درسال۹۵
«پتروشیمی امیرکبیر» رکورد تولید را شکست
مجمع عمومی عادی سالانه شرکت پتروشیمی امیرکبیر ۱۲۰۰ ریال سود به ازای هر سهم سال ۹۵ تصویب کرد. در این مجمع که با حضور اکثر سهامداران برگزار شد صورتهای مالی شرکت به تصویب رسید. نجات امینی بهعنوان رئیس، مهدی راعی و محمود مجیب بهعنوان ناظر و فرزان هوشمندان بهعنوان منشی اداره جلسه را بر عهده داشتند. دراین مجمع همچنین شرکت صنعتی نوید زرشیمی، بانک رفاه کارگران، توسعه تجارت رفاه پردیس، توسعه فناوری رفاه پردیس و شرکت ارزشآفرینان تجارت صبا برای مدت دو سال در مجمع مزبور بهعنوان اعضای هیات مدیره جدید شرکت انتخاب شدند.
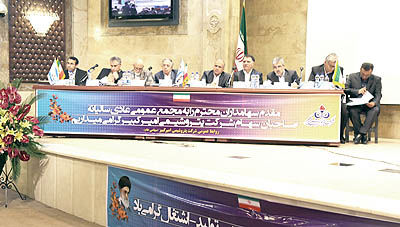
مجمع عمومی عادی سالانه شرکت پتروشیمی امیرکبیر ۱۲۰۰ ریال سود به ازای هر سهم سال ۹۵ تصویب کرد. در این مجمع که با حضور اکثر سهامداران برگزار شد صورتهای مالی شرکت به تصویب رسید. نجات امینی بهعنوان رئیس، مهدی راعی و محمود مجیب بهعنوان ناظر و فرزان هوشمندان بهعنوان منشی اداره جلسه را بر عهده داشتند. دراین مجمع همچنین شرکت صنعتی نوید زرشیمی، بانک رفاه کارگران، توسعه تجارت رفاه پردیس، توسعه فناوری رفاه پردیس و شرکت ارزشآفرینان تجارت صبا برای مدت دو سال در مجمع مزبور بهعنوان اعضای هیات مدیره جدید شرکت انتخاب شدند. براساس تصمیمات این مجمع روزنامههای دنیای اقتصاد و اطلاعات روزنامه کثیرالانتشار شرکت برای سال ۹۶ شدند. همچنین سازمان حسابرسی بهعنوان بازرس قانونی و حسابرس شرکت برگزیده شد.
سرمایه و ترکیب سهامداران
سرمایه شرکت در بدو تاسیس مبلغ ۱۰ میلیون ریال (شامل تعداد ۱۰.۰۰۰ سهم، به ارزش اسمی هر سهم ۱.۰۰۰ ریال) بوده که طی چند مرحله به شرح زیر به مبلغ ۳.۶۰۰ میلیارد ریال (شامل تعداد ۳.۶۰۰ میلیون سهم، به ارزش اسمی هر سهم ۱.۰۰۰ ریال) در پایان سال مالی منتهی به ۲۹/ ۱۲/ ۱۳۹۰ افزایش یافته است.
همچنین ترکیب سهامداران عمده شرکت در پایان سال مالی منتهی به ۳۰/ ۱۲/ ۱۳۹۵ به شرح زیر است.
