بهرهوری از طراحی تا تولید
حسن قرهئی مدیر برنامهریزی استراتژیک سایپا بهرهوری را میتوان «بهدست آوردن حداکثر سود ممکن یا کاهش قیمت تمام شده با استفاده بهینه از عوامل تولید محصول و ارائه خدمت» تعریف کرد. بهرهوری در اصل مفهومی اقتصادی است که در تمام حوزهها قابل رصد است و در صنعت خودرو باید آن را در تمام بخشهای زنجیره ارزش دنبال کرد. چنانچه به نمودار ارزش آفرینی این صنعت توجه کنیم، بیشترین ارزش در بخشهای تحقیق و توسعه، خدمات پس از فروش و کسب و کارهای پس از فروش ایجاد میشود؛ بنابراین جهت ارتقای بهرهوری در این صنعت، باید بر بخشهای نامبرده با اولویت بالاتری تمرکز کرد.
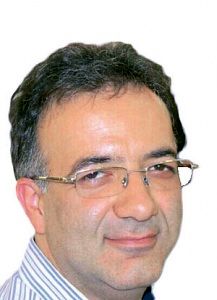
حسن قرهئی مدیر برنامهریزی استراتژیک سایپا بهرهوری را میتوان «بهدست آوردن حداکثر سود ممکن یا کاهش قیمت تمام شده با استفاده بهینه از عوامل تولید محصول و ارائه خدمت» تعریف کرد. بهرهوری در اصل مفهومی اقتصادی است که در تمام حوزهها قابل رصد است و در صنعت خودرو باید آن را در تمام بخشهای زنجیره ارزش دنبال کرد. چنانچه به نمودار ارزش آفرینی این صنعت توجه کنیم، بیشترین ارزش در بخشهای تحقیق و توسعه، خدمات پس از فروش و کسب و کارهای پس از فروش ایجاد میشود؛ بنابراین جهت ارتقای بهرهوری در این صنعت، باید بر بخشهای نامبرده با اولویت بالاتری تمرکز کرد. در این مقاله بهصورت خاص به بهرهوری صنعت خودرو از طراحی تا تولید خودرو میپردازیم.
تحقیق و توسعه (R&D)
تحقیق و توسعه در صنعت خودرو، بهعنوان یکی از مهمترین بخشهای ارزش آفرین، همواره هزینههای بسیاری را به این صنعت تحمیل کرده است؛ بنابراین خودروسازان جهانی برای افزایش بهرهوری در این بخش، به همکاری با یکدیگر روی آوردهاند و از این طریق هزینههای تحقیق و توسعه را به اشتراک گذارده و از توان یکدیگر بهصورت بهینه استفاده میکنند. رنو و نیسان بهعنوان دو غول خودروسازی جهان با اشتراک دانش فنی خود با یکدیگر به طراحی پلتفرمهای مشترک دست زدهاند و هزینههای طراحی پلتفرم که بیشترین هزینه R&D را به خود اختصاص میدهد را تا حدود ۴ میلیارد دلار در سال ۲۰۱۴ کاهش دادهاند؛ بنابراین علاوهبر تولید محصولات متنوع روی یک پلتفرم، تعداد مدلهای تولیدی از یک نوع محصول را نیز توسعه دادهاند بهطور مثال میتوان به پلتفرم V که در ۴ مدل خودروی نیسان و ۷ مدل خودرو رنو مورد استفاده قرار گرفته است، اشاره کرد. همچنین بهعنوان نمونه دیگر میتوان به خرید شرکت خودروسازی کیا توسط شرکت هیوندای و نیز همکاری پژو-سیتروئن اشاره کرد. شرکتهای خودروسازی برای مدیریت هزینههای R&D به توسعه همکاری با شرکتهای قطعهساز میپردازند؛ بنابراین درحالیکه هزینههای R&D در سال ۲۰۰۷، بهصورت ۷۵درصد خودروساز و ۲۵ درصد قطعهساز تقسیم شده بود در سال ۲۰۱۲ بهصورت مساوی تقسیم شد و پیشبینی میشود در سال ۲۰۲۰ خودروسازان ۲۵ درصد و قطعهسازان ۷۵ درصد هزینههای R&D را پرداخت کنند.
تولید و تامین قطعات
شرکتهای قطعهساز رده یک و ۲ با ادغام با یکدیگر یا خرید قطعهسازان کوچکتر توسط قطعهسازهای بزرگ، توانستهاند توان و بهرهوری بالاتری را در عرصه قطعهسازی بهدست آورند بهطوریکه ۲۰ قطعهساز بزرگ جهان در سال ۲۰۰۹ تنها ۳۹ درصد قطعات تولیدی مورد نیاز را تامین میکردند و پیشبینی میشود با استفاده از این استراتژی، صرفهجویی در مقیاسی ایجاد شود که در سال ۲۰۲۵ بتوانند ۷۵درصد قطعات را تامین کنند. قطعهسازانی که در سالهای گذشته بهصورت انحصاری برای هر یک از خودروسازان فعالیت میکردند، هماکنون با استفاده از استراتژیهای یکپارچگی به تامین قطعات تعداد زیادی از شرکتهای خودروساز میپردازند. بهعنوان مثال، ذکر این نکته ضروری است که در سال ۲۰۰۵، ۲۷ خودروساز بزرگ در کنار ۲۵۰۰ قطعهساز فعالیت میکردند و در سال ۲۰۱۰، ۱۹ خودروساز بزرگ در کنار ۷۰۰ قطعهساز فعالیت میکردند. درخصوص همکاری یک قطعهساز با چند خودروساز بهعنوان مثال میتوان به Autoliv بهعنوان تامینکننده ایربگ و Faurecia تامینکننده صندلی برای شرکتهای Audi، BMW، Fiat، Ford، GM Europe و Mercedes/ Smart اشاره کرد.
