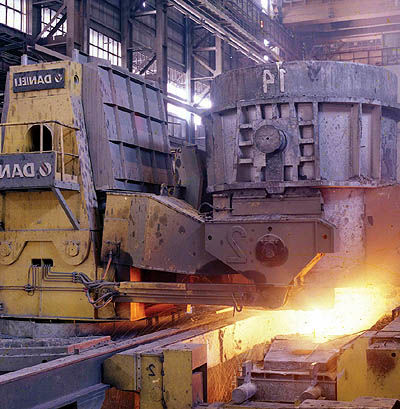
طبق آن مقرر شده تا سال ۱۴۰۰ شمسی میزان تولید فولاد در کشورمان مجموعا به ۴۰میلیون تن برسد؛ این در حالی است که در حال حاضر حدود ۱۴میلیون تن فولاد توسط بخش دولتی و خصوصی
هر دو با هم تولید میشود، لذا نظرات کارشناسی متفاوتی برای افزایش تولید فولاد و ظرفیتسازی در این بخش وجود دارد که در گزارش ذیل دو راهکار برای افزایش ظرفیت تولید فولاد ارائه شده است.
بررسی راهکارها جهت افزایش تولید فولاد در کشور
جهت تولید فولاد، دو راه حل کلی پیش روی ما است. یکی انتخاب کوره بلند و تبدیل سنگ آهن به فولاد و دیگری احیای مستقیم سنگآهن و تبدیل آهناسفنجی به فولاد.
با وجود منابع عظیم گاز و همچنین عدم خودکفایی در زمینه تولید کک متالورژیکی و وارداتی بودن آن و همچنین سرمایهگذاری بسیار زیادی که واحدهای کوره بلند نیاز دارند، تولید فولاد از این طریق را از موضوع بحث خارج میکنیم. این در حالی است که حدود
دو سوم فولاد دنیا از این طریق تولید میشود و به عنوان مثال، چیـــن که بزرگترین تولیدکننده فولاد جهان است، با سرمایهگذاریهای عظیم در این زمینه و با برنامهریزی دقیقی توانسته است رشد حیرتآوری در زمینه فولاد داشته باشد. با اینحال چین و دیگر کشورها دارای ذخایر زغالسنگ کک شو بوده و قیاس آنها با ایران چندان صحیح به نظر نمیرسد. چنانچه قبلا هم ذکر شد، این موضوع همچنین احتمالا، مبنای سیاستگذاریهای شرکت ملی فولاد نیز بوده است. در نتیجه برای افزایش ظرفیت تولید فولاد کشور، باید راه حل دوم یعنی استفاده از روش احیای مستقیم و کورههای الکتریکی مد نظر قرار گیرد.
جهت افزایش تولید فولاد در ایران، با هدف دستیابی به اهداف سناریوی شرکت ملی فولاد جهت تولید بیش از ۴۰میلیون تن فولاد در سال ۱۴۰۰، در اینجا دو پیشنهاد را مورد بررسی قرار میدهیم.
لازم به ذکر است که این پیشنهادات ارتباطی با طرحهای استانی نداشته و صرفا راهکارهایی جهت استفاده در طرحهای بعدی شرکت ملی فولاد، دیگر مراکز تصمیمگیر و بخش خصوصی بوده که امید است مورد توجه مدیران این صنعت کشور قرار گیرد. پیشنهادات ارائه شده در این قسمت ارزش بررسی بیشتر کارشناسان بخش دولتی و خصوصی را دارند.
به طور کلی یکی از راههای پیشرفت و توسعه، الگوبرداری از کشورهای موفق میباشد. لذا در خصوص تولید فولاد نیز جهت نیل به هدف افزایش تولید آن، میتوان با الگوبرداری از آن کشورها از قبیل هندوستان، ترکیه، چین و غیره، در این زمینه راهحلهای مناسب برای ایران را برگزید.
یکی از پیشنهاداتی که در این قسمت مورد بررسی قرار میگیرد، استفاده از تکنولوژیهای روز دنیا، جهت تولید آهناسفنجی در ظرفیتهای پایین و سپس تولید فولاد خام در کورههای الکتریکی و دیگری راهی است که کشور هندوستان آن را پیموده است.
روشهای جدید احیای مستقیم
امروزه، 60درصد از فولاد مصرفی در بخش خودروسازی، فولادی است که در کمتر از پنج سال پیش اختراع شده است. این موضوع نشانگر اهمیت پیشرفتها و تغییرات سریع تکنولوژیکی در عرصه فولاد است.
یکی از این پیشرفتهای تکنولوژیکی در این عرصه، تولید آهناسفنجی در مقیاسهای کوچک و با استفاده از گاز است.