بانک رفاه کارگران (سهامی عام) با ۸۵/ ۵۱ درصد، شرکت صنعتی نوید زرشیمی با ۰۰/ ۲۰ درصد، شرکت سرمایهگذاری سازمان بازنشستگی کشوری با ۸۵/ ۱۰ درصد، شرکت صادرفر با ۱۹/ ۱۰ درصد، شرکت سرمایهگذاری آتیه صبا با ۹۲/ ۲ درصد، صندوق بازنشستگی کشوری با ۸۲/ ۲ درصد است.گواهینامهها و نشانهای اخذ شده در سال ۱۳۹۵ عبارتند از:
* کسب گواهینامه و تقدیرنامه چهارستاره تعالی از فرآیند جایزه تعالی صنعت پتروشیمی
* دریافت تقدیرنامه دو ستاره جایزه ملی مدیریت مالی ایران
* کسب گواهینامه شاخص فنی و عملکرد انرژی (EPT) برتر از دبیرخانه جایزه ملی مدیریت انرژی
* دریافت سپاسنامه ششمین جشنواره ملی بهرهوری به دلیل ارائه تجربیات موفق ارتقای عملکرد در مجتمع
* تمدید گواهینامههای استاندارد IMS و مدیریت انرژی در سطح مجتمع
عمده فعالیتهای انجام شده در سال ۱۳۹۵ به شرح زیر است:
۱- استفاده از خوراک پروپان بهعنوان خوراک جایگزین که نقش عمدهای در افزایش تولید داشته است.
۲- استفاده از خوراک نفتای شرکت اکسیر برای جبران کسری خوراک مایع
۳- پیگیری تهیه اتیلن از سایر شرکتهای منطقه و خارج از منطقه برای افزایش تولید واحدهای پاییندست
۴- افزایش ۴۶ درصدی دریافت خوراک اتان نسبت به سال قبل
۵- استقرار و راهاندازی سیستم نرمافزاری آزمایشگاهها در سطح مجتمع
۶- استقرار و راهاندازی پروژه CMMS۱
۷- بازنگری در ارکان جهتساز و استراتژیهای سازمان به موازات استقرار و راهاندازی پروژه BI۲
۸- افزایش ۷۱ درصدی EPS شرکت نسبت به سال قبل
۹- راهاندازی سیستم حسابداری صنعتی بهای تمام شده
۱۰- انتقال اتوماتیک نقدینگی شرکت بهصورت روزانه به حساب سپرده برای ایجاد درآمد از طریق دریافت سود
۱۱- تکمیل تعویض کویلها و TLEهای کورهها و نیز تعمیر بسیاری از ادوات کورهها
۱۲- انجام مذاکرات احداث کارخانه NGL۳ و دریافت موافقت اصولی واگذاری آن از وزارت نفت
امیرکبیر در یک نگاه
مقایسه عملکرد سال 95 با عملکرد سال 94
شرکت پتروشیمی امیرکبیر در سال ۹۵ موفق به تولید ۱.۳۴۳.۱۶۶ تن محصول شد که بیشترین تولید از زمان راهاندازی شرکت بوده است که این مقدار افزایش تولید ۳۱ درصدی را نسبت به سال قبل نشان میدهد.
در زمینه دریافت خوراک شرکت موفق به دریافت ۱۳۰.۹۷۰ تن خوراک ارزانقیمت اتان شد که افزایش ۴۶ درصدی را نسبت به سال ۹۴ نشان میدهد.
همچنین خوراکهای مایع نیز نسبت به سال ۹۴ به میزان ۴۳ درصد افزایش یافته و به ۷۶۹.۵۰۹ تن رسید.
فروش کل شرکت از نظر مقداری به میزان ۲۲ درصد نسبت به سال قبل افزایش داشته و به ۸۵۸.۱۵۳ تن رسیده است. از نظر ریالی به میزان ۲۰ درصد نسبت به سال قبل افزایش داشته و به ۲۶.۱۵۰.۰۵۶ میلیون ریال رسیده است.
فروش داخلی شرکت از نظر مقداری به میزان ۲۸ درصد نسبت به سال قبل افزایش داشته و به ۶۵۴.۳۹۸ تن رسیده است. از نظر ریالی به میزان ۲۵ درصد نسبت به سال قبل افزایش داشته و به ۱۷.۶۹۸.۰۷۰ میلیون ریال رسیده است.
فروش صادراتی شرکت از نظر مقداری به میزان ۸ درصد نسبت به سال قبل افزایش داشته و به ۲۰۳.۷۵۵ تن رسیده است. از نظر ریالی به میزان ۱۱ درصد نسبت به سال قبل افزایش داشته و به ۸.۴۵۱.۹۸۶ میلیون ریال رسیده است.
