با سرمایهگذاری ۲۵۰۰ میلیارد ریالی توسط شرکت تولید روی ایران:
عملیات احداث بزرگترین کارخانه تولید روی خاورمیانه آغاز شد
از ۲۳۳ معدن روی شناخته شده در دنیا، ۱۰۸ معدن در منطقه آسیا-اقیانوسیه قرار گرفته است.
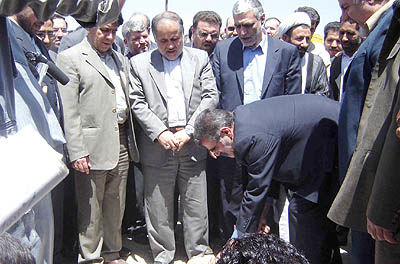
از ۲۳۳ معدن روی شناخته شده در دنیا، ۱۰۸ معدن در منطقه آسیا-اقیانوسیه قرار گرفته است.
از این تعداد، سهم ایران با بیش از 2درصد ذخیره روی جهان، چندین معدن بزرگ و کوچک میباشد که در این بین معادن سرب و روی انگوران (زنجان) و مهدیآباد (یزد) نسبت به معادن عمارت (اراک)، کوشک (بافق) و گوشفیل (اصفهان) شناختهشدهتر میباشد.
با اینکه میزان ذخیره انگوران نسبت به مهدیآباد بسیار کمتر است، اما اختلاف عیار این دو معدن، انگوران را متمایز کرده است.
عیار متوسط روی در خاک انگوران در حدود 28درصد و تقریبا بیش از هفت برابر عیار معدن مهدیآباد است.
کلا معدن سرب و روی انگوران به لحاظ نوع ترکیبات کانههای روی (که عمدتا اکسیده میباشند) و همچنین میزان روی محتوی، یکی از معادن مهم روی در جهان محسوب میشود.
استخراج این معدن براساس نتایج اکتشافات اولیه که نشاندهنده توده کوچکی از ذخیره معدنی بود از سال 1325 به روش زیرزمینی آغاز شد.
در سال ۱۳۵۲ و پس از مشخص شدن حجم واقعی این توده معدنی در مطالعات و عملیات اکتشافی صورت گرفته، استخراج از آن
به صورت روباز (Open Pit) آغاز شد که تاکنون نیز ادامه دارد.
وجود این ذخیره معدنی باعث ایجاد انگیزه مناسبی جهت برنامهریزی و سرمایهگذاری در زمینه تولید فلز روی شد.
تاریخچه احداث کارخانه تولید شمش روی در ایران
اولین مطالعات به عمل آمده در مورد احداث کارخانه تولید شمش روی با استفاده از خاک معدن انگوران پیش از انقلاب اسلامی و توسط بخش خصوصی (سرمایهگذاران شرکت کالسیمین) آغاز گردید که با توجه به وضعیت بازار و شرایط اقتصادی ناتمام ماند.
در سال 1360 و با تاسیس شرکت ملی سرب و روی ایران، مجددا تولید شمش روی مورد توجه قرار گرفت که نهایتا پس از کارشکنیهای فراوان توسط پیمانکاران خارجی، کارخانه 15000 تنی تولید شمش روی این شرکت به دست کارشناسان داخلی احداث گردید. این اقدام براساس تجربه موفقی بود که طی آن در سال 1376، کارخانه 7000 تنی تولید شمش روی دندی (متعلق به شرکت کالسیمین که بعدها ظرفیت آن به 14هزار تن افزایش یافت) با استفاده از روش هیدرومتالورژی و کنسانتره معدن انگوران به عنوان اولین تولیدکننده شمش روی در ایران طراحی، احداث و راهاندازی شد، پس از آن 26 واحد تولیدی بزرگ و کوچک دیگر احداث شد که از آن میان میتوان به کارخانجات ذوب و روی بافق (30هزار تن در سال)، ذوب و احیای روی قشم (20هزار تن در سال)، فرآوری مواد معدنی ایران (15هزار تن در سال) و ذوب روی بندرعباس (13هزار تن در سال) اشاره کرد.
احداث کارخانجات یکصدهزار تنی تولید شمش روی
در سال 1375 و با توجه به افزایش ارزش فلز روی در بازارهای جهانی و همچنین استعداد بالقوه کشور در زمینه تولید این فلز، هیات دولت تولید یکصدهزار تن شمش روی را تصویب و نهایتا در قالب برنامه دوم توسعه به تصویب مجلس شورای اسلامی نیز رسید.
