«دنیای اقتصاد» شیوههای کاهش هزینههای تولید در صنعت فولاد را بررسی کرد
دوئل برسر قیمت تمام شده در صنعت فولاد
محمدحسین بابالو : دستیابی به ظرفیت تولید ۵۵میلیون تن فولاد خام در افق ۱۴۰۴ یکی از مهمترین اهداف پیشبینی شده در برنامههای بالادستی نظام در حوزه صنعت است که با توجه به پذیرفتن آن توسط نهادهای مختلف تصمیمساز اقتصادی، هماکنون کشور در مسیر ایجاد زیرساختهای آن گام برمیدارد. سرمایهگذاری در معادن سنگآهن، تولید کنسانتره و گندله، ایجاد زیرساختهای موردنیاز در حملونقل، بارگیری و تخلیه همچنین بررسی برای کشف و حتی بازار مصرف داخلی و صادراتی، هماکنون مواردی است که در دستور کار قرار گرفته است.
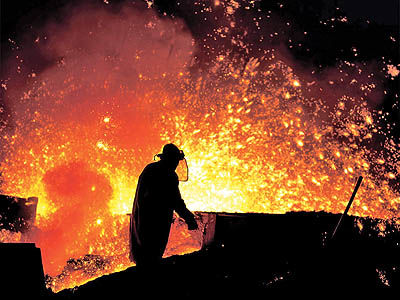
محمدحسین بابالو : دستیابی به ظرفیت تولید ۵۵میلیون تن فولاد خام در افق ۱۴۰۴ یکی از مهمترین اهداف پیشبینی شده در برنامههای بالادستی نظام در حوزه صنعت است که با توجه به پذیرفتن آن توسط نهادهای مختلف تصمیمساز اقتصادی، هماکنون کشور در مسیر ایجاد زیرساختهای آن گام برمیدارد. سرمایهگذاری در معادن سنگآهن، تولید کنسانتره و گندله، ایجاد زیرساختهای موردنیاز در حملونقل، بارگیری و تخلیه همچنین بررسی برای کشف و حتی بازار مصرف داخلی و صادراتی، هماکنون مواردی است که در دستور کار قرار گرفته است. در مقابل این رویکرد بالادستی، بسیاری از کارشناسان در بخشهای مختلف نسبت به اتخاذ این تصمیم، موضعی انتقادی به خود گرفتهاند یا چنین تصمیمی را غیرکارشناسی دانسته یا برنامهریزیهای نیل به این هدف را جامع، علمی و فراگیر نمیدانند. تجربه ۸ طرح فولادی که از دولت قبل آغاز شده و بخشهای محدودی از آن به مرحله اجرای واقعی رسیده است را میتوان دلایل متقنی بر غیرکارشناسی بودن این تصمیم به شمار آورد ولی این تمام ماجرا نیست.
نگاهی به وضعیت جهانی صنعت فولاد نشان میدهد کشورهای مهم و مهد تولید فولاد، هیچکدام از تولید این کالا عقبنشینی کامل نکردهاند یعنی کارخانههای جدید بهصورت مداوم احداث شده ولی از طرف مقابل، بسیاری از کارخانههای قدیمیتر یا توقف فعالیت داشته یا حتی تخریب شدهاند. نگاهی به آمارهای انجمن جهانی فولاد World Steel Association نشان میدهد در کنار رشد محدود حجم تولید، ضریب استفاده از ظرفیت نصب شده نیز در حال افزایش است. به عبارت سادهتر با وجود افزایش ظرفیت تولید در اقصی نقاط جهان، هماکنون از کارخانههای فولادی استفاده بیشتری به نسبت قبل صورت میگیرد که این رشد استفاده از ظرفیت نصب شده به واحدهای جدید بازمیگردد؛ یعنی کارخانههای قدیمیتر بسته شده و کارخانههای جدید با حداکثر توان کار میکنند. در نهایت خروجی این رخداد را باید در کاهش هزینه تولید کل جستوجو کرد. با توجه به همین واقعیتهای جهانی در کنار کاهش رشد تقاضای جهانی فولاد و شائبه دامپینگ که تقریبا تمام مجامع فولادی در مورد آن صحبت میکنند، باید کاهش قیمت تمامشده تولیدات به شیوههای مختلف را شاه کلید آینده این بازار به شمار آورد. البته در آخرین گزارش انجمن جهانی فولاد استفاده از ضریب نصب شده کاهش یافته است. توجه به همین نکته در تحلیل واقعیتهای فولادی کشورمان در مورد هدفگذاری تولید ۵۵ میلیون تن فولاد خام در افق ۱۴۰۴ میتواند رویکردهای آتی بررسیها را تشکیل دهد.