سود عملیاتی شرکت در سال ۹۵ به ۲۶.۱۵۰.۰۵۶ میلیون ریال رسیده است که از ابتدای کار شرکت بیشترین میزان بوده و نسبت به سال ۹۴ به میزان ۲۰ درصد افزایش داشته است.
سود خالص شرکت در سال ۹۵ به ۴.۲۵۵.۱۱۹ میلیون ریال رسیده است که از ابتدای کار شرکت بیشترین میزان بوده و نسبت به سال ۹۴ به میزان ۷۱ درصد افزایش داشته است.
EPS۱ شرکت نیز در سال ۹۵ به ۱.۱۸۲ ریال رسیده است که از ابتدای کار شرکت بیشترین میزان بوده و نسبت به سال ۹۴ به میزان ۷۱ درصد افزایش داشته است.
رخدادهای مهم سال ۱۳۹۵ عبارتند از:
واحدهای بهرهبرداری
واحد الفین
عمده کارهای مهم برای بهبود تولید، HSE۱، تعمیرات و آموزش پرسنل که در سال گذشته انجام شده به شرح زیر است:
۱- ادامه تعمیرات اساسی و تکمیل تعویض کویلها و TLE۲های کورهها و نیز تعمیر بسیاری از ادوات کورهها
۲- آموزش ایمنی کلیه پرسنل برای استقرار سیستم صدور پروانه کار جدید
۳- استفاده از خوراک پروپان بهعنوان خوراک جایگزین که نقش عمدهای در افزایش تولید داشته است.
۴- ایجاد پروژه تحقیقاتی در رابطه با علت افزایش مصرف بخار که نتایج بسیار خوبی از آن حاصل شده است.
۵- نصب رآکتور دوم یونیت ۲۷ برای کاهش COD۳ پساب ارسالی به فجر
۶- مسدود کردن خروجی آبهای سطحی به سمت خوریات به دلیل بالا بودن COD این پسابها و جلوگیری از جرایم سنگین به شرکت
۷- تعمیر مبدلهای E-۲۴۱۱ و E-۲۴۱۲ طبق آخرین متد علمی و با نظارت کامل برای جلوگیری از نشت PFO۴ به Dilution Steam و جلوگیری از افزایش مصرف بخار
۸- همکاری با شرکت لینده آلمان و ایجاد پروژه برای موارد زیر:
الف- مطالعه علل افزایش مصرف بخار در واحد
ب- پروژه تثبیت فشار اتان دریافتی به دلیل نوسانات شدید این خوراک
ج- به حداکثر رساندن مصرف پروپان در واحد
د- کاهش تولید بنزین در پروسه
۹- جذب نیروهای تحصیلکرده و بومی برای واحد و آموزش کامل ایشان طی ۳ ماه از سوی کارشناسان و متخصصان واحد
۱۰- تعمیر مبدلهای A,B,C E-۴۳۱۲ و E-۳۷۱۱ A,C,D بهطور کامل و تعمیر اصولی کپها و Tube Sheet مبدلها برای بازدهی بیشتر و خوردگی کمتر آنها
۱۱- استفاده از خوراک نفتای شرکت اکسیر برای جبران کسری خوراک مایع
۱۲- پیگیری تهیه اتیلن از سایر شرکتهای منطقه و خارج از منطقه برای افزایش تولید واحدهای پاییندست.
واحد بوتن 1
۱- اجرای موفقیتآمیز تست پروژه «هالو سیلان» برای بهبود فرآیند تولید بوتن ۱، کاهش مصرف کاتالیست و مواد شیمیایی که در صورت تهیه مواد شیمیایی صنعتی تست بلندمدت آن اجرا خواهد شد. اجرای این طرح مشترک بر عهده شرکت پژوهش و فناوری پتروشیمی و پتروشیمی امیرکبیر بوده که با اجرای آن علاوه بر کاهش مصرف کاتالیست به میزان ۳۰ درصد و کاهش پلیمر ناخواسته به میزان ۲۰ درصد، در دانش فنی به دست آمده نیز شراکت خواهد داشت.