در سال 1376 شرکت توسعه معادن روی ایران به منظور ایجاد این ظرفیت تولیدی و با سرمایهگذاری مردم تاسیس شد.
این شرکت پس از تعیین ظرفیت و فناوری مورد استفاده، خوراک مورد نیاز، بررسی بازار، مکانیابی طرح و انجام مطالعات امکانسنجی در سال ۱۳۷۷ در سه مقطع زمانی (۱۳۷۸، ۱۳۷۹ و ۱۳۸۰) نسبت به عقد قرارداد احداث کارخانه با پیمانکاران معتبر خارجی اقدام کرد که هیچ کدام به علت فراهم نشدن امکانات جذب سرمایهگذاری خارجی در بخش خصوصی اجرایی نشد.
لذا در دیماه سال 1381، به پیشنهاد آن شرکت و با تایید سازمان توسعه و نوسازی معادن و صنایع معدنی ایران، شرکت تولید روی ایران تاسیس شد.
شرکت توسعه معادن روی ایران که حدود ۸۰درصد سهام این شرکت را در اختیار دارد، تولیدکننده ۸۰درصد شمش روی و ۱۰۰درصد شمش سرب کشور میباشد.
سازمان توسعه و نوسازی معادن و صنایع معدنی ایران نیز که 20درصد سهام این شرکت را در اختیار دارد، سیاستگذاری فعالیتهای معدنی و صنایع معدنی کشور را بر عهده دارد.
با چنین پشتوانهای، تاسیس این شرکت با هدف استفاده از توانمندیهای بخش خصوصی متخصص توام با حمایتهای فنی و تخصصی دولت در راستای احداث کارخانجات یکصدهزار تنی تولید شمش روی انگوران صورت پذیرفت.
جایگاه کشور در تولید روی قبل و بعد از راهاندازی واحد یکصدهزار تنی
در حال حاضر با تولید حدود ۱۲۵هزار تن در سال، ایران در جایگاه ۲۲ جهان قرار دارد. با توجه به طرحهای در دست اجرا توسط کشورهای دیگر، پیشبینی میشود با راهاندازی طرح در سال ۱۳۸۹، کشور در جایگاه ۱۵ الی ۱۷ جهان قرار گیرد.
اقدامات انجام شده توسط شرکت تولید روی ایران جهت اجرای طرح
پس از طراحی مفهومی و انجام مطالعات امکانسنجی فنی و اقتصادی، پیمانکار اجرای طرح به صورت EPC از طریق برگزاری مناقصه بینالمللی انتخاب و قرارداد کلید گردان در خردادماه ۱۳۸۳ با برنده مناقصه منعقد شد.
مشکلات پیش آمده در تامین منابع مالی قرارداد با استفاده از منابع میانمدت کارگزاران خارجی (Buyer Credit Finance)، مانع از اجرایی شدن قرارداد مذکور شد.
در حال حاضر پس از تعیین محل اجرای طرح، انجام مطالعات فنی (زیستمحیطی، ژئوتکنیکی و...) در خصوص محل و اخذ مجوزهای مربوطه از سازمانها و ادارات ذیمدخل، اجرای طرح با استفاده از حداکثر توان متخصصان داخلی و استفاده از کارشناسان مجرب پرورش یافته در گروه شرکتهای توسعه معادن روی ایران در دستور کار قرار گرفت.
بر این اساس طراحی و احداث زیرساختها به دست مشاوران و پیمانکاران داخلی را آغاز کردهایم.
همچنین به منظور انتخاب طراح پایه کارخانه، مطالعات اولیه توسط مشاور مادر طرح (شرکت مهندسان مشاور آسه صنعت) آغاز شده است.