کاهش قیمت تمامشده تولیدات نکتهای نیست که بتوان از کنار آن ساده عبور کرد زیرا آینده بازار رقابتی فولاد به گونهای تولیدکنندگان را تحت فشار قرار خواهد داد که حتی یک دلار یا چند سنت قیمت تمام شده پایینتر، خود میتواند با افزایش قدرت چانهزنی تولیدکننده، سهم بازار بیشتری را بهدست آورده و جایگاه خود را تقویت کند. تجربه نشان داده است که چند واقعیت مغفول در صنعت فولاد بزرگترین تاثیرات را بر قیمت تمام شده و حتی امکانپذیری احداث آنها گذارده است. مکانیابی نامناسب، عدم توجه به وجود زیرساختهای مورد نظر همچون آب و راهآهن، فاصله با بنادر و آبهای آزاد مخصوصا آبهای اقیانوسی، تاثیرات زیستمحیطی و تغییرات اقلیم منطقهای، امکانپذیری تامین مواد اولیه و حتی حاملهای انرژی و وجود یا نبود تکنولوژیهای بومی و بازار مصرف مواردی است که توجیهپذیری احداث واحدهای جدید فولادی را با تردید مواجه میکند.
باید به صراحت عنوان داشت که بسیاری از واحدهای برنامهریزی شده فعلی غالب ویژگیهای موردنیاز را نداشته و اگر هم احداث شود در آینده در رقابت با سایرین به مشکلات بزرگی برخواهد خورد که باز هم حمایت دولتی را طلب خواهد کرد. با توجه به برخی واقعیتها شاید پافشاری بر یک اشتباه خود اشتباه بزرگتری باشد که در آینده هزینههای بیشتری را به کشور تحمیل خواهد کرد. به احتمال قوی در صورت احداث واحدهای بدون توجیه اقتصادی با محوریت احیای مستقیم، در آینده تولیدکنندگان مواد اولیه یا شرکتهای حملونقل یا سایر شرکتهای دولتی و حتی خصولتیها باید بار این کارخانهها را به دوش بکشند.
باز هم باید به کاهش قیمت تمام شده اشاره کنیم که البته بخش بزرگی از این هزینهها را میتوان در سرمایهگذاریهای اولیه جستوجو کرد. در فرآیند احیای مستقیم و به دلایل فنی باید در ابتدا سنگآهن دانهبندی شده به کنسانتره، گندله، آهن اسفنجی و نهایتا به کمک ذوب در کوره قوس الکتریکی در کنار آهن قراضه، به فولاد خام تبدیل شود. همین فرآیند در کنار مباحث مربوط به تکنولوژی مخصوص کشورهایی همچون ایران، هند و کشورهای حاشیه خلیج فارس است که از ذخایر بالای گاز برخوردار بوده یا همچون هند از احیای مستقیم به کمک زغالسنگ حرارتی استفاده میکنند.
به صراحت باید به این نکته اشاره کرد که مهمترین دلیل توجه تصمیمسازان اقتصادی به مکانیزمهای تولید فولاد خام به روش احیای مستقیم، یکی وجود ذخایر عظیم گاز طبیعی و دیگری نگرانیها از تامین زغالسنگ کک شو بوده که به نوعی بدبینی را به شیوههای تولید فولاد خام به روش احیای غیرمستقیم یا همان کوره بلند ایجاد کرده است. البته با توجه به ویژگیهای فنی استخراج زغالسنگ در کشور بهرغم ذخایر عظیم آن، ضخامت پایین لایهها، توالی لایهبندی با ضخامتهای پایین در کنار عمق و شیب لایهها، وجود ناخالصیها و مواد فرار، عدم وجود پتانسیلهایی قدرتمند برای استخراج مکانیزه زغالسنگ به استثنای منطقه پرودهطبس و بسیاری دیگر از واقعیتهای این عرصه، خوشبینی به زغالسنگ در قبل از انقلاب به بدبینی نسبت به آن منجر شد که یکی از مهمترین خروجیهای این واقعیت را باید عدم توسعه جدی کارخانه ذوبآهن در سالهای گذشته به نسبت سایر کارخانههای مشابه و مخصوصا شیوههای احیای مستقیم دانست.