۲- بهبود کیفیت محصول بهرغم استفاده از کاتالیست ارزانقیمت چینی با تغییر در شرایط پروسسی واحد
۳- بازدید کارشناسان شرکت Axens فرانسه بهعنوان لایسنسور از سایت و برگزاری جلسات فنی با ایشان، بررسی و پیگیری با شرکت Axens برای امکانسنجی جایگزینی تولید هگزن ۱- به جای بوتن ۱- با توجه به بهبود خواص پلیمر تولیدی با هگزن ۱- نسبت به بوتن۱- و سودآوری بالای آن
واحد بوتادین
۱- انجام پروژه تعویض کلیدهای سوییچگیرهای IV برق واحد که پیش از این بارها سبب قطع برق و توقف واحد شده بود.
۲- اصلاح شیب Man Way برج T-۴۰۴۱ برای جلوگیری از ماند بوتادین، تشکیل POP CORN۱ و توقف تولید
۳- نصب Flow meter روی مسیر صادراتی برای پایش میزان محموله صادراتی به کشتی
۴- تهیه پکینگ تاورها از منابع داخلی
۵- RETUBE مبدل E-۴۰۴۱
۶- اجرای پروژه تعویض Gass Detectorهای واحد و در سرویس قرار گرفتن آنها
۷- تعمیر اضطراری خطوط آب آتشنشانی
۸- اجرای پروژه تعویض خطوط آب آتشنشانی (در حال اجرا)
۹- انجام تعمیرات اساسی
۱۰- با کاهش فشارهای سیاسی ناشی از تحریمها، در سال ۹۵ جلساتی با نمایندگان و کارشناسان شرکت BASF در محل واحد برگزار شد که ضمن ارائه گزارشی از مشکلات موجود، به برخی از آنها پاسخ داده و راهحل ارائه شد و برخی دیگر همچون استفاده از مواد شیمیایی جدید ممانعتکننده از تشکیل POP CORN منوط به برگزاری جلسات بیشتر شد.
۱۱- بازدید کارشناسان شرکت KOBELCO ژاپن از سایت بهعنوان سازنده کمپرسورهای C-۱۰۵۳ و C-۳۰۳۱ و اعلام آمادگی برای تامین قطعات و اوورهال آنها
واحد پلیاتیلن سنگین
۱- اجرای تعمیرات اساسی
۲- اجرای TSR۱ مربوط به تغییر چیدمان سیستم بخار ZONEهای ۱۲گانه در بخش ۵۰۰ بهمنظور تسهیل در انجام تعمیرات
۲- بازسازی تعداد ۳۶ عدد از سگمنتهای مربوط به مبدلهای E-۱۰۲۱/ ۲/ ۳
۴- تعویض روتور مربوط به CE-۲۰۱۱ و DR-۵۰۰۱
۵- رفع اشکال از ترانس اکسترودر
۶- ادامه پایش مربوط به کاهش مصرف هگزان
۷- ادامه پایش کاهش مصارف Utility
۸- تعویض تعدادی از تلههای بخار (STEAM TRAP) جهت کاهش مصرف بخار
۹- کاهش مصارف مواد شیمیایی واحد با هدف کنترل بهینه مصارف مواد شیمیایی با اصلاح ضریب تزریق و انجام آزمایشهای تکمیلی برای اطمینان از کیفیت محصول و افزایش ORT۲ و تست ۳۸۰ ساعته
۱۰- کنترل جهت کاهش محصول OFF و اقلام مصرفی بستهبندی با اجرای مداوم سیستم پایشی و نظارتی در بخش بستهبندی
۱۱- رفع اشکال از SB-۸۰۰۱ برای افزایش فشار بخار خروجی تا ۵۰ بار برای تنظیم دمای صفحههای اکسترودر
۱۲- ادامه پروژه مربوط به رفع اشکال از توزینکنندههای SI-۲۰۳۱/ ۲/ ۳-SI-۶۰۰۱/ ۲/ ۳/ ۴-W-۵۰۰۱/ ۲
۱۳- اجرای TSR مربوط به تغییر لاین ورودی پمپهای P-۱۰۲۲A/ B از حالت Reducer Excentric Top Flat به Reducer Excentric Bottom Flat
۱۴- اجرای TSR مربوط به طراحی و ساخت پات در ورودی پمپهای P-۳۰۳۱ A/ B در بخش بوتن ریکاوری
۱۵- اجرای نصب فیلتر و تغییر مسیرهای هوای ابزار دقیق به D-۸۰۰۵ جهت گرفتن ذرات جامد به بخش بستهبندی
واحد پلیاتیلن سبک و سنگین
۱- برگزاری جلسات و تبادل اطلاعات با لایسنسور واحد به منظور تولید گریدهای جدید و بهکارگیری روشهای تولید جدید با تکنولوژی روز
۲- دستیابی به ظرفیت تولید ۳۸ تن بر ساعت با تغییرات اعمالشده در واحد که امیدواریم با رفع موانع موجود در سال جدید تولید پایداری را در این تناژ داشته باشیم.