مشخصات کارخانجات یکصد هزار تنی تولید شمش روی انگوران
* مساحت زمین* 140 هکتار
* محصول اصلی* شمش روی با ظرفیت یکصد هزار (۱۰۰۰۰۰) تن در سال
* محصول جانبی
- مواد حاوی سرب (کنسانتره سرب ۵۰درصد) با ظرفیت ۴۹۰۰۰تن در سال
- شمش کادمیوم با ظرفیت 800 تن در سال
* تعداد پرسنل* ۳۷۵نفر
* اشتغالزایی غیرمستقیم* 1500نفر
* انرژی مصرفی در روز*
- برق: 38 مگاوات ساعات
- گاز: ۴۸۰۰۰مترمکعب
- آب: 2400مترمکعب
* مواد مصرفی اصلی (تن در سال)*
- کانه معدنی روی 435000
- اسید سولفوریک ۱۰۰۰۰۰
- آهک 42000
- آهک هیدراته ۲۵۰۰۰
* میزان سرمایهگذاری طرح*
- سرمایه ثابت به میزان ۱۴۶۶
میلیارد ریال و 5/91میلیون یورو، جمعا معادل 2519میلیارد ریال
- هزینههای قبل از راهاندازی به میزان ۹/۶۵میلیارد ریال و ۱۶میلیون یورو جمعا معادل ۲۵۰میلیارد ریال
- سرمایه در گردش برای سال اول راهاندازی به میزان 5/377 میلیارد ریال و 911هزار یورو جمعا معادل 388میلیارد ریال
* دوره ساخت* ۴۰ ماه
* قیمت تمام شده هر تن شمش روی*
- قیمت تمام شده بدون استهلاک و بهره فاینانس: ۴/۹میلیون ریال معادل ۸۱۷یورو به ازای هر تن
- قیمت تمام شده با استهلاک و بهره فاینانس: 15میلیون ریال معادل 1267یورو به ازای هر تن
* هزینه تولید کنسانتره سرب نیز در قیمت فوق لحاظ شده است.
هزینههای جاری
* هزینههای جاری بدون در نظر گرفتن استهلاک و بهره فاینانس و با در نظر گرفتن هزینه فروش ۹۱۶۶۶۹میلیون ریال و ۲۱۵۴هزار یورو (معادل ۹۴۱۴۷۴میلیون ریال) میباشد.
* هزینههای جاری با در نظر گرفتن استهلاک و بهره بانکی 1195331میلیون ریال و 26588هزار یورو (معادل 1501573میلیون ریال) میباشد.
تولید روی به روش هیدرومتالورژی
امروزه استخراج و تولید فلز روی از کانههای سولفیدی و اکسیده به روش هیدرومتالورژی در مقایسه با روشهای قدیمی پیرومتالورژی دارای اولویت میباشد. در حال حاضر بیش از 80درصد از شمش روی در جهان به روش الکترولیتی (هیدرومتالورژی) تولید میشود.
در این روش به جای استفاده از روشهای حرارتی، با استفاده از یک حلال مناسب در مرحله فروشویی (Leach)، عناصر موجود در کانههای معدنی به صورت محلول در میآیند. محتوای فلز مورد نظر پس از گذر از مرحله تصفیه (Purification)، به خاطر حذف ناخالصیها، افزایش یافته و نهایتا در مرحله الکترووینینگ و با استفاده از جریان مستقیم برق، این فلز از محلول تصفیه شده به ورقههای فلزی (کاتد) منتقل میشود.
با توجه به مزیتهای چشمگیر روشهای هیدرومتالورژی نسبت به روشهای قدیمی پیرومتالورژی (سرمایهگذاری اولیه، مصرف انرژی و اثرات و زیانهای زیست محیطی در این روش به مراتب کمتر بوده، ضمن آنکه قابلیت بهرهگیری از منابع با عیارها و ناخالصیهای مختلف بیشتر و محصول نهایی از درجه خلوص بالاتری برخوردار میباشد) اقدامات زیادی در زمینه بهبود و توسعه این روش به کار گرفته شده است.
تولید روی به روش هیدرومتالورژی به سه فرآیند عمده زیر تقسیم میگردد که اساس طراحی مفهومی کارخانجات یکصدهزار تنی را تشکیل میدهند.
۱ - تولید محصول باردار حاوی روی از طریق فروشویی کانه روی (Leach).
2 - خالصسازی محلول باردار حاوی روی (Purification).
۳ - نشاندن روی موجود در محلول خالصسازی شده بر روی ورقههای فلزی با استفاده از جریان برق مستقیم (Electrowinning).
1 -فروشویی Leach
در فرآیند تولید محلول باردار حاوی روی(Pregnant Leach Solutioin) کانه روی در مرحله فروشویی (Leach) در اسید سولفوریک حل و روی موجود در خاک به محلول منتقل میگردد.
با توجه به اینکه اسید سولفوریک برای ترکیبات اکسید روی حلال مناسبی میباشد، در مواردی که خاک ورودی اکسیده نباشد، در ابتدا طی یک فرآیند حرارتی روی را به ترکیبی اکسیده تبدیل نموده و سپس فروشویی انجام میشود.
با توجه به ترکیب خاک معدن انگوران که بخش اصلی آن حاوی کانههای اکسیده روی میباشد، در فرآیند مورد نظر برای احداث کارخانجات یکصدهزار تنی، خاک معدن، بدون استفاده از فرآیندهای حرارتی به صورت مستقیم به مرحله فروشویی وارد میشود. (Direct Leach)، با بهرهگیری از این روش سرمایهگذاری احداث کارخانه بین ۲۰درصد الی ۳۰درصد کاهش مییابد.