البته بدبینی نسبت به زغالسنگ شاید واقعیت داشته باشد ولی حقیقت این ذخایر نیست زیرا ویژگیهای فنی و مغفول بسیاری وجود دارد که از یکسو جایگاه یک مهندس معدن را در زنجیره تحقیقات فولاد برجسته ساخته (هرچند که هماکنون این جایگاه به اندازه کافی به مهندسان معدن تفویض نشده است) و از سوی دیگر میتواند بخشی از این بدبینی را شاید برای همیشه جبران کند. در سادهترین تقسیمبندیهای زغالسنگ، این حامل انرژی را به دو دسته اصلی و ساده تقسیم میکنیم؛ زغالسنگ حرارتی و زغالسنگ ککشو. زغالسنگ حرارتی موسوم به آنتراسیت از یکسو عمر بیشتری را سپری کرده و از سوی دیگر ارزش حرارتی بیشتری نیز دارد. این در حالی است که این کالا برخلاف زغالسنگ ککشو، دیگر نیازی به تحمیل فرآیند ککسازی نداشته و پس از استخراج و احتمالا زغالشویی، میتوان از زغالسنگ حرارتی بهصورت مستقیم در کوره استفاده کرد. این شرایط باعث شده تا از این کالای ارزشمند بیشتر بهصورت مستقیم استفاده شود یعنی از آن برای تولید انرژی الکتریکی و گاهی تولید سیمان بهرهبرداری شود.
هرچند که قابلیت مکانیزه کردن معادن زغالسنگ در ایران محدود است و آن معادنی که چنین پتانسیلی را داشته، تاکنون در حد توان خود فرآیندهای مکانیزه شدن را تجربه کردهاند ولی بازهم ذخایر زغالسنگ ایران نقاط مغفول بزرگی دارد. بهعنوان مثال میتوان از ذخایر زغالسنگ حرارتی در منطقه مزینوی طبس نام برد که با وجود ۴/ ۱ میلیارد تن ذخیره، هماکنون جزو چند معدن کوچک، بهرهبرداری گستردهای در آن صورت نگرفته و شاید توسعه این معدن نیز همپای احداث نیروگاه زغالسنگ حرارتی در طبس، یک گام به پیش و دو گام به پس باشد.
نکته مهمی که معدن مزینوی طبس را شاید از تمامی ذخایر ایران متمایز میسازد باید در ویژگیهای زمینشناسی آن دانست زیرا این حوزه زمینشناسی در کنار منطقه پروده، در یک حوزه طاقدیس شکل قرار گرفته و با توجه به ویژگیهای زمینشناسی طاقدیسها، لایههای زغالدار از اعماق زمین به سطح آمده و البته فرسایش طبیعی نیز بخش اعظم باطلهبرداری را خود انجام داده است. به عبارت سادهتر لایههای زغالدار مزینو هماکنون در عمق مطلوبی قرار داشته و قابلیت استخراج روباز را دارد، هرچند که مدتی است که چند معدن بخش خصوصی بهصورت روباز و بهوسیله باطلهبرداری سطحی، این ذخایر را استخراج میکنند.