۳- اوورهال گیربکس مربوط به بخش MELT PUMP اکسترودر برای بار اول از ابتدای راهاندازی
۴- برگشت آب کندانس (LPC): افزایش ۲۰ درصدی به واسطه برگشت کندانسهای دورریز و هدایت آن به شبکه اصلی
۵- کاهش ۱۳ درصدی مصرف بخار به واسطه استفاده از آب گرم تولیدی در فرآیند به بخار مصرفی جهت C-۴۷۰
۶- برق مصرفی: کاهش ۲ تا ۳ درصدی به واسطه استفاده از دستگاه کاهنده برق
واحد پلیاتیلن سبک
۱- ایجاد تغییرات در جریان سیستم خنک کاری رآکتور (Hot Water) و Tuning رآکتور جهت کاهش Fouling در رآکتور و افزایش تولید نزدیک به طراحی در گریدهای مختلف
۲- تولید گریدهای ۲۴۲۰H، ۲۴۲۰D و ۲۴۲۰K طبق نیاز بازار فروش
۳- اجرا و راهاندازی سیستم مانیتورینگ کمپرسورهای فشار بالا برای پایش و عیبیابی دقیق برای جلوگیری از توقفات ناخواسته
۴- استفاده از آب BFW۱ به جای پمپهای P-۱۸۰۵ و P-۱۷۰۸ جهت کاهش هزینههای تعمیراتی و توقف به علت خرابی پمپهای مذکور
۵- ایجاد تغییرات در فرآیند واکسزدایی مبدلهای HP Recycle طبق اسناد لایسنسور در جهت کاهش ورود پلیمر به کمپرسور ثانویه
۶- جایگزینی حلال «ایزودودکان» که از شرکتهای خارجی با قیمت بالا تهیه میشد با حلال نرمال پارافین که در داخل کشور با تفاوت قیمت بسیار با نمونه خارجی تولید میشود. این تغییر در ماده شیمیایی مصرفی با بررسی و ایجاد تغییرات در سیستم خنکسازی موفقیتآمیز بوده و هماکنون در فرآیند مورد استفاده قرار میگیرد.
۷- رفع عیب طراحی سیستم Dryer و ایجاد تغییرات براساس دستور کار اداره محترم خدمات فنی جهت کاهش تولید رشتههای پلیمری و خرابیهای مکرر این تجهیز
۸- ایجاد سیستم پایش و ثبت ضایعات محصول و مواد مصرفی بهصورت روزانه در جهت عارضهیابی و کاهش ضایعات
۹- تست جایگزینی ماده شیمیایی «پروپیون آلدهید» که از شرکتهای خارجی تهیه میشود با پروپیلن تولیدی واحد الفین برای کاهش هزینه مصرف مواد شیمیایی
۱۰- ارائه پیشنهاد استفاده از پالت چوبی به جای پالت پلاستیکی که بالغ بر ۹۰.۰۰۰.۰۰۰.۰۰۰ ریال در سال سودآوری به همراه خواهد داشت و هماکنون مراحل خرید در حال انجام است.
ارسال نظر