با توجه به آنکه شرکتهای داخلی دارای لیسانس شرکت میدرکس بوده و توان ساخت واحدهای احیای مستقیم با ظرفیت 800هزار تن در سال را دارند، چنین به نظر میرسد که انتخاب ظرفیت 800هزار تن برای واحدهای تولید فولاد استانی، بر اساس توانمندی این شرکتها انتخاب شده است. با وجود بررسیها و جستوجوهای فراوان، علت دیگری برای این مقوله یافت نشد.
به هر حال آنچه مسلم است، تکنولوژی تولید یکی از عوامل مشخصکننده ظرفیت تولیــد است، چنانچه احتمالا در طرحهای استانی نیز ملاک همین موضوع بوده است.
جهت استفاده از گاز طبیعی به عنوان ماده احیاکننده سنگآهن در فرآیند احیای مستقیم، راه حل دیگری که به غیر از روش میدرکس برای تولید وجود دارد، استفاده از میکرو مادولهایی است که استفاده از آنها در دنیا شروع شده است و حتی کشورهای عربی همسایه ایران نیز در حال سرمایهگذاری در این بخش هستند.
از اصلیترین خصوصیات این مادولهای کوچک، امکان تولید آهناسفنجی در ظرفیتهای پایین، حتی ۲۰۰هزار تن در سال است. محصول این فرآیند، با محصولی که از فرآیند میدرکس به دست میآید تفاوتی نداشته، امکان ساخت فولادهای کیفی و نیز محصولات فولادی تخت را نیز میدهد.
همچنین در این فرآیند به ریفرمر نیازی نبوده و درجه متالیزاسیون آهناسفنجی حداقل 93درصد خواهد بود.
از خصوصیات دیگر این روش در مقایسه با روش میدرکس، میتوان به موارد ذیل اشاره کرد:
- کیفیت بالاتر محصولات
- میزان کربن بیشتر در محصول (آهناسفنجی) در حدود ۲ تا ۵درصد
- امکان استفاده از آهناسفنجی داغ به طور مستقیم در کورههای قوس الکتریکی
- انعطافپذیری در استفاده از سنگآهنهای مختلف با عیارهای متفاوت
- درجه متالیزاسیون بالاتر
- هزینههای تولید کمتر
- عدم محدودیت در استفاده از گازهای طبیعی با مشخصات متفاوت
- اثرات کمتر بر محیط زیست.
همچنین با توجه به عدم نیاز این فرآیند به ریفرمر، میتوان به مزیتهای آن به شرح ذیل اشاره نمود:
- اشغال فضای کمتر کارخانه به علت نداشتن ریفرمر
- استفاده مستقیم از گازطبیعی در
Shaft Furnace
- امکان استفاده از گازطبیعی با سولفور بالا
- افزایش کربن در محصول
- هزینه کمتر به علت عدم استفاده از ریفرمر.
بررسی فنی بیشتر این میکرومادولها که توسط شرکت Tenova HYL در حال توسعه هستند، ارزش بررسی توسط کارشناسان را دارد.
جهت مقایسه این روش با روش موجــود در ایــران، در اینجا به بررسی شاخــصهای مالــی واحد تولید آهناسفنجی به کمک یک میـکرومادول 200هزار تن در سال، همراه با یک خط ذوب و ریختهگری با استفاده از کورههای قوس الکتریکی میپردازیم.
با وجود آنکه بخش خصوصی میتواند به همراه استفاده از این میکرومادولها از کورههای القایی نیز استفاده کند، دلیل انتخاب کوره قوس در اینجا نشان دادن جذابیت این طرح با وجود هزینه بالاتر کورههای قوس الکتریکی است.
طبق اطلاعات به دست آمده از شرکت HYL، هزینههای ارزی تجهیزات واحد میکرومادول حدود 40میلیون دلار و هزینههای ریالی آن حدود 10میلیارد تومان است. در مجموع با احتساب کلیه هزینههای کارهای عمرانی (زمیــن، ساختــمانها، محـوطهسازی و غیره)، تجهیزات جانبی، نصب و راهاندازی و غیره، هزینه راهاندازی طرح به 60میلیون دلار و 30میلیارد تومان بالغ میشود.
با در نظر گرفتن شارژ ۸۰درصد آهناسفنجی همراه با ۲۰درصد قراضه آهن و نیز هزینه تبدیلی برابر با یک واحد میدرکس و راهاندازی ۲ ساله طرح، نتایج بررسیها به شرح جدول ذیل است. همانطور که از جدول پیدا است، این طرح نیز جذابیت بالایی جهت جذب سرمایهگذاریهای بخش خصوصی دارد و لازم است مورد توجه بیشتر مدیران قرار گیرد.
ارسال نظر