با توجه به توالی لایهها و همچنین با فرض استفاده از کارخانه زغالشویی، میتوان ذخایر عظیمی از زغالسنگ حرارتی این منطقه را به سادگی استخراج کرد که این منطقه خاص زمین شناسی را به نسبت سایر نقاط ایران متمایز ساخته است. به نظر میرسد این ویژگی مهم از دید بسیاری از کارشناسان این عرصه مغفول باقی مانده ولی برخی رفتارها از سوی برخی از شرکتهای فنی با رویکرد حرفهای در هفتهها و ماههای اخیر نشان میدهد که گویی به دادههایی مغفول دست یافتهاند هرچند که بررسیهای فنی دقیقا به منظور دست یافتن به این واقعیتها صورت میپذیرد. در نهایت باید به این نکته به صراحت اشاره داشت که با توجه به پایین بودن سرمایهگذاری اولیه برای تولید فولاد خام برپایه زغالسنگ مخصوصا انواع حرارتی آن که از یکسو به تولید گندله نیاز نداشته و از سوی دیگر فرآیند ککسازی نیز حذف میشود، میتوان به کاهش هزینه تولید فولاد در این شیوه امیدوار بود هرچند که برخی اما و اگرهای فنی را نیز نمیتوان نادیده گرفت.
پایین بودن تجربههای عملی در کشور و حتی در سایر کشورهای جهان، نیاز به سرمایهگذاری بخشهای دولتی و خصوصی بر پایه منابع داخلی، ناآشنا بودن تکنولوژیهای تولیدی، ترس از راندمان پایین و حتی عدم موفقیت در تولید و مواردی از این قبیل، میتواند نقاط ضعف سرمایهگذاری در این عرصه جدید باشد. البته باید به این نکته نیز اشاره داشت که سرمایهگذار خارجی قطعا بیهوده به گدار نمیزند و تا از موفقیت طرحی مطمئن نباشد، نسبت به سرمایهگذاری آنها در کشوری دیگری اقدام نخواهد کرد. در خبرها آمده است که پوسکو در حال حاضر یک خط ۶/ ۱ میلیون تنی تولید فولاد خام را در چابهار به روش فاینکس در دستور کار دارد و در حال برنامهریزی برای آغاز این پروژه است.
تکنولوژی فاینکس یعنی استفاده از زغالسنگ حرارتی در فرآیند فولادسازی و امکان مصرف نرمه سنگآهن یا سنگ آهنریزدانه و توان استفاده از سنگ آهن با عیار پایین توانسته است امکان صرفهجویی قابل ملاحظهای در تولید فولاد نسبت به روشهای موجود ایجاد کند. البته باید به این نکته نیز اشاره داشت که اگر قصد بر خرید ماشینآلات و احداث کارخانهای بر پایه منابع مالی داخلی است باید به شدت نگران کارآیی این سیستم بود، زیرا موارد فنی یا توجیهات اقتصادی هرچقدر هم که قوی باشد باز هم نمیتواند از کارخانهای مدرن، فولاد تولید کند، زیرا ویژگیهای شیمیایی عنصر آهن مخصوصا میل به ترکیب بسیار بالای آن ممکن است بسیاری از شیوهها را با عدم کارآیی روبهرو سازد. رخدادی که بارها تجربه شده و ممکن است باز هم تجربه شود.
پس از تکنولوژی فاینکس، استفاده از کورههای دوار با تکنولوژی SL/ RN را میتوان در دستور کار قرار داد، هرچند که اولین واحد با این تکنولوژی به زودی آغاز به کار خواهد کرد. روش SL/ RN روشی است که در آن آهن اسفنجی در کوره افقی دوار با شیب حدود ۵ درجه و با استفاده از زغال بهعنوان عامل حرارتی تولید میشود. در این روش سنگآهن، آهک یا دولومیت وارد کوره گردان شده و در دمایی حدود ۹۰۰ تا ۱۱۰۰ درجه سلسیوس در طول کوره احیا میشود. آهن اسفنجی تولید شده با دمای ۱۰۰۰ درجه سلسیوس پس از خروج از کوره گردان مستقیم یا غیرمستقیم به وسیله آب در محفظههای گردان سرد شده و عناصر احیا نشده در آن از طریق روشهای مغناطیسی حذف میشود. با افتتاح و راهاندازی واحد احیای مجتمع در آینده نزدیک فولاد کویر دامغان اولین شرکتی خواهد بود که از روش SL/ RN برای احیای سنگآهن استفاده خواهد کرد.
ارسال نظر