تولید خودرو
بهرغم تصور عموم مردم از اینکه تولید خودرو سهم عمدهای از سود این صنعت را به خود اختصاص میدهد، نمودار ارزشآفرینی و آمارهای جهانی نشانگر خلاف این موضوع است. تولید خودرو اگرچه پر زحمتترین و پرچالشترین بخش از زنجیره ارزش است، بخش کوچکی از سود این صنعت را منتفع میشود؛ بنابراین بهرهوری در این بخش نیز میتواند نقش زیادی در کاهش هزینهها و افزایش سودآوری ایفا کند. از مهمترین راهکارهای افزایش بهرهوری در این بخش میتوان به موارد زیر اشاره کرد:
- راهاندازی سایتهای تولیدی یا استفاده از سایتهای دیگر خودروسازان جهت کاهش هزینههای لجستیک:
در سال ۱۹۵۰ حدود ۷۵ درصد خودروها در ایالاتمتحده آمریکا تولید میشد و بهدست مصرفکنندگان در کل دنیا میرسید. با توجه به هزینههای حمل و نقل در این فرآیند، شرکتهای خودروساز تصمیم به تاسیس سایت تولیدی در مناطق مختلف جهان (نزدیک به محلهای مصرف) کردهاند. برای مثال در حال حاضر تویوتا دارای ۵۴ سایت تولیدی در ۲۷ کشور و رنو دارای ۳۲ سایت تولیدی در ۱۶ کشور جهان است که در ۲ سایت کشور مغرب و هند خودروهای نیسان نیز تولید میشود.
ارتقای تکنولوژی تولید از طریق جذب سرمایهگذاریهای خارجی (شرکتهای خودروساز جهانی):
این راهکار در کشورهایی مانند هند، چین و کره جنوبی مورد استفاده قرار گرفته و توانسته است سرعت رشد صنعت را تحت تاثیر قرار دهد و به تبع آن بهرهوری را افزایش دهد. بیشک جذب سرمایهگذاریهای خارجی در این کشورها بدون حمایتهای دولتی امکانپذیر نبوده که پرداختن به آن، در این مقال نمیگنجد.
عقد قراردادهای همکاری در تامین قطعات / دریافت خدمات مشترک:
همانگونه که در بخش تولید قطعات، همکاری و ادغام قطعهسازان برای استفاده از توان یکدیگر و ارائه خدمات به دامنه بزرگتری از خودروسازان میتواند موثر واقع شود، خودروسازان نیز میتوانند برای تخصصی تر کردن و ارتقای کیفیت قطعات مورد استفاده در فرآیند تولید، شرکتهایی را در این خصوص تاسیس کنند. شرکت RNPO بهعنوان سازمان خرید رنو و نیسان که از اتحاد استراتژیک این دو شرکت بهوجود آمده است، نمونه موفقی از اجرای این استراتژی به شمار میرود. با توجه به آنچه گفته شد یکی از موثرترین راهکارهای افزایش بهرهوری در صنعت خودرو که در تمامی بخشهای زنجیره ارزش مورد استفاده قرار گرفته است، صرفهجویی در مقیاس با استفاده از توان یکدیگر در قالب تعریف انواع همکاریها اعم از پروژههای مشترک، اتحاد استراتژیک، سرمایهگذاری مشترک، خرید و ادغام یکدیگر هستند؛ بنابراین به نظر میرسد برای افزایش بهرهوری در این صنعت، توسعه همکاری یا ادغام دو خودروساز اصلی در این عرصه (ایرانخودرو و سایپا) مناسب است. همچنین ادغام قطعهسازان کوچکتر با یکدیگر از طریق سرمایهگذاریهای مشترک و ایجاد قطعهسازان قویتر در این عرصه در مرحله اول و جذب سرمایهگذاریهای خارجی (از طریق ایجاد خطوط تولید جدید یا واگذاری سهام قطعهسازان موجود) در مرحله دوم، راهکار مناسبی برای افزایش بهرهوری در بخش تولید قطعات است. همانگونه که گفته شد، جذب سرمایهگذاریهای خارجی نیاز به حمایتهای دولتی در این موضوع دارد که کشورهای برزیل، روسیه، هند، چین و کره جنوبی نمونههای مناسبی برای الگوبرداری هستند. البته در کنار تمام آنچه گفته شد، آموزش و ارتقای نیروی انسانی بهعنوان بزرگترین سرمایههای سازمان در اجرای استراتژیها نباید به فراموشی سپرده شود.
ارسال نظر