در این روش بازیابی فلز روی از کانه بیش از 96درصد میباشد.
۲ - خالصسازی Purification
در فرآیند خالصسازی و با توجه به اینکه اسید سولفوریک ناخالصیهای موجود در خاک را نیز به همراه روی وارد محلول مینماید، تولید محلول حاوی روی با کمترین مقدار ناخالصی مد نظر قرار دارد.
این کار با دو روش قابل انجام است:
الف) روش خالصسازی از طریق ترسیب و سمانتاسیون و یا روش مرسوم (Conventional) که در آن با استفاده از روشهای مختلف از جمله افزودن مواد (از جمله پودر روی) ناخالصیهای مختلف از قبیل کبالت، کادمیوم و... به صورت جانشینی از محلول جدا شده و
به صورت نمک و هیدروکسید فلز تهنشین میشوند.
ب) روش خالصسازی از طریق استخراج با حلال(Solvent Extraction) که در مقایسه با حذف ناخالصیها از محلول در روش قبل، این روش براساس استفاده از خاصیت «جذب انتخابی» برخی از مواد بنا نهاده شده است. در این روش محلول آبی حاوی فلز روی و ناخالصیهای دیگر در تماس با یک محلول آلی قرار میگیرد که حاوی ماده استخراجکننده (Extractant) است. بر اثر همجواری این دو محلول، ماده استخراجکننده، روی را از فاز آبی به فاز آلی منتقل مینماید. در مرحله بعد با انتقال روی از فاز آلی به یک فاز آبی عاری از ناخالصی، عمل خالصسازی پایان مییابد.
نکات قابل ملاحظه در مقایسه این دو روش عبارتند از:
2 -1- روش SX مستلزم واردات D2EHPA (دی -2- اتیل هگزا فسفریک اسید که به عنوان استخراجکننده استفاده میشود) از خارج از کشور میباشد، در حالی که در روش مرسوم مواد وارداتی ناچیز است.
۲ -۲- با عنایت به میزان سازههای مورد نیاز در روش SX حجم سرمایهگذاری در این روش بیش از روش مرسوم است.
2 - 3 - در روش SX ماده استخراج کننده علاوه بر روی، آهن، نیکل و مس را نیز استخراج و به فاز محلول وارد کرده که میتواند در کیفیت محصول موثر باشد.
۲ -۴- وجود مراجع صنعتی متعدد در تولید روی در نقاط مختلف دنیا با روش مرسوم.
2 -5- از نظر هزینههای مربوط به آموزش فنی پرسنل، روش مرسوم با توجه به سابقه تولید روی در ایران ارجح بوده و تعداد زیادی از کارکنان صنعت روی در منطقه زنجان، دارای شناخت کاملی نسبت به این روش میباشند.
۳ - الکترووینینگ Electrowinning
در الکترووینینگ با استفاده از جریان برق مستقیم، محلول خالصسازی شده که در این مرحله الکترولیت نامیده میشود، باردار شده و در نتیجه آن، یونهای فلز روی بر سطح صفحات آلومینیومی کاتد رسوب میکند. بر این اساس و پس از گذشت 48 ساعت، بیشتر روی موجود در الکترولیت بر سطح کاتدها مینشیند. در صورتی که حضور ناخالصیها کمتر از حد مجاز است، خلوص فلز روی میتواند تا مرز 999/99درصد نیز برسد.
پس از این مرحله ورقه فلزی تولید شده به صورت اتوماتیک از دو طرف کاتد جدا و پس از ذوب در کورههای تعبیه شده، توسط ماشین ریختهگری در قالبهای استاندارد ۲۵ کیلوگرمی ریختهگری و آماده ارائه به بازار میشود.
همچنین با توجه به عیار سرب (6درصد) و کادمیوم (22/0درصد) در خاک معدن انگوران، در طراحی مفهومی این کارخانه واحدهای جانبی نیز برای بازیابی سرب و کادمیوم از پسماند واحد فروشویی و تبدیل آن به مواد قابل فروش در بازارهای داخلی و جهانی در نظر گرفته شد. بر این اساس مقرر شد، محصولات جانبی کارخانه شامل مواد حاوی سرب جهت استفاده در کوره کالدو و همچنین کادمیوم اسفنجی (با خلوص 98/99درصد) در اشکال مختلف قابل ارائه به بازار باشد.
ارسال نظر